Brazing welding is a process that involves joining metals using a filler metal with a melting point above 840°F (450°C) but below the melting point of the base metals. While it is a relatively safe process compared to other welding methods, it still requires strict adherence to safety precautions to prevent accidents, injuries, and health hazards. Key safety measures include proper ventilation, personal protective equipment (PPE), fire safety protocols, and careful handling of materials and equipment. This answer outlines the essential safety precautions for brazing welding, ensuring a safe working environment for operators and others nearby.
Key Points Explained:
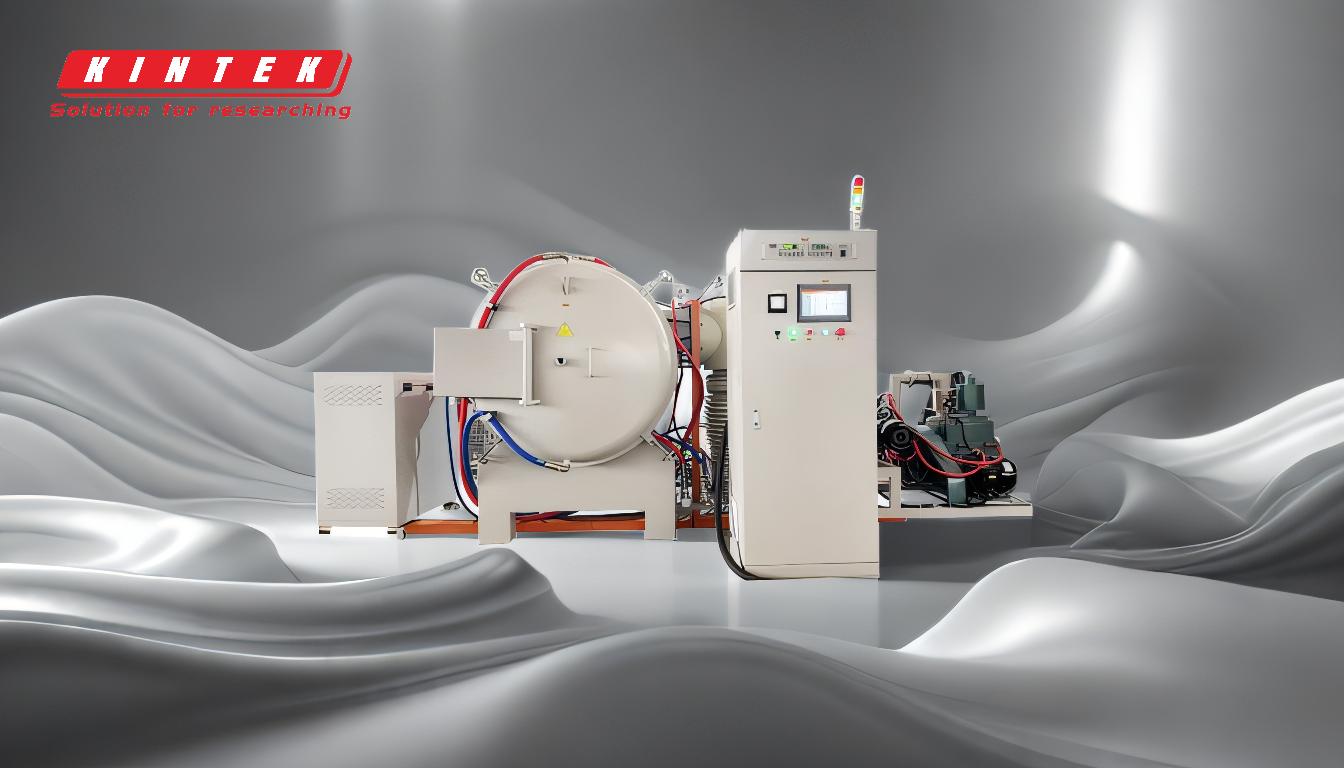
-
Ensure Proper Ventilation
- Brazing welding produces fumes and gases, such as zinc oxide, cadmium oxide, and flux vapors, which can be harmful if inhaled.
- Use local exhaust ventilation (LEV) systems or fume extraction equipment to remove contaminants from the air.
- Work in well-ventilated areas or use general ventilation systems to disperse fumes effectively.
- Avoid confined spaces without adequate airflow, as this can lead to the accumulation of hazardous fumes.
-
Wear Appropriate Personal Protective Equipment (PPE)
- Eye Protection: Wear safety goggles or a face shield to protect against sparks, splashes of molten metal, and UV radiation.
- Respiratory Protection: Use respirators or masks with appropriate filters if ventilation is insufficient or when working with materials that produce toxic fumes.
- Heat-Resistant Gloves: Wear gloves made of leather or other heat-resistant materials to protect hands from burns and hot surfaces.
- Protective Clothing: Use flame-resistant clothing, aprons, and sleeves to shield the body from heat, sparks, and molten metal.
- Footwear: Wear steel-toed boots to protect feet from falling objects and hot materials.
-
Fire Safety Precautions
- Keep a fire extinguisher rated for Class A, B, and C fires nearby, as brazing involves open flames and flammable materials.
- Remove flammable substances, such as solvents, oils, and paper, from the work area.
- Use fire-resistant barriers or welding blankets to protect nearby surfaces and materials.
- Have a fire watch person present during and after welding operations to monitor for potential fire hazards.
-
Handle Materials and Equipment Safely
- Inspect brazing equipment, such as torches, hoses, and regulators, for damage or leaks before use.
- Use only approved and properly labeled filler metals and fluxes.
- Store flammable gases, such as acetylene and propane, in well-ventilated areas away from heat sources.
- Follow manufacturer guidelines for setting up and operating brazing equipment.
- Avoid touching hot workpieces or equipment without proper protection.
-
Prevent Electrical Hazards
- Ensure all electrical connections and equipment are properly grounded and insulated.
- Avoid using damaged power cords or equipment with exposed wires.
- Keep electrical equipment dry and away from water or moisture to prevent electric shock.
-
Health and Hygiene Practices
- Wash hands thoroughly after handling brazing materials, especially fluxes and filler metals, to avoid skin irritation or ingestion of harmful substances.
- Avoid eating, drinking, or smoking in the work area to prevent accidental ingestion of contaminants.
- Seek medical attention if exposed to harmful fumes or if symptoms like dizziness, nausea, or respiratory distress occur.
-
Training and Awareness
- Ensure all operators are trained in brazing techniques and safety protocols.
- Stay updated on safety standards and best practices for brazing welding.
- Conduct regular safety audits and inspections of the work area and equipment.
By following these safety precautions, operators can minimize risks and create a safer environment for brazing welding operations. Proper planning, equipment maintenance, and adherence to safety guidelines are essential to prevent accidents and ensure the well-being of everyone involved.
Summary Table:
Safety Measure | Key Actions |
---|---|
Proper Ventilation | Use LEV systems, work in well-ventilated areas, avoid confined spaces. |
Personal Protective Equipment | Wear goggles, respirators, heat-resistant gloves, flame-resistant clothing. |
Fire Safety | Keep fire extinguishers, remove flammables, use fire-resistant barriers. |
Material & Equipment Handling | Inspect equipment, use approved materials, store gases safely. |
Electrical Safety | Ground equipment, avoid damaged cords, keep equipment dry. |
Health & Hygiene | Wash hands, avoid eating/drinking in work area, seek medical attention if needed. |
Training & Awareness | Train operators, stay updated on safety standards, conduct regular audits. |
Ensure your brazing welding operations are safe and efficient—contact our experts today for personalized advice!