Thin film deposition is a critical process in materials science and engineering, used to create thin layers of material on a substrate. The techniques for thin film deposition are broadly categorized into two main types: Physical Vapor Deposition (PVD) and Chemical Vapor Deposition (CVD). These methods are further divided into various sub-techniques, each with unique mechanisms and applications. PVD techniques involve the physical transfer of material from a source to a substrate, typically in a vacuum environment, while CVD techniques rely on chemical reactions to deposit material onto the substrate. Additionally, other methods like Atomic Layer Deposition (ALD), Spray Pyrolysis, and Spin Coating offer specialized approaches for achieving precise control over film thickness and properties. Understanding these techniques is essential for selecting the appropriate method based on the desired film characteristics and application requirements.
Key Points Explained:
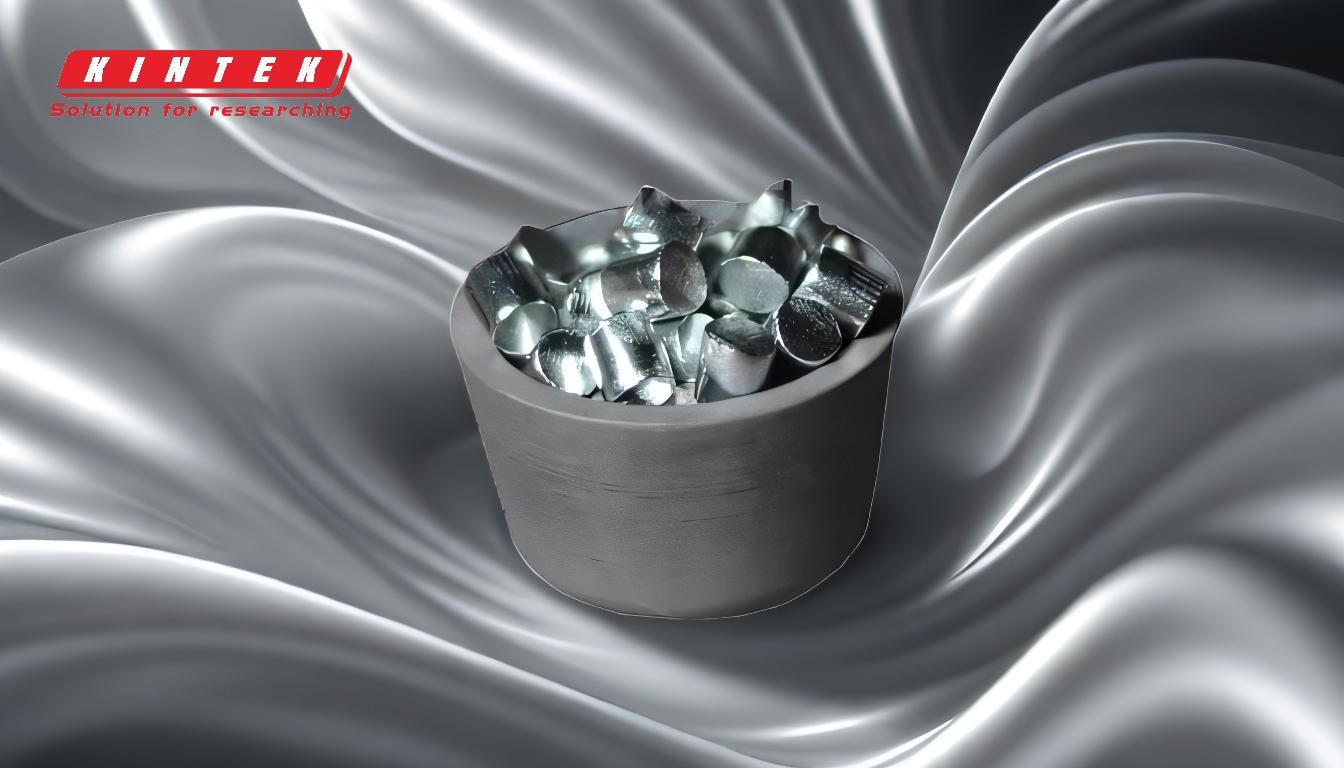
-
Physical Vapor Deposition (PVD)
- Definition: PVD involves the physical transfer of material from a source to a substrate, typically in a vacuum environment.
