Sintering is a critical process in materials science and manufacturing, used to transform powdery materials into dense, solid bodies by applying heat and pressure below the material's melting point. This process is widely employed in industries such as ceramics, powder metallurgy, and plastics. The sintering process is typically divided into three main stages: powder composing, powder compacting, and sintering or firing. Each stage plays a vital role in ensuring the final product's structural integrity, density, and performance. Understanding these stages is essential for optimizing the sintering process and achieving high-quality results.
Key Points Explained:
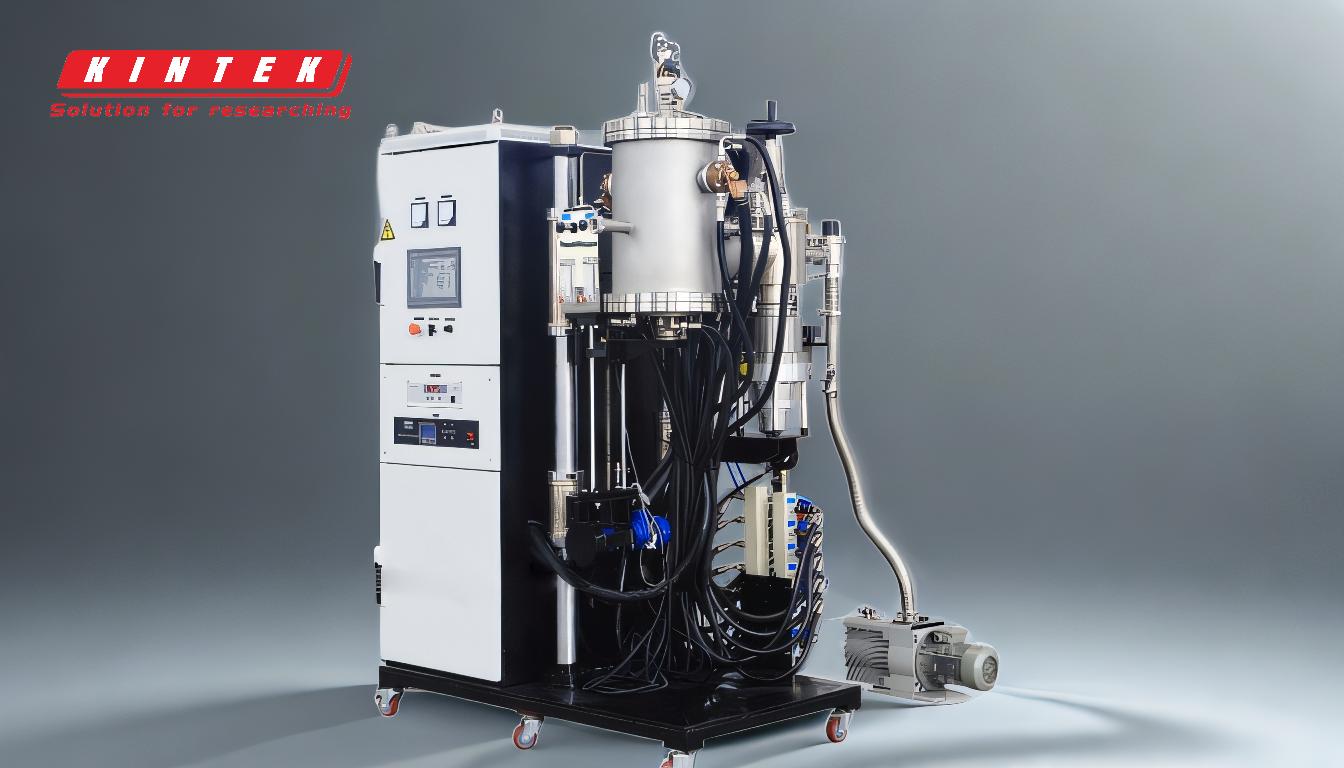
-
Powder Composing:
- Definition: This is the initial stage where raw materials are prepared and mixed to create a uniform powder blend.
