The Chemical Vapor Deposition (CVD) process is a sophisticated method used to deposit thin films onto substrates through chemical reactions in a controlled environment. It involves several key steps: preparation of the substrate, introduction of precursor gases into a reaction chamber, activation of the precursors through heat, light, or plasma, and the subsequent chemical reactions that result in the deposition of a solid material on the substrate. The process is influenced by various parameters such as temperature, pressure, and flow rates, which determine the quality and characteristics of the deposited film. CVD is widely used in industries for coating applications, semiconductor manufacturing, and the production of advanced materials.
Key Points Explained:
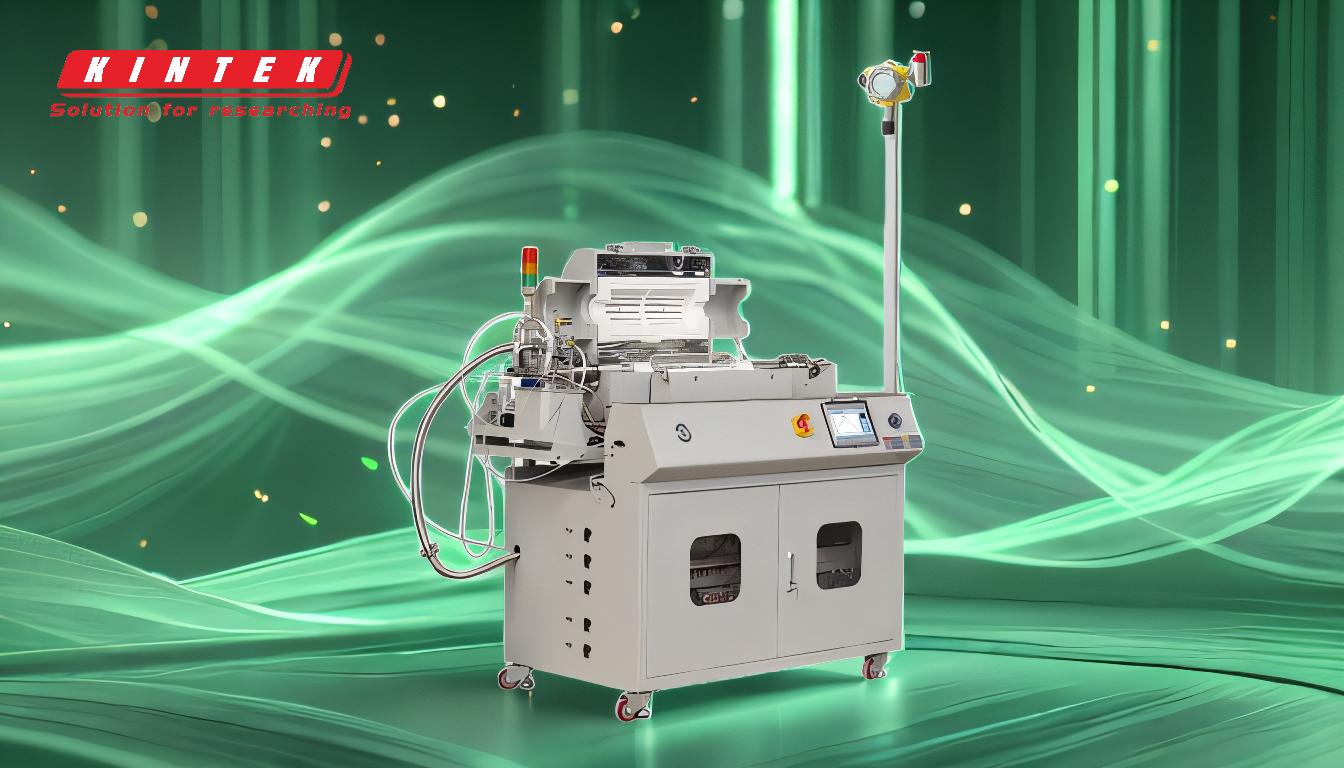
-
Preparation of the Substrate:
- The substrate must be thoroughly cleaned and prepared to ensure proper adhesion of the thin film. This involves removing any contaminants and sometimes pre-treating the surface to enhance bonding.
-
Introduction of Precursor Gases:
- Volatile precursor gases are introduced into the reaction chamber. These gases are chosen based on the desired chemical composition of the deposited film.
-
Activation of Precursors:
- The precursor gases are activated using heat, light, or plasma. This activation causes the gases to react or decompose, forming reactive species that are essential for the deposition process.
-
Chemical Reaction and Deposition:
- The activated species react on the surface of the substrate, leading to the deposition of a thin film. The chemical reactions occur at the molecular level, ensuring a uniform and high-quality coating.
-
Control of Process Parameters:
- Key parameters such as temperature, pressure, and flow rates are carefully controlled to influence the structure, morphology, and properties of the deposited film. These parameters are critical for achieving the desired film characteristics.
-
Exhaustion of By-products:
- Chemical by-products and unreacted gases are continuously removed from the reaction chamber through an exhausting system. This step is crucial to maintain the purity and quality of the deposited film.
-
Post-Deposition Treatments:
- After deposition, the coated substrate may undergo additional treatments such as annealing or surface modification to enhance the film's properties and performance.
-
Applications of CVD:
- CVD is used in various applications including semiconductor manufacturing, protective coatings, and the production of advanced materials like polycrystalline diamond. The versatility of the CVD process makes it a valuable technique in multiple industries.
By understanding and controlling each of these steps, manufacturers can produce high-quality thin films with specific properties tailored to their application needs. The CVD process's ability to deposit uniform and adherent films makes it a cornerstone in modern material science and engineering.
Summary Table:
Step | Description |
---|---|
1. Preparation of Substrate | Clean and pre-treat the substrate to ensure proper adhesion of the thin film. |
2. Introduction of Gases | Introduce volatile precursor gases into the reaction chamber. |
3. Activation of Precursors | Activate gases using heat, light, or plasma to form reactive species. |
4. Chemical Reaction | Reactive species deposit a uniform, high-quality thin film on the substrate. |
5. Control Parameters | Regulate temperature, pressure, and flow rates for desired film characteristics. |
6. Exhaust By-products | Remove by-products and unreacted gases to maintain film purity. |
7. Post-Deposition Treatments | Enhance film properties through annealing or surface modification. |
8. Applications | Used in semiconductor manufacturing, protective coatings, and advanced materials. |
Discover how the CVD process can elevate your material science projects—contact our experts today!