Physical Vapor Deposition (PVD) is a widely used technique for depositing thin films onto substrates, and it is categorized into two primary types: thermal evaporation and sputtering. These methods differ in their mechanisms of material vaporization and deposition. Thermal evaporation involves heating a material until it vaporizes, which then condenses onto the substrate. Sputtering, on the other hand, uses a plasma to eject atoms from a target material, which then deposit onto the substrate. Both methods are conducted in a vacuum environment to ensure high-quality film deposition. PVD is often chosen over Chemical Vapor Deposition (CVD) for its ability to operate at lower temperatures and produce films with fewer impurities.
Key Points Explained:
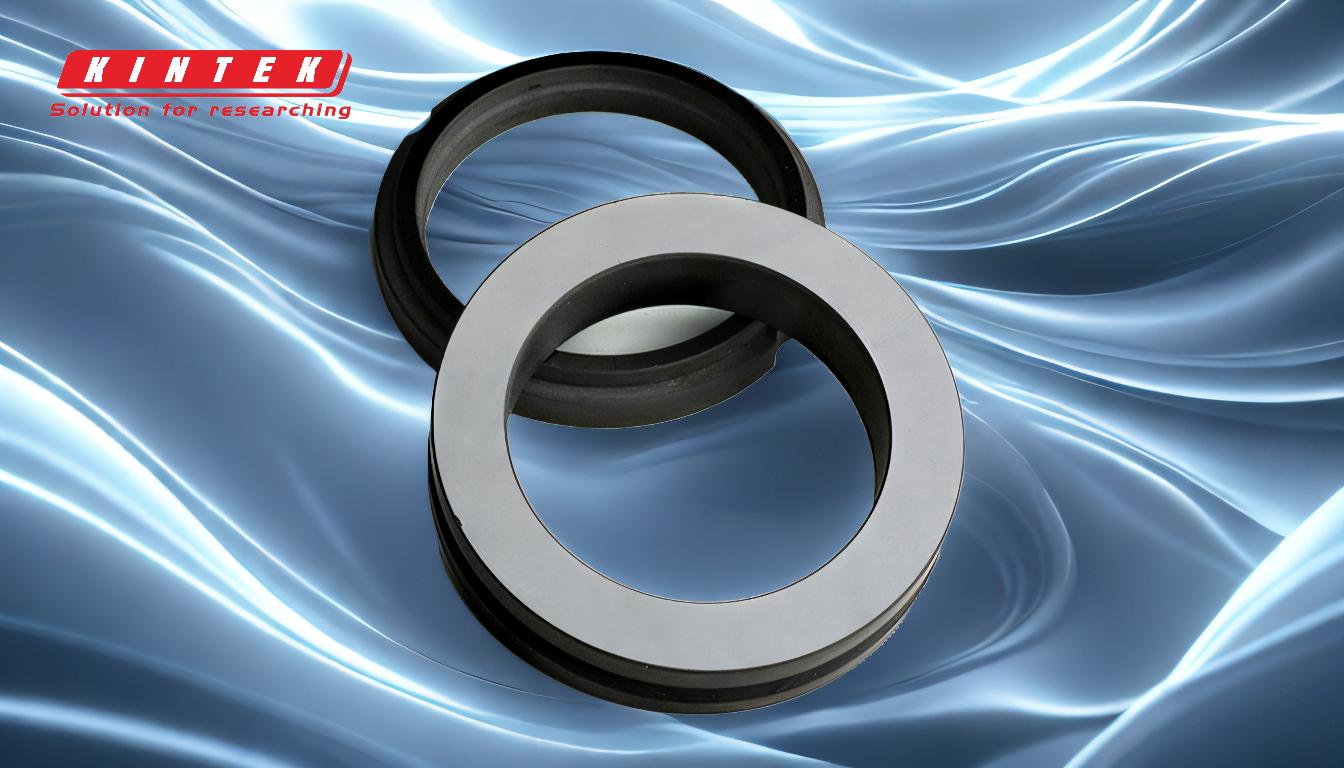
-
Thermal Evaporation:
- Process: In thermal evaporation, the material to be deposited is heated in a vacuum until it vaporizes. The vapor then travels through the vacuum and condenses on the substrate, forming a thin film.
- Advantages: This method is relatively simple and can deposit a wide range of materials, including metals, alloys, and some organic compounds. It is particularly useful for applications requiring high-purity films.
- Limitations: Thermal evaporation is a line-of-sight process, meaning it is less effective for coating complex geometries or areas not directly in the line of sight of the vapor source.
-
Sputtering:
- Process: Sputtering involves bombarding a target material with high-energy ions (usually from a plasma) to eject atoms from the target. These ejected atoms then deposit onto the substrate.
- Advantages: Sputtering can produce highly uniform and dense films, even on complex geometries. It is also capable of depositing a wide variety of materials, including metals, semiconductors, and insulators.
- Limitations: The process can be slower than thermal evaporation and may require more complex equipment, such as a microwave plasma chemical vapor deposition system, to generate the necessary plasma.
-
Comparison with CVD:
- Temperature: PVD processes, including thermal evaporation and sputtering, typically operate at lower temperatures (250°C~450°C) compared to CVD, which often requires temperatures between 450°C and 1050°C.
- Material State: PVD uses solid materials that are vaporized and then deposited, whereas CVD relies on gaseous precursors that react chemically to form the film.
- Environmental Impact: PVD is generally considered more environmentally friendly than CVD, as it does not produce corrosive gaseous byproducts.
-
Applications:
- Thermal Evaporation: Commonly used in the production of optical coatings, solar cells, and thin-film transistors.
- Sputtering: Widely used in the semiconductor industry, for creating hard coatings on tools, and in the production of decorative coatings.
-
Vacuum Environment:
- Both thermal evaporation and sputtering are conducted in a vacuum to minimize contamination and ensure the purity of the deposited film. The vacuum environment also helps in controlling the deposition rate and film quality.
In summary, the two primary types of PVD—thermal evaporation and sputtering—offer distinct advantages and are chosen based on the specific requirements of the application. While thermal evaporation is simpler and suitable for high-purity films, sputtering provides better coverage on complex geometries and is widely used in high-tech industries. Both methods are conducted in a vacuum to ensure optimal film quality and are generally more environmentally friendly compared to CVD.
Summary Table:
Aspect | Thermal Evaporation | Sputtering |
---|---|---|
Process | Material is heated to vaporize and condense on the substrate. | High-energy ions eject atoms from a target, which deposit onto the substrate. |
Advantages | Simple process, high-purity films, suitable for metals, alloys, and organic compounds. | Uniform and dense films, works on complex geometries, versatile material use. |
Limitations | Line-of-sight process, less effective for complex geometries. | Slower process, requires complex equipment like plasma systems. |
Applications | Optical coatings, solar cells, thin-film transistors. | Semiconductor industry, hard coatings, decorative coatings. |
Vacuum Environment | Conducted in a vacuum to ensure high-quality film deposition. | Conducted in a vacuum to minimize contamination and control deposition rate. |
Need help choosing the right PVD method for your application? Contact our experts today!