PVD (Physical Vapor Deposition) coating is a highly advanced surface finishing technique that alters the properties of metal at a molecular level. It is renowned for its exceptional hardness, corrosion resistance, and durability. PVD coatings are typically thin, ranging from 0.5 to 5 microns, and are applied at relatively low temperatures (150–250°C), ensuring minimal distortion of the coated components. The process is environmentally friendly, produces pure and clean coatings, and offers precise control over film properties such as density, structure, and stoichiometry. These attributes make PVD coatings ideal for applications requiring high wear resistance, corrosion protection, and aesthetic appeal.
Key Points Explained:
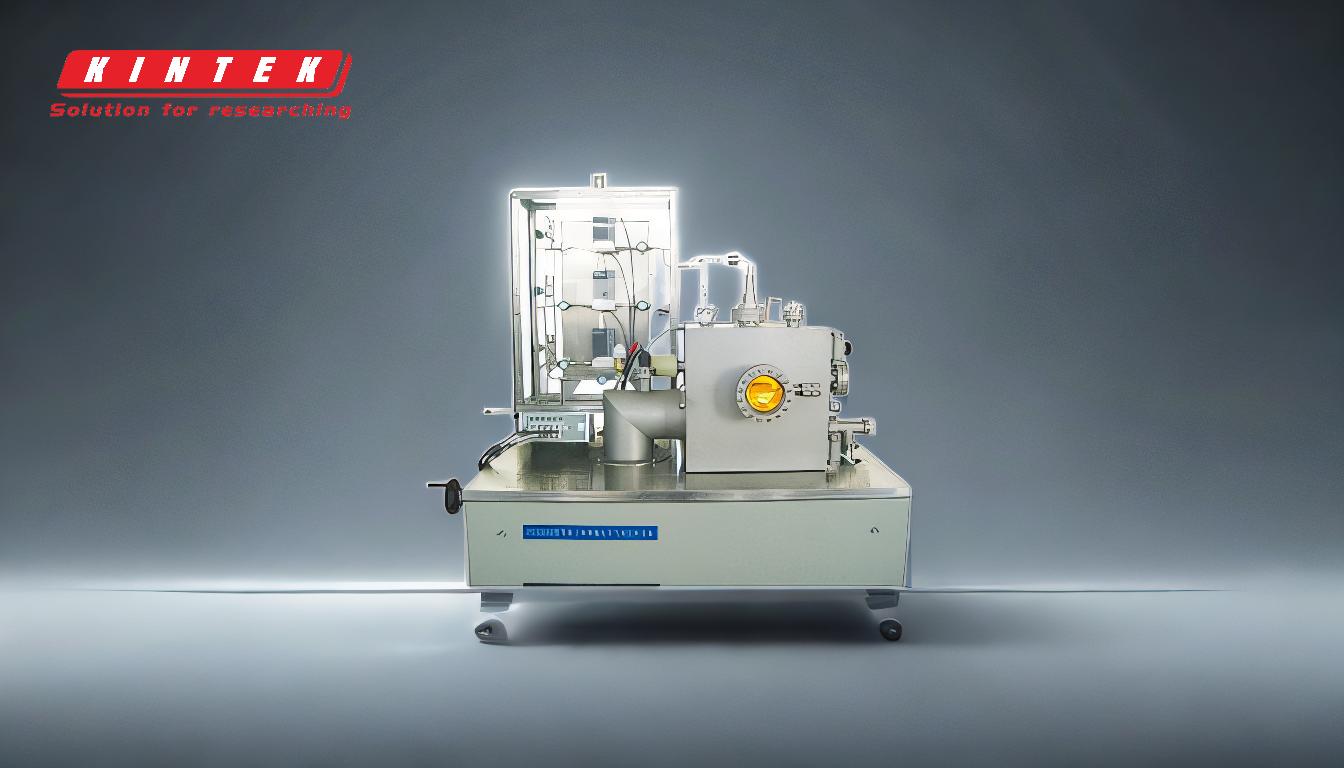
-
Hardness and Durability:
- PVD coatings are among the hardest synthetic materials, with a hardness range of 1500 to 4500 HV (Vickers hardness).
- This high hardness translates to excellent resistance to wear, abrasion, and erosion, making PVD-coated components highly durable and long-lasting.
-
Thickness and Precision:
- PVD coatings are extremely thin, typically ranging from 0.5 to 5 microns.
- This minimal thickness ensures that the size tolerance of the coated component is not significantly affected, making it suitable for precision applications.
-
Low-Temperature Process:
- The PVD coating process occurs at relatively low temperatures, between 150°C and 250°C.
- This low-temperature deposition prevents distortion of the coated components and preserves the core hardness of the substrate material.
-
Corrosion and Oxidation Resistance:
- PVD coatings provide excellent resistance to corrosion and oxidation.
- This makes them ideal for use in harsh environments where components are exposed to moisture, chemicals, or high temperatures.
-
Environmental Friendliness:
- The PVD process is environmentally friendly, using physical means rather than chemical reactions.
- It produces no harmful byproducts and is more sustainable compared to other coating methods like CVD (Chemical Vapor Deposition).
-
Versatility in Applications:
- PVD coatings can be applied to a variety of materials, including stainless steel, and are used in industries such as aerospace, automotive, medical devices, and cutting tools.
- The process allows for the creation of coatings with specific attributes, such as adhesion, lubricity, and hardness, tailored to the needs of the application.
-
Aesthetic and Functional Benefits:
- PVD coatings offer a wide range of colors and textures, enhancing the aesthetic appeal of products.
- Beyond aesthetics, these coatings improve the chemical and wear resistance of products, increasing their durability and lifespan.
-
Process Steps:
- The PVD process involves three main steps:
- Vaporization: The coating material is vaporized in a vacuum.
- Migration: The vaporized atoms, molecules, or ions migrate through the vacuum.
- Deposition: The vaporized material condenses and forms a thin film on the substrate.
- This process ensures pure and high-quality coatings with improved surface quality by reducing roughness.
- The PVD process involves three main steps:
-
Challenges and Limitations:
- While PVD technology offers numerous benefits, it is still evolving. Challenges such as in-situ doping and achieving uniform coatings on complex geometries remain areas for further development.
In summary, PVD coating is a versatile and advanced technology that provides exceptional hardness, durability, and corrosion resistance. Its low-temperature process, environmental friendliness, and ability to produce thin, precise coatings make it a preferred choice for a wide range of industrial and decorative applications.
Summary Table:
Property | Specification |
---|---|
Hardness | 1500–4500 HV (Vickers hardness) |
Thickness | 0.5–5 microns |
Temperature Range | 150–250°C |
Corrosion Resistance | Excellent resistance to corrosion and oxidation |
Environmental Impact | Eco-friendly, no harmful byproducts |
Applications | Aerospace, automotive, medical devices, cutting tools |
Aesthetic Options | Wide range of colors and textures |
Process Steps | Vaporization, migration, deposition |
Learn how PVD coating can enhance your products—contact our experts today for more details!