Physical vapor deposition (PVD) is a versatile and widely used technique for depositing thin films of materials onto substrates in a vacuum environment. This process is essential in various industries due to its ability to produce high-purity, durable, and functional coatings. PVD is employed in microelectronics, optics, material research, solar-cell production, decorative coatings, and aerospace technology. It enhances the properties of substrates, such as wear resistance, hardness, oxidation resistance, and scratch resistance, making it invaluable in applications ranging from automotive parts and cutting tools to jewelry and medical devices.
Key Points Explained:
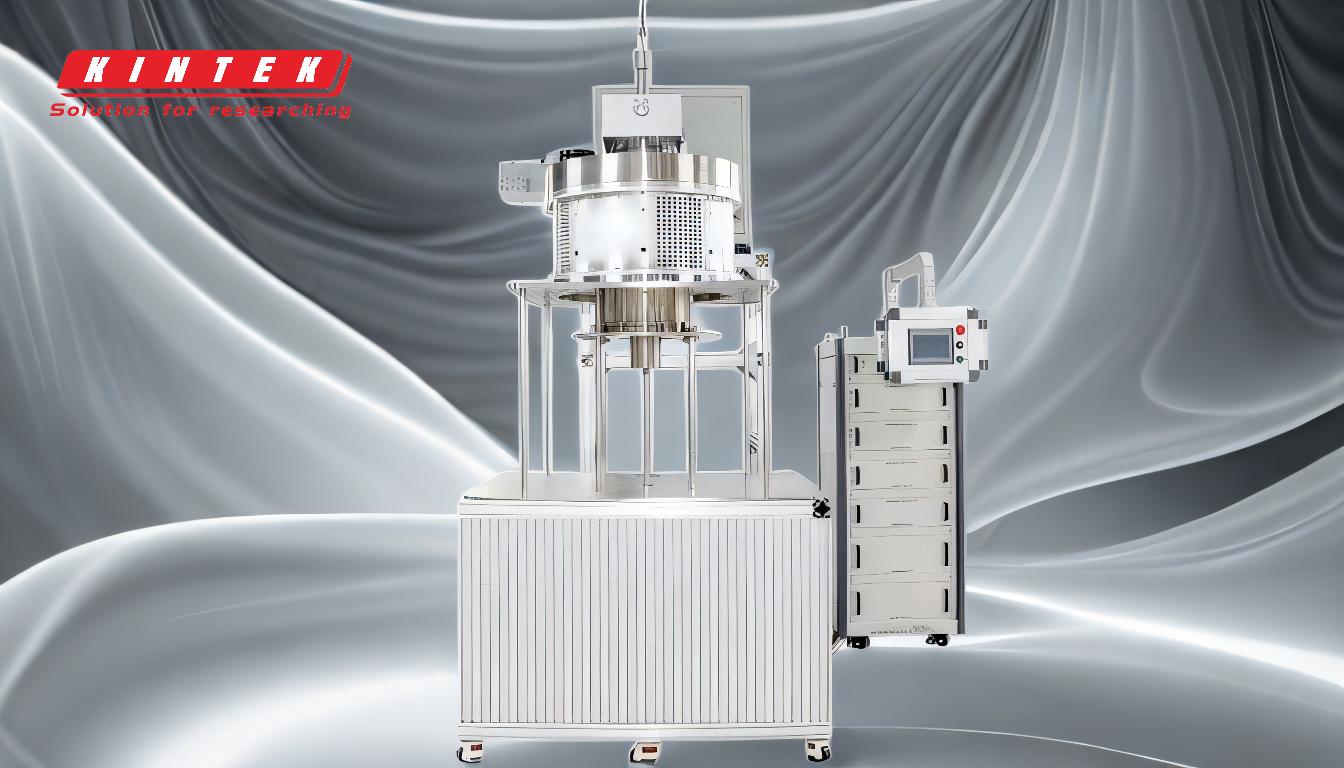
-
Fundamentals of PVD:
- PVD involves the vaporization of a target material in a vacuum environment, followed by the condensation of the vaporized atoms onto a substrate to form a thin film.
- Techniques such as electron-beam evaporation and sputter deposition are commonly used in PVD processes.
- The process requires a vacuum chamber, a high-voltage DC power supply, and a substrate connected to the negative voltage of the power supply.
-
Applications in Microelectronics and Optics:
- PVD is extensively used in the production of thin films for microelectronic devices, including semiconductors and integrated circuits.
- In optics, PVD is used to create coatings that enhance the performance of lenses, mirrors, and other optical components by improving their reflectivity, transparency, or durability.
-
Solar-Cell Production:
- PVD plays a crucial role in the manufacturing of thin-film solar cells, where it deposits high-purity layers of materials like silicon, cadmium telluride, or copper indium gallium selenide onto substrates.
- These thin films are essential for converting sunlight into electricity efficiently.
-
Decorative and Tribological Coatings:
- PVD is widely used to create decorative coatings on products such as jewelry, door and window hardware, kitchen and bathroom fixtures, and marine supplies.
- Tribological coatings, which improve wear resistance and reduce friction, are applied to automotive parts, cutting tools, and forming tools.
-
Aerospace and High-Temperature Applications:
- PVD coatings are used in aerospace technology to enhance the resistance of components to high temperatures, ablation, and corrosion.
- These coatings are critical for improving the performance and longevity of aerospace components exposed to extreme conditions.
-
Medical Devices and Holographic Displays:
- PVD is employed in the production of coatings for medical devices, such as stents and surgical instruments, to improve biocompatibility and durability.
- It is also used in the fabrication of holographic displays, where precise thin films are required to create high-quality images.
-
Innovative and Emerging Applications:
- PVD technology is continually evolving, with new applications emerging in fields such as electronic packaging, automotive sensors, and advanced material research.
- These innovative uses leverage the unique properties of PVD coatings, such as their ability to provide tailored surface properties and high-purity materials.
In summary, physical vapor deposition is a critical technology with a broad range of applications across multiple industries. Its ability to produce durable, high-performance coatings makes it indispensable in modern manufacturing and research.
Summary Table:
Application | Key Benefits |
---|---|
Microelectronics | High-purity thin films for semiconductors and integrated circuits |
Optics | Enhanced reflectivity, transparency, and durability for lenses and mirrors |
Solar-Cell Production | Efficient sunlight-to-electricity conversion with high-purity thin films |
Decorative Coatings | Durable and aesthetic finishes for jewelry, fixtures, and hardware |
Aerospace | High-temperature, ablation, and corrosion resistance for extreme conditions |
Medical Devices | Biocompatible and durable coatings for stents and surgical tools |
Holographic Displays | Precise thin films for high-quality image creation |
Emerging Applications | Tailored surface properties for electronic packaging, sensors, and material research |
Unlock the potential of PVD for your industry—contact us today to learn more!