Sputtering is a widely used thin-film deposition technique that involves the ejection of atoms from a solid target material due to bombardment by energetic ions, followed by their deposition onto a substrate. The process typically occurs in a vacuum chamber and utilizes an inert gas, such as argon, to create a plasma. The key steps involve creating a vacuum, introducing the inert gas, ionizing the gas, and accelerating ions toward the target to eject material, which then deposits onto the substrate. This method is highly versatile and used in applications ranging from semiconductor manufacturing to optical coatings.
Key Points Explained:
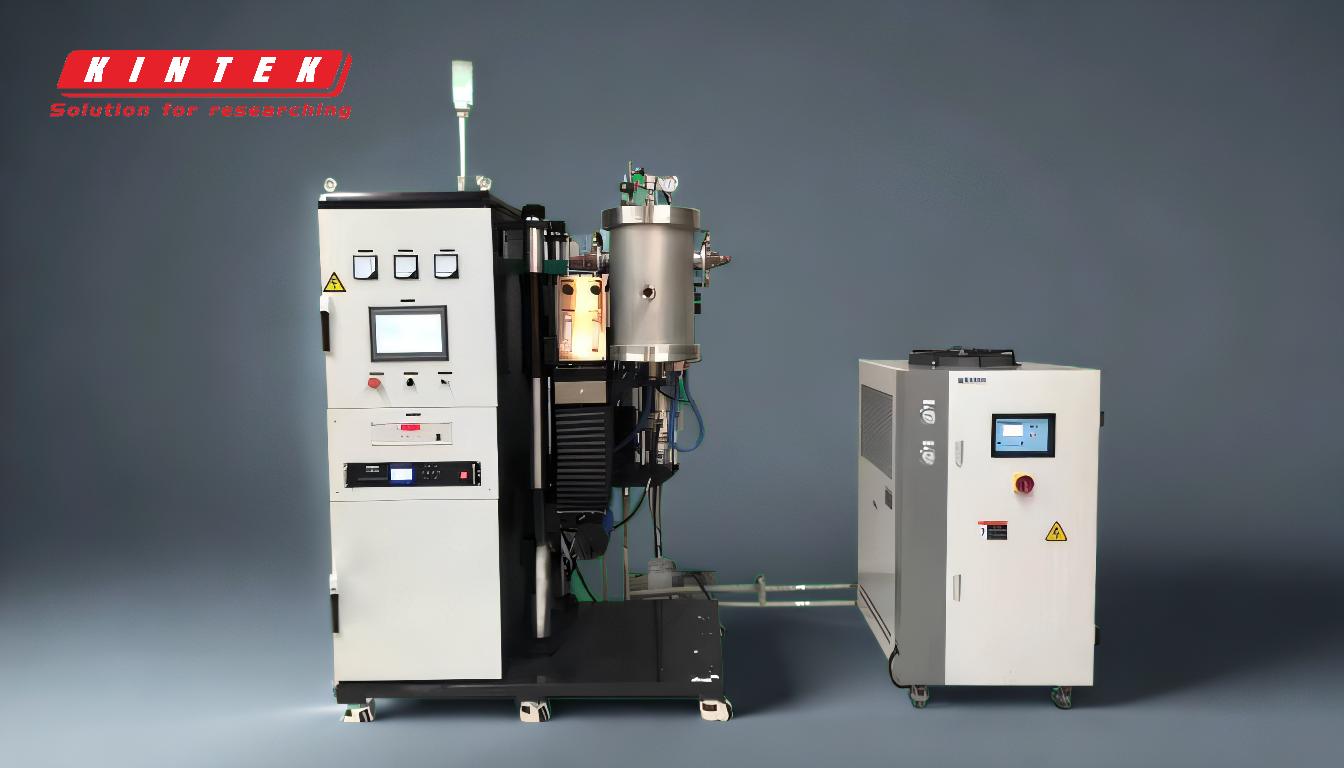
-
Creating a Vacuum:
- The first step in the sputtering process is to evacuate the reaction chamber to create a vacuum. This is crucial for removing moisture, impurities, and any residual gases that could interfere with the deposition process. The pressure is typically reduced to around 1 Pa (Pascal). A vacuum environment ensures that the sputtering gas and target material interact without contamination.
-
Introducing Inert Gas:
- Once a vacuum is established, an inert gas, such as argon, is introduced into the chamber. Inert gases are preferred because they do not react chemically with the target material or the substrate. The gas creates a low-pressure atmosphere, which is essential for generating a stable plasma during the ionization step.
-
Heating the Chamber:
- The chamber is often heated to temperatures between 150°C and 750°C, depending on the materials involved and the desired film properties. Heating helps to improve the adhesion of the deposited film to the substrate and can also influence the microstructure of the film. This step is particularly important for achieving high-quality, dense coatings.
-
Creating a Magnetic Field (Magnetron Sputtering):
- In magnetron sputtering, a magnetic field is created using an electromagnet placed between the target and the substrate. This magnetic field confines the plasma close to the target surface, increasing the efficiency of the sputtering process. The confined plasma leads to higher ionization rates and more energetic ions, which enhances the rate of target material ejection.
-
Ionizing the Gas:
- A high voltage is applied to ionize the inert gas atoms. This ionization process creates a plasma, which consists of positively charged gas ions and free electrons. The plasma is essential for accelerating the ions toward the target material. In RF (radio frequency) sputtering, radio waves are used to ionize the gas, making this method suitable for insulating target materials.
-
Sputtering the Target Material:
- The target material is negatively charged (cathode), attracting the positively charged gas ions from the plasma. When these ions collide with the target, they transfer their kinetic energy to the target atoms, causing them to be ejected from the surface. This process is known as sputtering. The ejected atoms travel through the vacuum and deposit onto the substrate, forming a thin film.
-
Deposition on the Substrate:
- The ejected target atoms travel through the vacuum and condense onto the substrate, forming a thin film. The substrate is typically positioned opposite the target and may be heated or biased to improve film quality. The thickness and properties of the deposited film can be controlled by adjusting parameters such as gas pressure, voltage, and deposition time.
-
Glow Discharge and Plasma Stability:
- During the sputtering process, a glow discharge may occur as some positive ions return to their ground state by capturing free electrons and releasing photons. This glow discharge is a visible indication of the plasma's presence and stability. Maintaining a stable plasma is critical for consistent and uniform film deposition.
By following these steps, the sputtering process enables the precise deposition of thin films with controlled thickness, composition, and microstructure. This makes it an invaluable technique in industries such as microelectronics, optics, and materials science.
Summary Table:
Step | Description |
---|---|
1. Creating a Vacuum | Evacuate the chamber to remove impurities and achieve a pressure of ~1 Pa. |
2. Introducing Inert Gas | Add inert gas (e.g., argon) to create a low-pressure atmosphere for plasma. |
3. Heating the Chamber | Heat to 150°C–750°C to improve film adhesion and microstructure. |
4. Magnetic Field (Optional) | Use electromagnets to confine plasma for higher efficiency (magnetron sputtering). |
5. Ionizing the Gas | Apply high voltage to create plasma for ion acceleration. |
6. Sputtering Target Material | Eject atoms from the target by ion bombardment. |
7. Deposition on Substrate | Ejected atoms condense on the substrate to form a thin film. |
8. Glow Discharge & Plasma Stability | Maintain stable plasma for consistent film deposition. |
Need expert advice on sputtering systems? Contact us today to find the right solution for your application!