Thin films deposited by evaporation are a type of material layer created by heating a source material in a vacuum until it vaporizes, then allowing the vapor to condense onto a substrate, forming a thin, uniform layer. This technique is widely used in various industries, including electronics, optics, and coatings, due to its ability to produce high-purity films with precise thickness control. The process involves several steps, including vacuum creation, material heating, vaporization, and deposition. The resulting films can be tailored for specific applications by adjusting parameters such as temperature, pressure, and substrate material. This method is particularly valued for its simplicity, scalability, and ability to deposit a wide range of materials.
Key Points Explained:
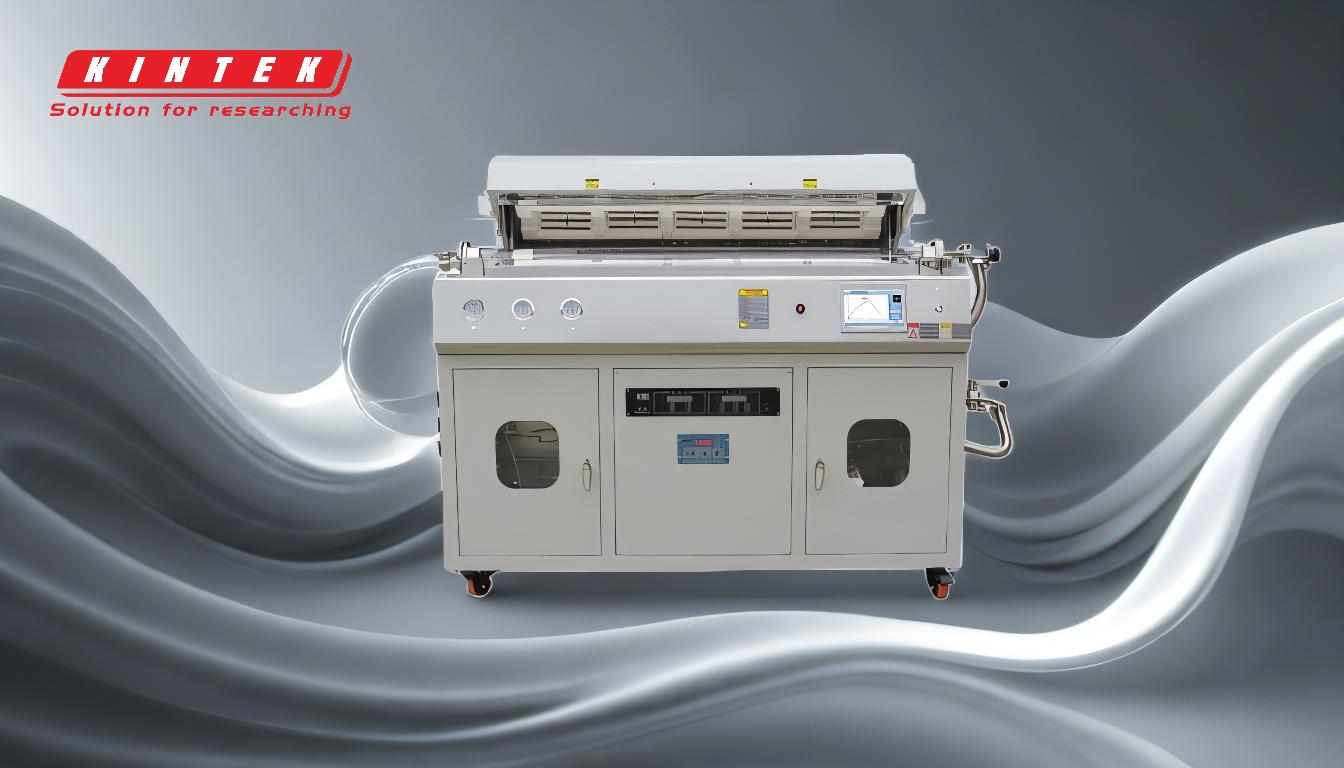
-
Definition of Thin Films Deposited by Evaporation:
- Thin films deposited by evaporation are ultra-thin layers of material created through a process where a source material is heated in a vacuum until it vaporizes. The vapor then condenses onto a substrate, forming a uniform film. This technique is essential in industries requiring precise material layers, such as semiconductors and optical coatings.
