Induction furnaces are widely used in industrial applications for melting metals and alloys. The two main types of induction furnaces are core-type (or channel) induction furnaces and coreless-type induction furnaces. Each type has distinct characteristics, applications, and advantages, making them suitable for specific industrial needs. Core-type furnaces are typically used for melting low melting point alloys or as holding units, while coreless furnaces are more versatile and used for a broader range of applications, including steelmaking.
Key Points Explained:
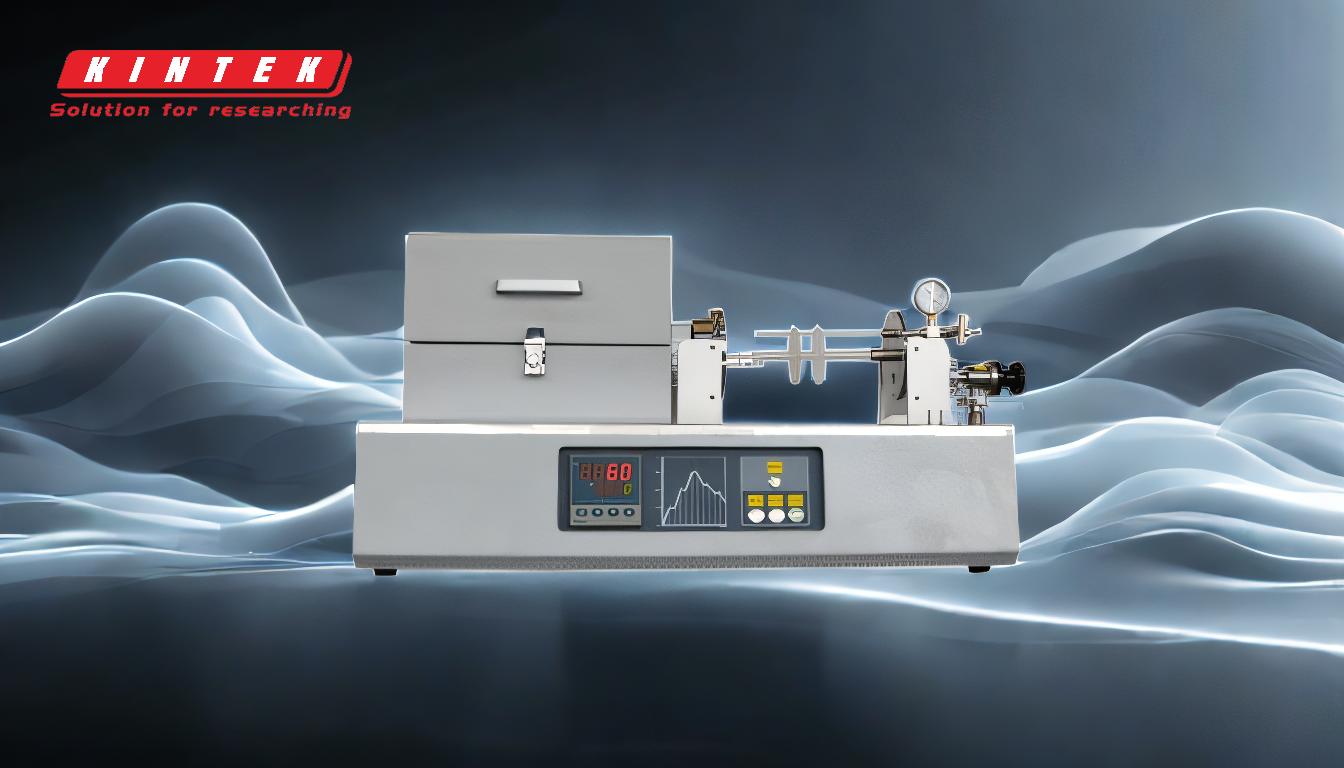
-
Core-Type (Channel) Induction Furnaces:
- Design and Functionality: Core-type induction furnaces, also known as channel furnaces, feature a core made of magnetic material (like iron) that surrounds a channel filled with molten metal. The core helps in concentrating the magnetic field, which induces currents in the molten metal, generating heat.
- Applications: These furnaces are primarily used for melting low melting point alloys, such as aluminum and zinc. They are also employed as holding and superheating units for higher melting point alloys like cast iron.
-
Advantages:
- High energy efficiency due to the concentrated magnetic field.
- Suitable for continuous operation, making them ideal for holding and superheating applications.
- Lower operating costs for specific alloys.
-
Limitations:
- Limited to specific alloys and lower melting point metals.
- Not suitable for rapid melting or frequent alloy changes.
-
Coreless-Type Induction Furnaces:
- Design and Functionality: Coreless induction furnaces do not have a magnetic core. Instead, they use a coil to generate an alternating magnetic field, which induces eddy currents directly in the metal charge, causing it to melt. The absence of a core allows for greater flexibility in the furnace design.
- Applications: These furnaces are highly versatile and are used for melting a wide range of metals, including steel, iron, copper, and aluminum. They are particularly favored in steelmaking and foundry applications.
-
Advantages:
- Versatility in handling different metals and alloys.
- Rapid melting capabilities, making them suitable for batch processes.
- Easy to clean and change alloys, which is beneficial for foundries with diverse production needs.
-
Limitations:
- Higher energy consumption compared to core-type furnaces.
- Less efficient for holding and superheating applications.
-
Comparison of Core-Type and Coreless-Type Induction Furnaces:
- Efficiency: Core-type furnaces are more energy-efficient for specific applications, while coreless furnaces offer greater flexibility at the cost of higher energy consumption.
- Versatility: Coreless furnaces are more versatile and can handle a wider range of metals and alloys, making them suitable for diverse industrial applications.
- Operational Costs: Core-type furnaces generally have lower operating costs for specific alloys, whereas coreless furnaces may incur higher costs due to their broader application range and energy usage.
-
Industrial Applications:
- Core-Type Furnaces: Commonly used in industries that require continuous melting or holding of low melting point alloys, such as aluminum foundries and zinc processing plants.
- Coreless Furnaces: Widely used in steelmaking, iron foundries, and other industries that require rapid melting and flexibility in handling various metals.
By understanding the differences between these two types of induction furnaces, industries can make informed decisions about which type best suits their specific melting and processing needs.
Summary Table:
Feature | Core-Type Induction Furnace | Coreless Induction Furnace |
---|---|---|
Design | Magnetic core surrounds a molten metal channel | No magnetic core; uses a coil for induction |
Applications | Low melting point alloys (e.g., aluminum, zinc) | Wide range of metals (e.g., steel, iron, copper) |
Advantages | High energy efficiency, continuous operation | Versatile, rapid melting, easy alloy changes |
Limitations | Limited to specific alloys, slower melting | Higher energy consumption, less efficient for holding |
Industrial Use | Aluminum foundries, zinc processing | Steelmaking, iron foundries |
Need help choosing the right induction furnace for your industrial needs? Contact our experts today!