PVD (Physical Vapor Deposition) coating is a versatile process that can be applied to a wide range of substrates, including metals, ceramics, plastics, and glass. The choice of substrate depends on its compatibility with the vacuum environment and the desired properties of the final coated product. Common substrates include tool materials, steels, glass, brass, zinc, and ABS plastic, often pre-treated to enhance adhesion. PVD coatings are used in various industries, from aerospace to automotive, and can be applied to materials like gold, brass, copper, stainless steel, graphite, titanium, and various plastics. The process does not level surface imperfections, so the substrate's surface finish is crucial for achieving the desired final appearance.
Key Points Explained:
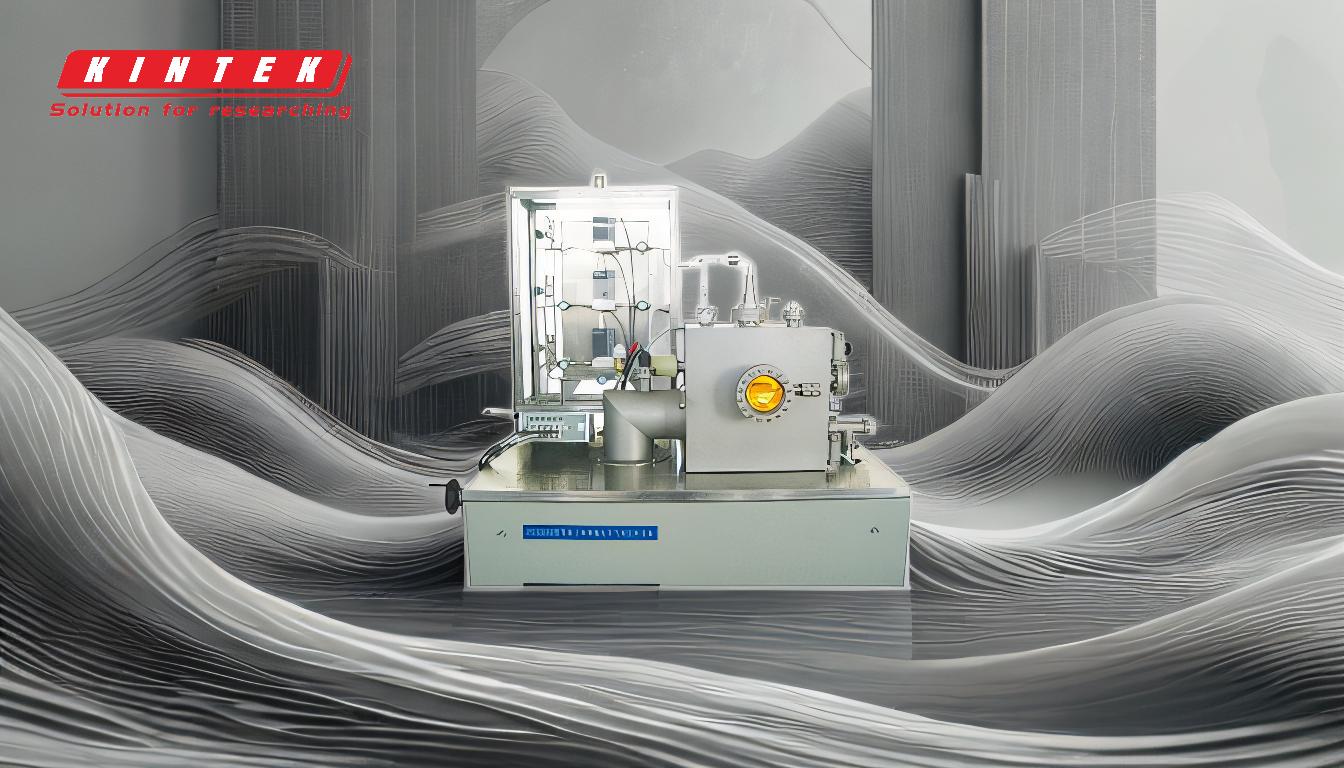
-
Types of Substrates for PVD Coating:
- Metals: Common metals include stainless steel, brass, copper, titanium, and zinc. High-alloy steels like high-speed steels and stainless steels are particularly suitable due to their durability and compatibility with the PVD process.
- Ceramics: Ceramics are also compatible with PVD coating, offering high thermal and chemical resistance.
- Plastics: Plastics such as ABS, polycarbonate, and PC-ABS can be coated, though they often require pre-treatment to ensure proper adhesion.
- Glass: Glass substrates are used in applications requiring transparency and scratch resistance.
-
Pre-Treatment of Substrates:
- Substrates often undergo pre-treatment processes like organic coatings or electroplating with nickel and chromium to improve adhesion and compatibility with the PVD process.
- Surface finish is crucial; polished surfaces are used for polished PVD finishes, while brushed or satin surfaces are used for satin or matt finishes.
-
Material Compatibility:
- Materials must be vacuum-compatible. For example, brass without galvanization or galvanized materials are not suitable due to their vacuum-unfriendly nature.
- Chrome or nickel-plated metal products can be coated, enhancing their durability and appearance.
-
Applications of PVD Coating:
- Aerospace and Automotive: High-performance materials like graphite and titanium are often used in these industries due to their strength and resistance to extreme conditions.
- Plastic Molding Dies: Coatings like chromium nitride (CrN), titanium nitride (TiN), and titanium carbonitride (TiCN) are used to enhance the durability and performance of plastic molding dies.
-
Specialized Coatings:
- PVD coatings can include unique materials like carbides, nitrides, silicides, and borides, tailored for specific applications requiring enhanced properties such as hardness, wear resistance, or thermal stability.
-
Limitations and Considerations:
- PVD coating does not level or fill surface imperfections, so the substrate's surface quality is critical for the final appearance.
- The process is compatible with a wide range of materials, but the substrate must be carefully selected and prepared to ensure optimal results.
In summary, PVD coating is a highly adaptable process suitable for a diverse array of substrates, each requiring specific considerations for pre-treatment and surface finish to achieve the desired properties and appearance.
Summary Table:
Substrate Type | Examples | Key Considerations |
---|---|---|
Metals | Stainless steel, brass, copper, titanium, zinc | High durability, vacuum compatibility |
Ceramics | Alumina, zirconia | High thermal and chemical resistance |
Plastics | ABS, polycarbonate, PC-ABS | Requires pre-treatment for adhesion |
Glass | Borosilicate, soda-lime | Transparency, scratch resistance |
Pre-Treatment | Organic coatings, electroplating | Enhances adhesion and surface finish |
Applications | Aerospace, automotive, plastic molding dies | High-performance and durability requirements |
Learn how PVD coating can enhance your materials—contact our experts today!