-
The Evaporation Process:
- The process begins with creating a vacuum environment to minimize contamination and ensure a clean deposition surface. The source material is then heated using methods such as resistive heating, electron beam heating, or laser ablation. As the material vaporizes, it travels through the vacuum and condenses on the substrate, forming a thin film. The thickness and uniformity of the film can be controlled by adjusting the evaporation rate and substrate temperature.
-
Types of Evaporation Techniques:
- Thermal Evaporation: Involves heating the source material using a resistive heater. This method is simple and cost-effective but is limited to materials with lower melting points.
- Electron Beam Evaporation: Uses a focused electron beam to heat the source material, allowing for the deposition of high-melting-point materials. This technique offers better control over deposition rates and film purity.
- Laser Ablation: Employs a high-energy laser to vaporize the source material. This method is suitable for complex materials and multi-layer structures.
-
Applications of Thin Films Deposited by Evaporation:
- Electronics: Used in the fabrication of semiconductors, solar cells, and thin-film transistors. The high purity and precise thickness control make it ideal for these applications.
- Optics: Applied in anti-reflective coatings, mirrors, and optical filters. The ability to deposit uniform films with specific optical properties is crucial in this field.
- Coatings: Utilized for protective and decorative coatings on various surfaces, including metals, glass, and plastics. The films can enhance durability, corrosion resistance, and aesthetic appeal.
-
Advantages of Evaporation Deposition:
- High Purity: The vacuum environment minimizes contamination, resulting in high-purity films.
- Precise Thickness Control: The deposition rate and time can be finely tuned to achieve the desired film thickness.
- Versatility: A wide range of materials, including metals, semiconductors, and insulators, can be deposited using this method.
- Scalability: The process can be scaled up for industrial production, making it suitable for large-scale applications.
-
Challenges and Limitations:
- Material Limitations: Some materials may decompose or react during the heating process, limiting their use in evaporation deposition.
- Uniformity Issues: Achieving uniform film thickness over large areas can be challenging, especially for complex geometries.
- Cost: High-vacuum systems and specialized equipment can be expensive, particularly for electron beam and laser ablation techniques.
-
Future Trends and Innovations:
- Advanced Materials: Research is ongoing to develop new materials and composites that can be deposited using evaporation techniques, expanding the range of applications.
- Process Optimization: Improvements in vacuum technology, heating methods, and deposition control are expected to enhance the efficiency and quality of thin films.
- Integration with Other Techniques: Combining evaporation deposition with other thin-film deposition methods, such as sputtering or chemical vapor deposition, could lead to the development of hybrid processes with enhanced capabilities.
In summary, thin films deposited by evaporation are a critical technology in modern manufacturing and research. The process offers high purity, precise control, and versatility, making it indispensable in fields such as electronics, optics, and coatings. While there are challenges, ongoing advancements in materials and techniques continue to expand the potential applications and effectiveness of this method.
Summary Table:
Aspect | Details |
---|---|
Definition | Ultra-thin layers created by vaporizing a source material in a vacuum. |
Process | Vacuum creation, material heating, vaporization, and deposition. |
Techniques | Thermal, electron beam, and laser ablation evaporation. |
Applications | Electronics, optics, and protective/decorative coatings. |
Advantages | High purity, precise thickness control, versatility, and scalability. |
Challenges | Material limitations, uniformity issues, and high equipment costs. |
Future Trends | Advanced materials, process optimization, and hybrid deposition methods. |
Discover how thin films deposited by evaporation can enhance your projects—contact our experts today!