The growth of carbon nanotubes (CNTs) using chemical vapor deposition (CVD) is a widely adopted method due to its cost-effectiveness, controllability, and scalability. A critical component of this process is the catalyst, which plays a pivotal role in the decomposition of carbon-containing gases and the subsequent formation of CNTs. The choice of catalyst significantly influences the quality, yield, and properties of the CNTs. Transition metals such as iron (Fe), nickel (Ni), and cobalt (Co) are commonly used due to their ability to efficiently catalyze the decomposition of hydrocarbons and facilitate carbon nanotube growth. The synthesis process, while effective, must also consider environmental impacts, such as energy consumption and greenhouse gas emissions, to ensure sustainability.
Key Points Explained:
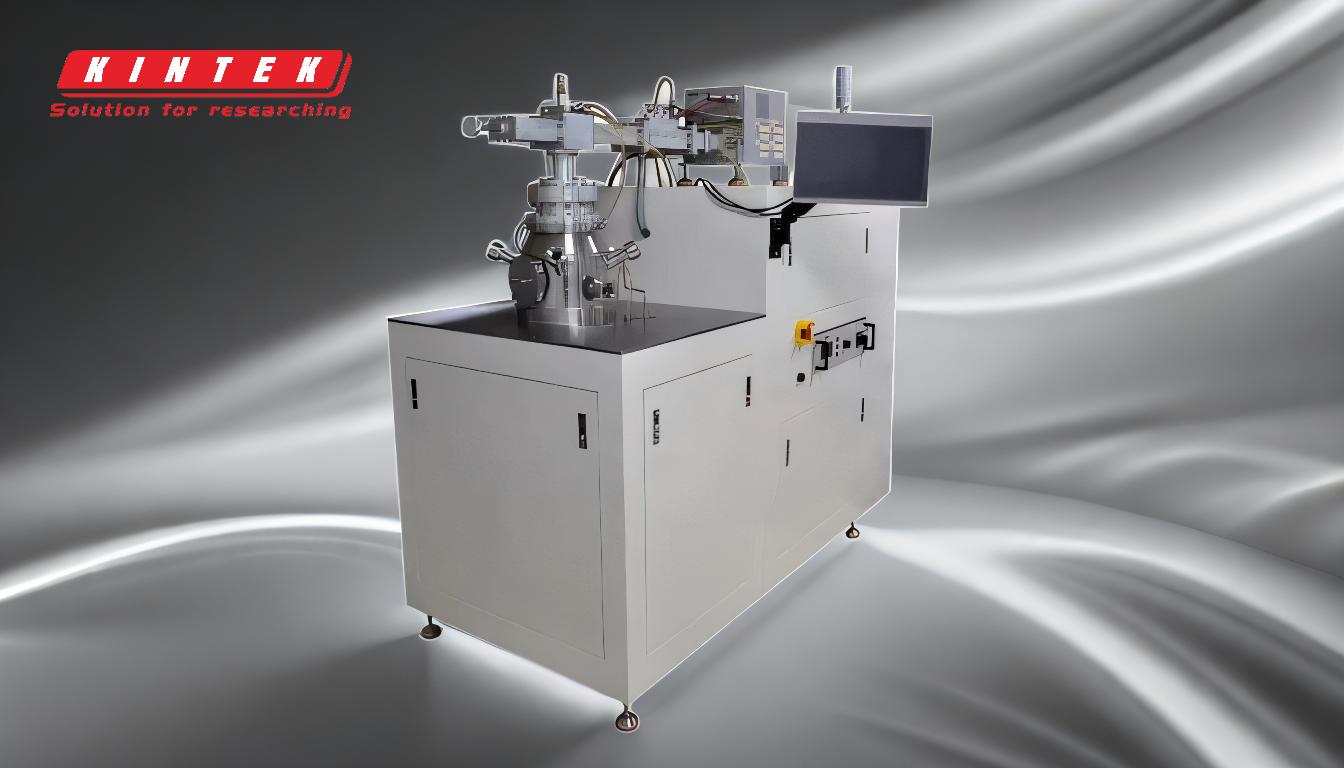
-
Role of Catalysts in CNT Growth:
- Catalysts are essential for the decomposition of carbon-containing gases (e.g., methane, ethylene, or acetylene) during the CVD process.
- They provide active sites for carbon atoms to nucleate and form the tubular structure of CNTs.
- The catalyst's composition, size, and morphology directly affect the diameter, length, and chirality of the CNTs.
-
Commonly Used Catalysts:
- Iron (Fe): Widely used due to its high catalytic activity and ability to produce high-quality CNTs. It is often supported on substrates like alumina or silica to enhance stability and dispersion.
- Nickel (Ni): Known for its ability to grow multi-walled carbon nanotubes (MWCNTs) with high yields. It is also effective in producing single-walled carbon nanotubes (SWCNTs) under specific conditions.
- Cobalt (Co): Often used in combination with other metals (e.g., Fe or Ni) to improve catalytic performance and control the growth of CNTs with specific properties.
-
Catalyst Deposition and Preparation:
- Catalysts are typically deposited as nanoparticles on a substrate (e.g., silicon, quartz, or alumina) to provide a controlled environment for CNT growth.
- Techniques such as sputtering, evaporation, or solution-based methods are used to deposit the catalyst.
- The size of the catalyst nanoparticles is critical, as it determines the diameter of the CNTs. Smaller nanoparticles generally produce narrower CNTs.
-
Environmental and Energy Considerations:
- The CVD process involves high temperatures (600–1000°C) and energy-intensive steps, which contribute to its environmental footprint.
- Optimizing catalyst efficiency can reduce material consumption and energy requirements, thereby minimizing greenhouse gas emissions.
- Life cycle assessments (LCAs) are increasingly used to evaluate and improve the sustainability of CNT synthesis processes.
-
Advantages of Catalytic CVD:
- Structural Controllability: The use of catalysts allows for precise control over the diameter, length, and chirality of CNTs, which is crucial for tailoring their properties for specific applications.
- Scalability: Catalytic CVD is a scalable method suitable for industrial production, making it a preferred choice for large-scale CNT synthesis.
- Cost-Effectiveness: Compared to other methods like arc discharge or laser ablation, catalytic CVD is more economical due to lower energy and material costs.
-
Challenges and Future Directions:
- Catalyst Deactivation: Over time, catalysts can become deactivated due to carbon deposition or sintering, reducing their efficiency.
- Chirality Control: Achieving precise control over the chirality of SWCNTs remains a challenge, as it directly impacts their electronic properties.
- Sustainability: Research is ongoing to develop greener synthesis methods, such as using renewable carbon sources or reducing the reliance on high-energy processes.
In conclusion, the choice of catalyst is a critical factor in the growth of carbon nanotubes via chemical vapor deposition. Transition metals like iron, nickel, and cobalt are commonly used due to their catalytic efficiency and ability to produce high-quality CNTs. However, optimizing the synthesis process to minimize environmental impacts and improve sustainability remains an ongoing challenge. By addressing these issues, the production of CNTs can become more efficient, cost-effective, and environmentally friendly.
Summary Table:
Catalyst | Key Properties | Applications |
---|---|---|
Iron (Fe) | High catalytic activity, produces high-quality CNTs | Supported on substrates like alumina or silica |
Nickel (Ni) | High yield for MWCNTs, effective for SWCNTs under specific conditions | Used in industrial-scale CNT production |
Cobalt (Co) | Enhances catalytic performance, controls CNT properties | Often combined with Fe or Ni for improved results |
Want to learn more about CNT synthesis? Contact our experts today for tailored solutions!