The two most common methods to heat the source material in evaporation are resistive heating and electron beam heating. Resistive heating involves passing a high current through a refractory metal element (such as tungsten, molybdenum, or graphite) to generate heat via Joule heating, which then evaporates the material. Electron beam heating, on the other hand, uses a focused beam of high-energy electrons to directly heat and evaporate the source material. Both methods are widely used in thermal evaporation processes, with resistive heating being simpler and more cost-effective, while electron beam heating is preferred for materials with very high melting points or when precise control over evaporation is required.
Key Points Explained:
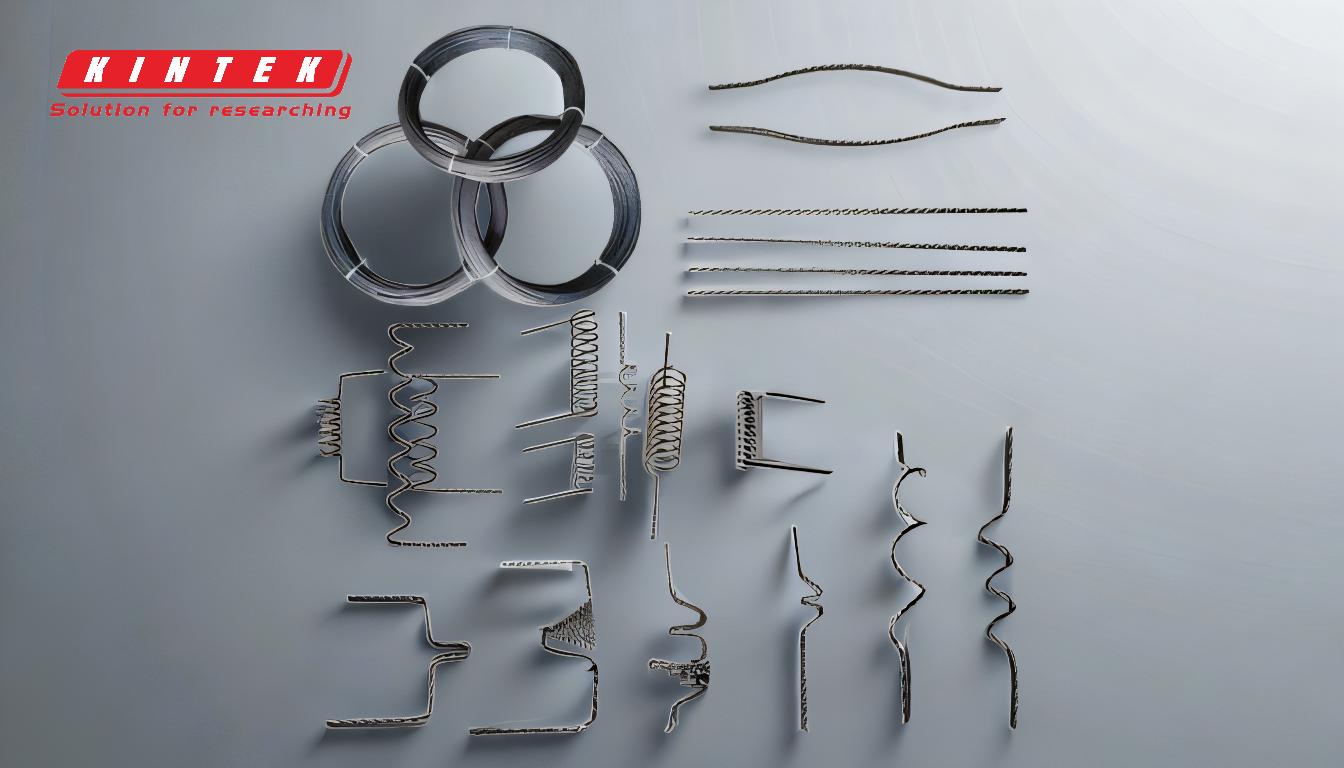
-
Resistive Heating Evaporation
- Mechanism: Resistive heating relies on Joule heating, where an electric current is passed through a high-melting-point conductor (e.g., tungsten, molybdenum, or graphite) to generate heat.
- Setup: The conductor is often shaped into a basket, boat, or filament, and the source material is placed directly on it.
-
Advantages:
- Simple and cost-effective.
- Suitable for materials with moderate melting points.
- Easy to control and maintain.
-
Limitations:
- Not ideal for materials with extremely high melting points.
- Potential contamination from the heating element.
-
Electron Beam (E-Beam) Heating Evaporation
- Mechanism: A focused beam of high-energy electrons is directed at the source material, transferring kinetic energy to the material and causing it to heat up and evaporate.
- Setup: The electron beam is generated by an electron gun, and the source material is placed in a crucible, often made of materials like copper or graphite.
-
Advantages:
- Capable of evaporating materials with very high melting points.
- Minimal contamination risk, as the electron beam does not physically contact the material.
- High precision and control over the evaporation process.
-
Limitations:
- More complex and expensive equipment.
- Requires a high vacuum environment for optimal operation.
-
Comparison of Resistive and Electron Beam Heating
- Material Compatibility: Resistive heating is better suited for materials with lower to moderate melting points, while electron beam heating excels with high-melting-point materials.
- Cost and Complexity: Resistive heating is simpler and more economical, making it a preferred choice for many applications. Electron beam heating, while more expensive, offers superior control and is indispensable for specialized applications.
- Contamination Risk: Resistive heating may introduce contamination from the heating element, whereas electron beam heating minimizes this risk due to its non-contact nature.
-
Applications and Use Cases
- Resistive Heating: Commonly used in thin-film deposition for semiconductors, optical coatings, and decorative coatings.
- Electron Beam Heating: Ideal for advanced applications such as high-purity thin films, refractory metal coatings, and specialized research requiring precise material control.
-
Factors Influencing Choice of Heating Method
- Material Properties: Melting point, reactivity, and vapor pressure of the source material.
- Deposition Requirements: Desired film thickness, uniformity, and purity.
- Operational Constraints: Budget, equipment availability, and required vacuum conditions.
By understanding these two primary heating methods, equipment and consumable purchasers can make informed decisions based on their specific application needs, material properties, and operational constraints.
Summary Table:
Aspect | Resistive Heating | Electron Beam Heating |
---|---|---|
Mechanism | Joule heating via electric current through a refractory metal (e.g., tungsten). | High-energy electron beam directly heats the source material. |
Advantages | Simple, cost-effective, easy to control. | High precision, minimal contamination, ideal for high-melting-point materials. |
Limitations | Not suitable for very high melting points; potential contamination. | Complex, expensive, requires high vacuum. |
Applications | Thin-film deposition, semiconductors, optical coatings. | High-purity thin films, refractory metal coatings, specialized research. |
Need help choosing the right heating method for your application? Contact our experts today!