-
Techniques:
- Evaporation: Material is heated until it vaporizes and then condenses on the substrate. Techniques include thermal evaporation and electron beam evaporation.
- Sputtering: Atoms are ejected from a solid target material by bombarding it with high-energy ions, which then deposit onto the substrate. Common methods include magnetron sputtering and ion beam sputtering.
- Pulsed Laser Deposition (PLD): A high-power laser ablates material from a target, creating a plasma plume that deposits onto the substrate.
- Molecular Beam Epitaxy (MBE): A highly controlled process where beams of atoms or molecules are directed at the substrate to grow epitaxial films layer by layer.
- Applications: PVD is widely used in semiconductor manufacturing, optical coatings, and decorative finishes.
-
Chemical Vapor Deposition (CVD)
- Definition: CVD involves chemical reactions to produce high-purity thin films. Precursor gases react on the substrate surface to form the desired material.
-
Techniques:
- Thermal CVD: The substrate is heated to high temperatures to facilitate the chemical reaction.
- Plasma-Enhanced CVD (PECVD): Plasma is used to lower the reaction temperature, making it suitable for temperature-sensitive substrates.
- Atomic Layer Deposition (ALD): A specialized form of CVD where films are deposited one atomic layer at a time, offering exceptional control over thickness and uniformity.
- Metal-Organic CVD (MOCVD): Uses metal-organic precursors to deposit compound semiconductors, commonly used in LED and laser diode production.
- Applications: CVD is essential for creating high-quality films in microelectronics, solar cells, and protective coatings.
-
Other Deposition Techniques
- Spin Coating: A liquid precursor is applied to a substrate, which is then spun at high speeds to spread the material evenly. This method is commonly used for creating uniform polymer films.
- Dip Coating: The substrate is dipped into a liquid precursor and then withdrawn at a controlled speed, leaving a thin film on the surface.
- Spray Pyrolysis: A solution containing the desired material is sprayed onto a heated substrate, where it decomposes to form a thin film.
- Sol-Gel: A wet-chemical process where a solution (sol) transitions to a gel-like state, which is then dried and sintered to form a thin film.
- Electroplating: An electrochemical process where metal ions are reduced and deposited onto a conductive substrate.
-
Factors Influencing Technique Selection
- Film Thickness and Uniformity: Techniques like ALD and spin coating offer precise control over thickness, while PVD and CVD are better suited for thicker films.
- Substrate Material and Temperature Sensitivity: PECVD and ALD are ideal for temperature-sensitive substrates, whereas thermal CVD and PVD require higher temperatures.
- Material Compatibility: Certain materials are better suited to specific techniques, such as metals for sputtering and semiconductors for MOCVD.
- Application Requirements: The intended use of the thin film (e.g., optical, electronic, or protective) dictates the choice of deposition method.
-
Emerging Trends in Thin Film Deposition
- Hybrid Techniques: Combining PVD and CVD methods to leverage the advantages of both.
- Nanostructured Films: Advanced techniques like ALD and MBE are enabling the creation of films with nanoscale precision.
- Sustainability: Development of eco-friendly precursors and energy-efficient processes to reduce environmental impact.
By understanding these techniques and their respective advantages, equipment and consumable purchasers can make informed decisions when selecting the appropriate method for their specific application.
Summary Table:
Category | Techniques | Applications |
---|---|---|
Physical Vapor Deposition (PVD) | Evaporation, Sputtering, PLD, MBE | Semiconductor manufacturing, optical coatings, decorative finishes |
Chemical Vapor Deposition (CVD) | Thermal CVD, PECVD, ALD, MOCVD | Microelectronics, solar cells, protective coatings |
Other Techniques | Spin Coating, Dip Coating, Spray Pyrolysis, Sol-Gel, Electroplating | Polymer films, nanostructured films, eco-friendly processes |
Need help selecting the right thin film deposition technique? Contact our experts today!