Vapor phase techniques, particularly in the context of Physical Vapor Deposition (PVD), are essential for creating thin films and coatings with high purity and uniformity. The two most common techniques are thermal evaporation and sputtering. Thermal evaporation involves heating a material until it vaporizes, allowing the vapor to condense on a substrate to form a thin film. Sputtering, on the other hand, involves ejecting material from a target using high-energy ions, which then deposits onto a substrate. These methods are widely used in industries requiring precise and high-quality coatings, such as semiconductors, optics, and electronics.
Key Points Explained:
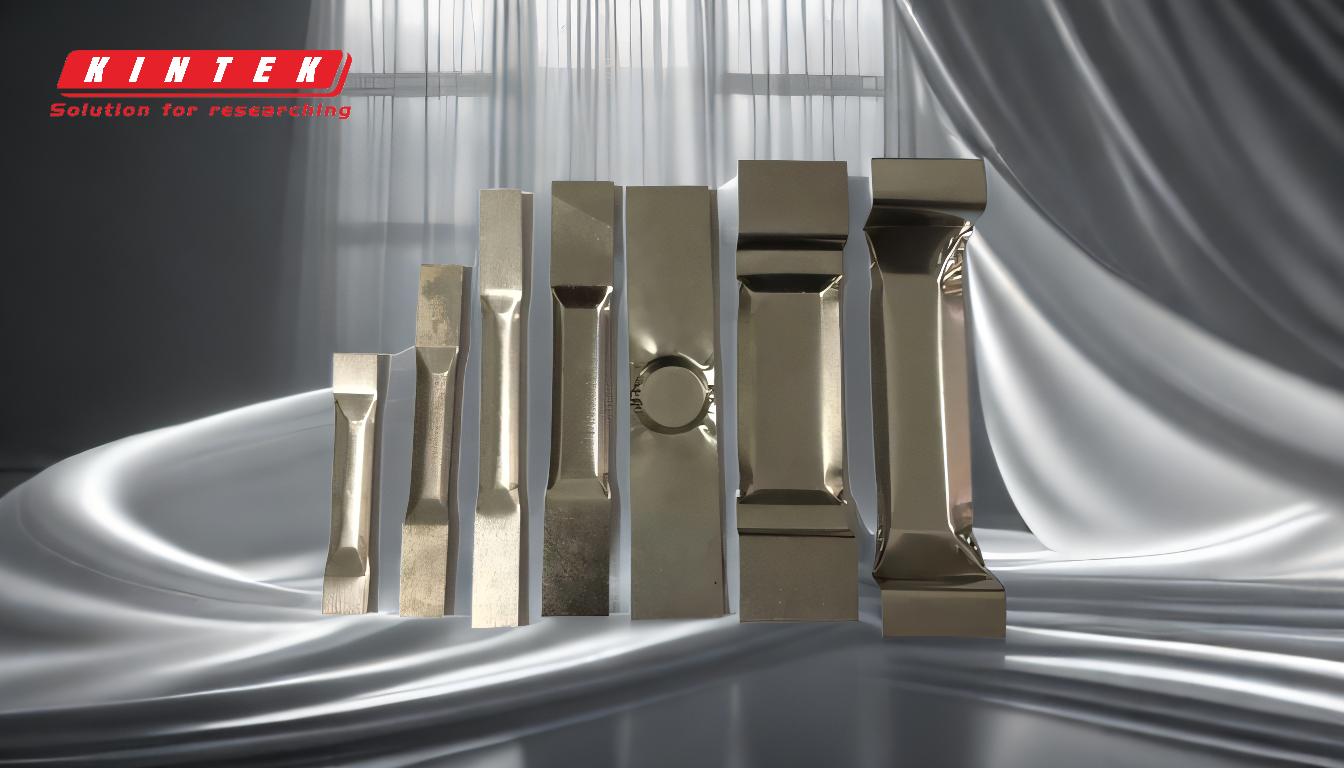
-
Thermal Evaporation:
- Process: In thermal evaporation, the material to be deposited is heated in a vacuum until it reaches its vaporization temperature. The vapor then travels through the vacuum and condenses on the cooler substrate, forming a thin film.
