Brazing is a widely used joining process that involves heating a filler metal to its melting point and allowing it to flow into the joint between two or more metal parts. While brazing is an effective method, it requires strict adherence to safety precautions to prevent accidents, injuries, and health hazards. Key safety measures include proper ventilation, the use of personal protective equipment (PPE), fire prevention, and handling of hazardous materials. These precautions ensure a safe working environment and minimize risks associated with heat, fumes, and chemical exposure.
Key Points Explained:
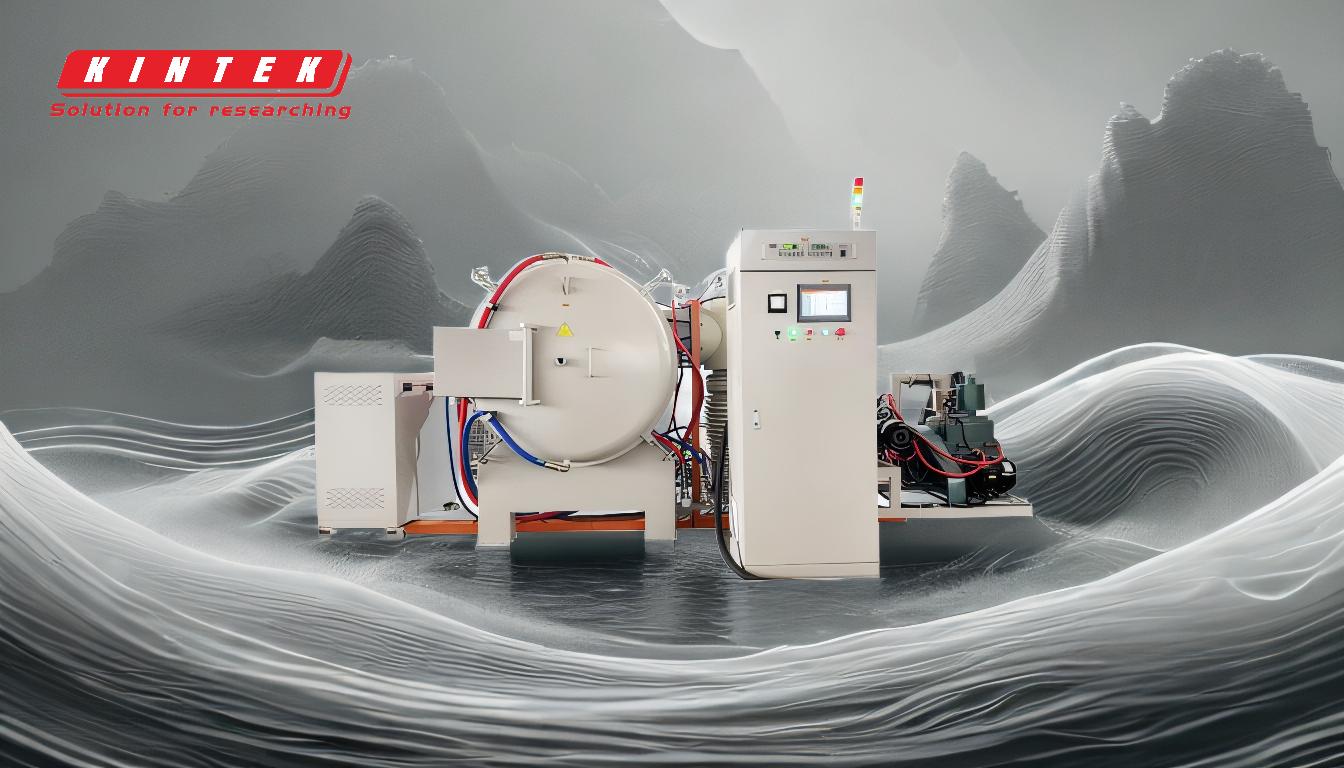
-
Proper Ventilation
- Brazing produces fumes and gases, such as zinc oxide, cadmium oxide, and flux vapors, which can be harmful if inhaled.
- Ensure the workspace is well-ventilated, either through natural airflow or mechanical ventilation systems like fume extractors.
- Use local exhaust ventilation (LEV) systems to capture fumes at the source, preventing them from spreading into the workspace.
-
Personal Protective Equipment (PPE)
- Wear appropriate PPE to protect against burns, eye injuries, and inhalation of harmful fumes.
- Safety glasses or face shields with side protection are essential to shield eyes from sparks and molten metal.
- Heat-resistant gloves and aprons protect against burns from hot materials and equipment.
- Respiratory protection, such as masks or respirators, should be used when working in areas with inadequate ventilation or when handling toxic materials.
-
Fire Prevention
- Brazing involves high temperatures, which can ignite flammable materials nearby.
- Keep the workspace clear of combustible materials, such as paper, cloth, or solvents.
- Have fire extinguishers readily available, and ensure they are suitable for metal fires (Class D extinguishers).
- Use fire-resistant barriers or screens to contain sparks and spatter.
-
Handling Hazardous Materials
- Brazing often involves fluxes and filler metals that may contain hazardous substances like cadmium or lead.
- Read and follow the safety data sheets (SDS) for all materials used in the brazing process.
- Store hazardous materials in properly labeled containers and ensure they are kept away from heat sources.
- Dispose of waste materials, such as used flux and metal scraps, in accordance with local regulations.
-
Equipment Safety
- Inspect brazing equipment, such as torches and heating elements, before use to ensure they are in good working condition.
- Avoid using damaged or malfunctioning equipment, as it can lead to accidents or injuries.
- Follow the manufacturer’s instructions for operating and maintaining brazing equipment.
- Use equipment with safety features, such as flame arrestors and automatic shut-off valves, to reduce risks.
-
Training and Awareness
- Ensure all personnel involved in brazing operations are properly trained in safety procedures and emergency response.
- Conduct regular safety briefings to reinforce the importance of following safety protocols.
- Post safety signs and warnings in the workspace to remind workers of potential hazards.
-
Emergency Preparedness
- Have a first aid kit readily available to treat minor burns or injuries.
- Establish an emergency response plan, including evacuation routes and procedures for dealing with fires or chemical spills.
- Train workers on how to respond to emergencies, such as using fire extinguishers or administering first aid.
By following these safety precautions, you can minimize risks and create a safer environment for brazing operations. Always prioritize safety to protect yourself and others from potential hazards.
Summary Table:
Safety Measure | Key Actions |
---|---|
Proper Ventilation | Use fume extractors or LEV systems to remove harmful fumes and gases. |
Personal Protective Equipment (PPE) | Wear safety glasses, heat-resistant gloves, aprons, and respiratory protection. |
Fire Prevention | Keep workspace clear of combustibles; use fire extinguishers and barriers. |
Handling Hazardous Materials | Follow SDS guidelines; store and dispose of materials safely. |
Equipment Safety | Inspect equipment regularly; follow manufacturer instructions. |
Training and Awareness | Train personnel on safety protocols and emergency response. |
Emergency Preparedness | Have first aid kits and fire extinguishers ready; establish evacuation plans. |
Ensure your brazing operations are safe and efficient—contact our experts today for personalized advice!