Pyrolysis is a thermal decomposition process that requires specific conditions and factors to be optimized for efficient and effective results. The process is influenced by a variety of parameters, including temperature, pressure, residence time, feedstock properties, and reactor design. These factors collectively determine the yield, composition, and quality of the resulting products, such as bio-oil, char, and pyrolytic gas. Understanding these requirements is essential for optimizing the pyrolysis process, whether for waste management, energy production, or material recovery.
Key Points Explained:
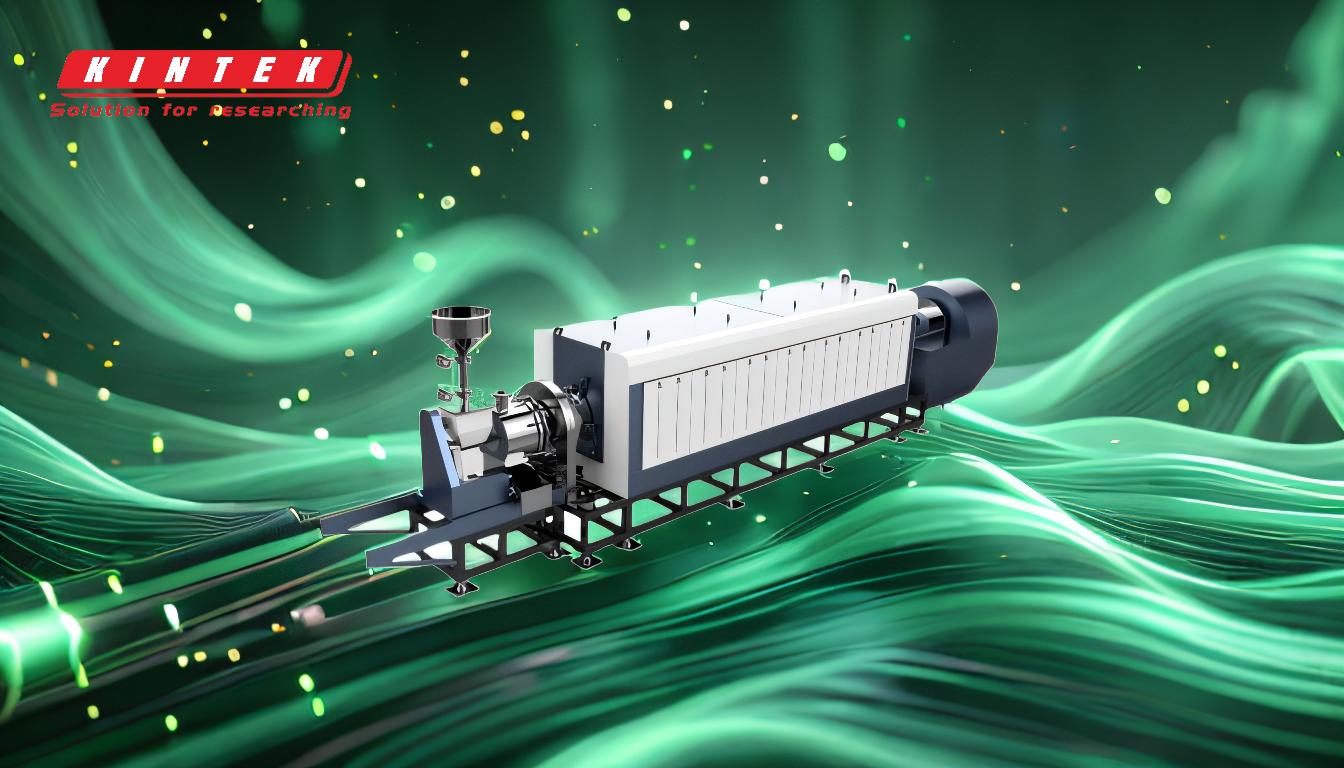
-
Temperature:
- Temperature is one of the most critical factors in pyrolysis. It directly influences the decomposition of the feedstock and the distribution of products (gas, liquid, and solid).
- Higher temperatures generally favor the production of non-condensable gases, while lower temperatures tend to produce more solid char and liquid bio-oil.
- The optimal temperature range varies depending on the feedstock and desired products. For example, biomass pyrolysis typically occurs between 400°C and 800°C.
-
Pressure:
- Pressure affects the pyrolysis process by influencing the rate of chemical reactions and the stability of intermediate products.
