Sputtering is a highly advantageous technique for creating metal interconnect systems compared to evaporation. Two key advantages of sputtering over evaporation include better adhesion of deposited films and the ability to deposit materials with very high melting points. Sputtering ensures stronger adhesion due to the higher kinetic energy of sputtered atoms, which leads to better bonding with the substrate. Additionally, sputtering can handle materials with extremely high melting points, which are challenging or impossible to evaporate. These advantages make sputtering a more versatile and reliable method for creating high-quality metal interconnect systems.
Key Points Explained:
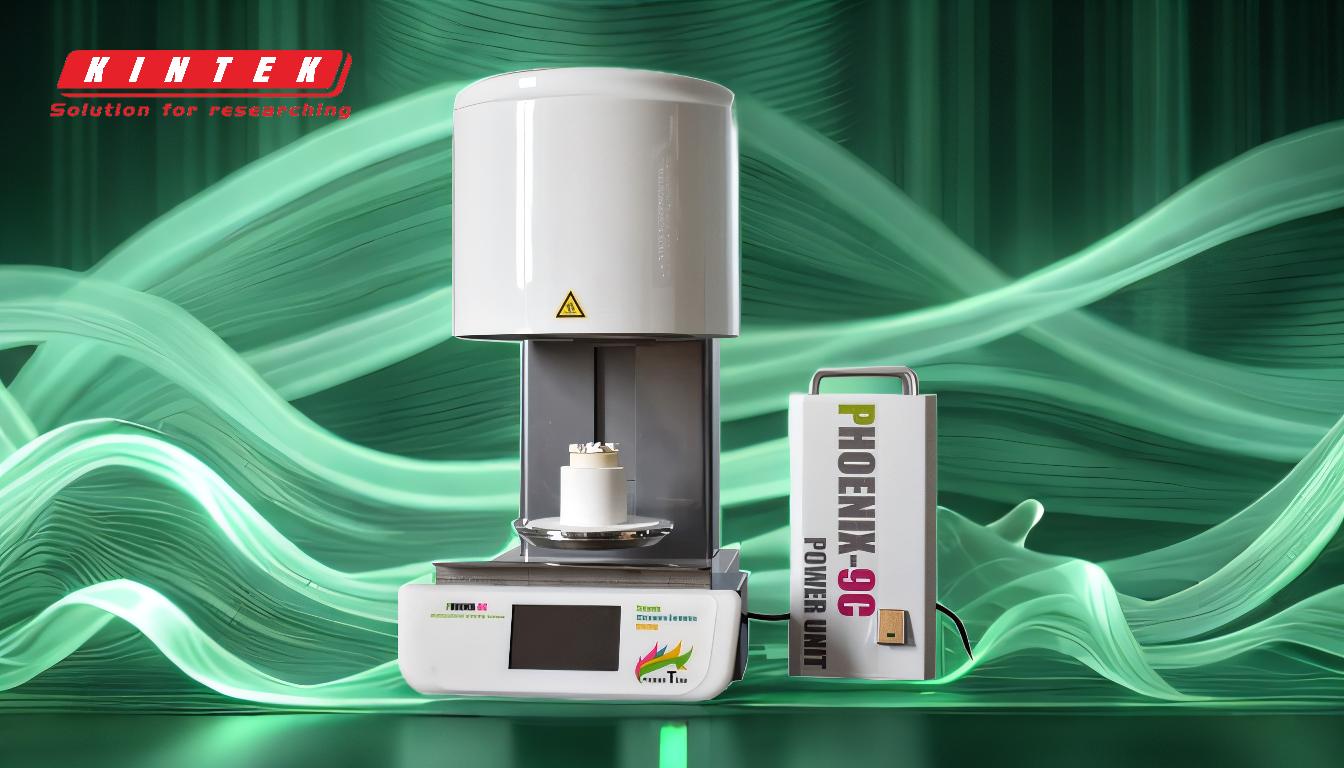
-
Better Adhesion of Deposited Films
- Sputtered atoms have significantly higher kinetic energy compared to evaporated materials. This higher energy results in stronger bonding with the substrate, leading to better adhesion.
- Better adhesion is critical in metal interconnect systems, as it ensures the durability and reliability of the deposited films, reducing the risk of delamination or failure during operation.
- Unlike evaporation, sputtering allows for both bottom-up and top-down deposition, further enhancing the uniformity and adhesion of the films.
-
Ability to Deposit Materials with Very High Melting Points
- Sputtering can deposit materials with extremely high melting points, which are difficult or impossible to evaporate using traditional thermal or e-beam evaporation techniques.
- This capability is particularly important for advanced applications in semiconductor manufacturing, where materials like tungsten or refractory metals are often required for interconnects.
- The composition of sputtered films closely matches the source material, ensuring consistency and precision in the deposited layers.
-
Additional Advantages Supporting Metal Interconnect Systems
- Reproducibility and Process Control: Sputtering offers excellent reproducibility and simpler process automation, making it easier to achieve consistent results in large-scale manufacturing.
- Compatibility with Reactive Gases: Sputtering can be performed in the presence of reactive gases, enabling the deposition of oxide or nitride layers with precise composition control.
- Uniformity and Packing Density: Sputtered films are more uniform and have higher packing densities, even at low temperatures, which is beneficial for creating high-performance interconnects.
- Maintenance-Free Operation: Sputtering systems are maintenance-free and compatible with ultrahigh vacuum conditions, reducing downtime and operational costs.
These advantages make sputtering a superior choice for creating metal interconnect systems, ensuring high-quality, durable, and precise deposition of materials critical for modern semiconductor and electronic applications.
Summary Table:
Advantage | Description |
---|---|
Better Adhesion | Higher kinetic energy ensures stronger bonding with the substrate. |
High Melting Point Materials | Deposits materials like tungsten, which are challenging to evaporate. |
Reproducibility & Process Control | Offers consistent results and simpler automation for large-scale manufacturing. |
Reactive Gas Compatibility | Enables precise deposition of oxide or nitride layers. |
Uniformity & Packing Density | Produces uniform films with high packing density, even at low temperatures. |
Maintenance-Free Operation | Reduces downtime and operational costs with ultrahigh vacuum compatibility. |
Interested in enhancing your metal interconnect systems with sputtering? Contact our experts today to learn more!