- Applications: This technique is commonly used for depositing metals and simple compounds. It is particularly useful in applications requiring high purity and uniformity, such as in the production of optical coatings and semiconductor devices.
- Advantages: Thermal evaporation is relatively simple and cost-effective. It allows for high deposition rates and can be used with a wide range of materials.
- Limitations: The process is limited by the need for high vacuum conditions and the difficulty in depositing complex compounds or alloys.
-
Sputtering:
- Process: Sputtering involves bombarding a target material with high-energy ions, typically from a plasma. The impact of these ions ejects atoms from the target, which then deposit onto the substrate.
- Applications: Sputtering is widely used in the deposition of thin films for electronic devices, magnetic storage media, and hard coatings. It is also used in the production of solar panels and flat-panel displays.
- Advantages: Sputtering allows for the deposition of a wide range of materials, including metals, alloys, and ceramics. It provides excellent control over film thickness and composition, and it can be used to deposit films with high adhesion and uniformity.
- Limitations: The process can be more complex and expensive than thermal evaporation. It also requires precise control of the sputtering parameters to achieve the desired film properties.
-
Molecular Beam Epitaxy (MBE):
- Process: MBE is a highly controlled form of thermal evaporation where atomic or molecular beams are directed at a substrate in an ultra-high vacuum. The atoms or molecules condense on the substrate, forming a crystalline film.
- Applications: MBE is primarily used in the semiconductor industry for the growth of high-quality epitaxial layers. It is essential for the fabrication of advanced electronic and optoelectronic devices.
- Advantages: MBE allows for precise control over the composition and thickness of the deposited layers. It can produce films with extremely high purity and crystalline quality.
- Limitations: The process is slow and requires sophisticated equipment and ultra-high vacuum conditions, making it expensive and less suitable for large-scale production.
-
Ion Beam Sputtering Deposition (IBSD):
- Process: IBSD involves directing a focused ion beam at a target material, causing atoms to be ejected and deposited onto a substrate. The ion beam is typically generated by an ion source separate from the deposition chamber.
- Applications: IBSD is used in applications requiring high-precision and high-quality thin films, such as in the production of optical coatings and magnetic storage media.
- Advantages: IBSD provides excellent control over film thickness and composition. It can produce films with very low defect densities and high adhesion.
- Limitations: The process is complex and requires specialized equipment, making it more expensive and less commonly used than other sputtering techniques.
In summary, vapor phase techniques like thermal evaporation and sputtering are fundamental to the production of high-quality thin films and coatings. Each method has its unique advantages and limitations, making them suitable for different applications and industries. Understanding these techniques allows for the selection of the most appropriate method based on the specific requirements of the application.
Summary Table:
Technique | Process Overview | Applications | Advantages | Limitations |
---|---|---|---|---|
Thermal Evaporation | Heating material in a vacuum until vaporization; vapor condenses on substrate. | Optical coatings, semiconductor devices. | Simple, cost-effective, high deposition rates. | Requires high vacuum; limited for complex compounds. |
Sputtering | Bombarding target with high-energy ions; ejected atoms deposit on substrate. | Electronics, solar panels, flat-panel displays. | Wide material range, excellent control over film properties. | Complex, expensive, requires precise parameter control. |
MBE | Atomic/molecular beams condense on substrate in ultra-high vacuum. | Semiconductor industry, advanced electronic devices. | High purity, precise control over composition and thickness. | Slow, expensive, requires ultra-high vacuum. |
IBSD | Focused ion beam ejects target atoms, depositing them on substrate. | Optical coatings, magnetic storage media. | High precision, low defect densities, excellent adhesion. | Complex, expensive, specialized equipment required. |
Need help selecting the right vapor phase technique for your application? Contact our experts today!