- Atmospheric pressure is commonly used in pyrolysis, but vacuum or elevated pressures can be employed to achieve specific outcomes, such as reducing secondary reactions or enhancing the yield of certain products.
-
Residence Time:
- Residence time refers to the duration that the feedstock remains in the pyrolysis reactor. It impacts the degree of thermal conversion and the composition of the resulting products.
- Longer residence times can lead to more complete decomposition but may also increase the risk of secondary reactions, which can alter product quality.
-
Feedstock Properties:
- The nature of the feedstock, including its composition, moisture content, particle size, and physical structure, significantly influences the pyrolysis process.
- For example, biomass with high moisture content requires additional energy for drying, while smaller particle sizes facilitate faster and more uniform thermal decomposition.
- Feedstock pretreatment, such as drying or shredding, can improve pyrolysis efficiency and product quality.
-
Heating Rate:
- The rate at which the feedstock is heated affects the distribution of pyrolysis products. Fast heating rates are typically associated with higher yields of liquid bio-oil, while slow heating rates favor the production of char and gas.
- The heating rate must be carefully controlled to achieve the desired product distribution and avoid undesirable side reactions.
-
Reactor Design:
- The type of reactor used in pyrolysis (e.g., fixed-bed, fluidized-bed, or rotary kiln) plays a crucial role in determining process efficiency and product characteristics.
- Reactor design influences heat transfer, residence time, and the ability to handle different feedstocks. For example, fluidized-bed reactors are known for their excellent heat transfer properties and uniform temperature distribution.
-
Atmosphere:
- The atmosphere in which pyrolysis occurs (e.g., inert, oxidative, or reducing) affects the chemical reactions and product composition.
- An inert atmosphere (e.g., nitrogen or argon) is commonly used to prevent oxidation and ensure the production of high-quality bio-oil and char.
-
Feed Rate:
- The rate at which feedstock is introduced into the reactor affects the overall efficiency and stability of the pyrolysis process.
- A consistent and controlled feed rate is essential to maintain optimal operating conditions and prevent issues such as reactor clogging or incomplete decomposition.
-
Environmental and Economic Considerations:
- Factors such as greenhouse gas (GHG) emissions, energy consumption, and the cost of feedstock processing must be considered to ensure the sustainability and economic viability of pyrolysis.
- For example, the energy used in biomass harvesting, pretreatment, and pyrolysis oil upgrading can significantly impact the overall carbon footprint of the process.
-
Product Quality and Yield Optimization:
- The yield and quality of pyrolysis products (bio-oil, char, and gas) are influenced by the interplay of all the above factors.
- Optimization of these parameters is essential to maximize the value of the products, whether for energy generation, chemical production, or material recovery.
In summary, pyrolysis is a complex process that requires careful control of multiple variables to achieve desired outcomes. By understanding and optimizing these requirements, it is possible to enhance the efficiency, sustainability, and economic viability of pyrolysis for various applications.
Summary Table:
Factor | Impact on Pyrolysis | Optimal Range/Considerations |
---|---|---|
Temperature | Influences decomposition and product distribution (gas, liquid, solid). | 400°C–800°C for biomass pyrolysis. Higher temps favor gas; lower temps favor char and bio-oil. |
Pressure | Affects reaction rates and product stability. | Atmospheric pressure is common; vacuum or elevated pressure for specific outcomes. |
Residence Time | Determines degree of thermal conversion and product composition. | Longer times increase decomposition but may cause secondary reactions. |
Feedstock Properties | Composition, moisture, particle size, and structure affect efficiency and product quality. | Pretreatment (drying, shredding) improves efficiency. |
Heating Rate | Influences product distribution (bio-oil, char, gas). | Fast heating favors bio-oil; slow heating favors char and gas. |
Reactor Design | Determines heat transfer, residence time, and feedstock handling. | Fluidized-bed reactors offer excellent heat transfer and uniform temperature distribution. |
Atmosphere | Affects chemical reactions and product composition. | Inert atmosphere (e.g., nitrogen) prevents oxidation and ensures high-quality products. |
Feed Rate | Impacts process stability and efficiency. | Consistent and controlled feed rate prevents clogging and incomplete decomposition. |
Environmental Factors | GHG emissions, energy consumption, and feedstock costs influence sustainability. | Biomass pretreatment and oil upgrading impact the overall carbon footprint. |
Product Optimization | Yield and quality depend on the interplay of all factors. | Optimization maximizes value for energy, chemicals, or material recovery. |
Ready to optimize your pyrolysis process? Contact our experts today for tailored solutions!