The three primary methods for depositing carbon nanotubes (CNTs) are chemical vapor deposition (CVD), laser ablation, and arc discharge. Among these, CVD is the most widely used due to its cost-effectiveness, structural controllability, and scalability. Laser ablation and arc discharge are traditional methods but are less favored in commercial applications due to higher costs and lower efficiency. Emerging methods, such as using green or waste feedstocks, are being explored to reduce environmental impacts. Each method has unique advantages and limitations, making them suitable for different applications and research contexts.
Key Points Explained:
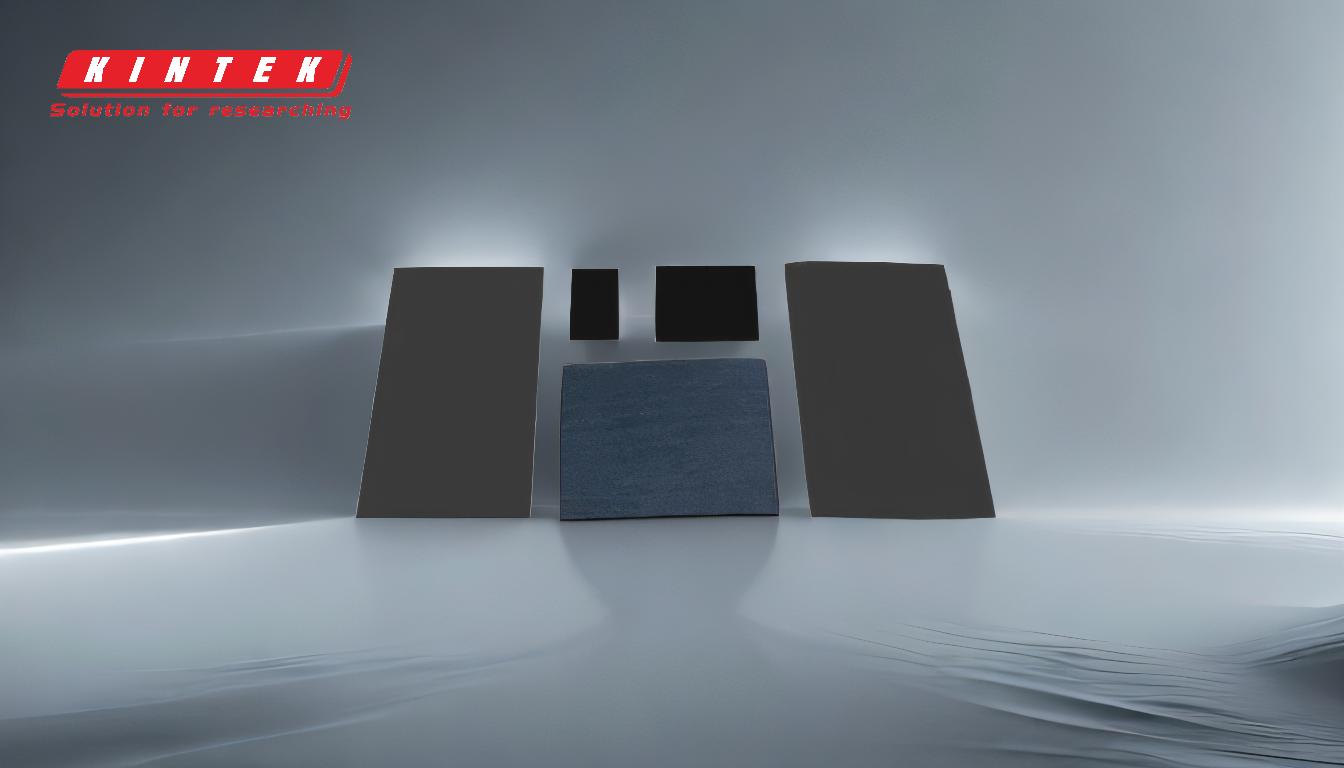
-
Chemical Vapor Deposition (CVD):
- Process: CVD involves the decomposition of hydrocarbon gases at high temperatures in the presence of a catalyst, typically metal nanoparticles, to form CNTs.
-
Advantages:
- High structural controllability, allowing for the synthesis of CNTs with specific diameters and lengths.
- Cost-effective and scalable, making it the dominant commercial method.
- Can be optimized to reduce environmental impacts by limiting material and energy consumption.
-
Limitations:
- Requires precise control of temperature and gas flow rates.
- Potential ecotoxicity impacts due to the use of catalysts and hydrocarbon gases.
-
Laser Ablation:
- Process: Laser ablation involves using a high-power laser to vaporize a carbon target in the presence of a catalyst, producing CNTs.
-
Advantages:
- Produces high-quality CNTs with fewer defects compared to other methods.
- Suitable for research purposes where high purity is required.
-
Limitations:
- High energy consumption and cost, making it less suitable for large-scale production.
- Limited scalability and efficiency.
-
Arc Discharge:
- Process: Arc discharge involves creating an electric arc between two carbon electrodes in an inert gas atmosphere, resulting in the formation of CNTs.
-
Advantages:
- Simple and relatively inexpensive setup.
- Produces multi-walled CNTs with good structural integrity.
-
Limitations:
- Low yield and difficulty in controlling the size and structure of CNTs.
- High energy consumption and production of amorphous carbon as a byproduct.
-
Emerging Methods:
- Green or Waste Feedstocks: Emerging methods focus on using sustainable feedstocks, such as carbon dioxide captured by electrolysis in molten salts or methane pyrolysis, to produce CNTs.
-
Advantages:
- Potential to reduce environmental impacts by utilizing waste materials or renewable resources.
- Aligns with the growing emphasis on sustainability in materials science.
-
Limitations:
- Still in the research and development phase, with limited commercial viability.
- Requires further optimization to achieve cost-effectiveness and scalability.
In summary, while CVD remains the most practical and widely used method for CNT deposition, laser ablation and arc discharge are valuable for specific research applications. Emerging methods using green or waste feedstocks represent a promising direction for reducing the environmental footprint of CNT production.
Summary Table:
Method | Process | Advantages | Limitations |
---|---|---|---|
Chemical Vapor Deposition (CVD) | Decomposes hydrocarbon gases at high temperatures with a catalyst. | Cost-effective, scalable, high structural controllability. | Requires precise control; potential ecotoxicity. |
Laser Ablation | Uses a high-power laser to vaporize a carbon target with a catalyst. | Produces high-quality CNTs with fewer defects. | High energy consumption; limited scalability. |
Arc Discharge | Creates an electric arc between carbon electrodes in an inert gas atmosphere. | Simple setup; produces multi-walled CNTs with good structural integrity. | Low yield; high energy consumption; produces amorphous carbon as a byproduct. |
Emerging Methods | Uses green or waste feedstocks for sustainable CNT production. | Reduces environmental impacts; aligns with sustainability goals. | Limited commercial viability; requires further optimization. |
Interested in learning more about carbon nanotube deposition methods? Contact us today to discuss your specific needs!