-
Process:
- Water, deflocculant, binder, and unfired ceramic powder are mixed to form a slurry.
- The slurry is then spray-dried to produce a free-flowing powder.
-
Purpose:
- Ensures uniformity in particle size and composition.
- Prepares the material for the next stage of compaction.
-
Considerations:
- The choice of binder and deflocculant affects the flowability and compaction properties of the powder.
- Proper mixing is crucial to avoid defects in the final product.
-
Powder Compacting:
- Definition: This stage involves the mechanical densification of the powder to form a "green" part, which is a pre-sintered shape.
-
Process:
- The powder is compacted using cold or hot mold pressing techniques.
- Pressure is applied to eliminate voids and achieve the desired shape and density.
-
Purpose:
- Creates a green part with sufficient strength to handle before sintering.
- Reduces porosity and increases density, which is critical for the final product's mechanical properties.
-
Considerations:
- The pressure applied must be carefully controlled to avoid cracking or uneven density.
- The green part must have enough strength to withstand handling and transportation to the sintering furnace.
-
Sintering or Firing:
- Definition: The final stage where the green part is heated in a controlled environment to fuse the particles together.
-
Process:
- The green part is placed in a sintering furnace, where it is heated to a temperature below the material's melting point.
- During heating, particles undergo diffusion, leading to neck formation and densification.
- The material is then cooled to solidify into a rigid and cohesive structure.
-
Purpose:
- Achieves the final density and mechanical properties of the material.
- Bonds the particles together to form a solid mass without melting the entire material.
-
Considerations:
- Temperature control is critical to prevent over-sintering or under-sintering.
- The atmosphere in the furnace (e.g., reducing, oxidizing, or inert) can affect the final properties of the sintered product.
- Cooling rates must be controlled to avoid thermal stresses that could lead to cracking.
-
Post-Sintering Processes:
- Definition: Additional treatments that may be applied after sintering to enhance the properties of the final product.
-
Process:
- Heat treatment to improve mechanical properties.
- Surface finishing (e.g., grinding, polishing) to achieve the desired surface quality.
- Coating or impregnation to enhance wear resistance or other properties.
-
Purpose:
- Further improves the mechanical, thermal, or chemical properties of the sintered product.
- Ensures the product meets specific application requirements.
-
Considerations:
- The choice of post-sintering treatments depends on the material and the intended use of the product.
- These processes can add significant value but also increase production costs.
-
Applications and Materials:
-
Applications:
- Sintering is used in a wide range of industries, including automotive, aerospace, electronics, and medical devices.
- Common products include gears, bearings, filters, and cutting tools.
-
Materials:
- Metals (e.g., iron, copper, tungsten).
- Ceramics (e.g., alumina, zirconia).
- Plastics (e.g., PTFE, PEEK).
-
Considerations:
- The choice of material depends on the desired properties of the final product (e.g., strength, wear resistance, thermal conductivity).
- Different materials may require specific sintering conditions (e.g., temperature, atmosphere).
-
Applications:
In conclusion, the sintering process is a complex and multi-stage procedure that transforms powdery materials into dense, solid bodies. Each stage—powder composing, powder compacting, and sintering—plays a crucial role in determining the final product's properties and performance. Understanding these stages and their nuances is essential for optimizing the sintering process and achieving high-quality results in various industrial applications.
Summary Table:
Stage | Description | Key Considerations |
---|---|---|
Powder Composing | Mixing raw materials to create a uniform powder blend. | Binder and deflocculant choice, proper mixing to avoid defects. |
Powder Compacting | Densifying the powder to form a pre-sintered "green" part. | Controlled pressure, green part strength for handling. |
Sintering/Firing | Heating the green part to fuse particles without melting. | Temperature control, furnace atmosphere, cooling rate to prevent cracking. |
Post-Sintering | Additional treatments (heat treatment, surface finishing, coating). | Material and application-specific treatments, cost considerations. |
Applications | Used in automotive, aerospace, electronics, and medical devices. | Material choice (metals, ceramics, plastics) based on desired properties. |
Optimize your sintering process for high-quality results—contact our experts today!