Heat generation in a hydraulic system is primarily caused by inefficiencies in the system's operation, which convert mechanical energy into thermal energy. This process is unavoidable to some extent, but excessive heat can lead to system inefficiencies, component wear, and potential failure. Understanding the sources of heat generation is crucial for designing and maintaining efficient hydraulic systems. The main contributors to heat include fluid friction, mechanical friction, and energy losses during pressure drops across valves and orifices. Proper system design, component selection, and maintenance can help mitigate excessive heat generation and ensure optimal performance.
Key Points Explained:
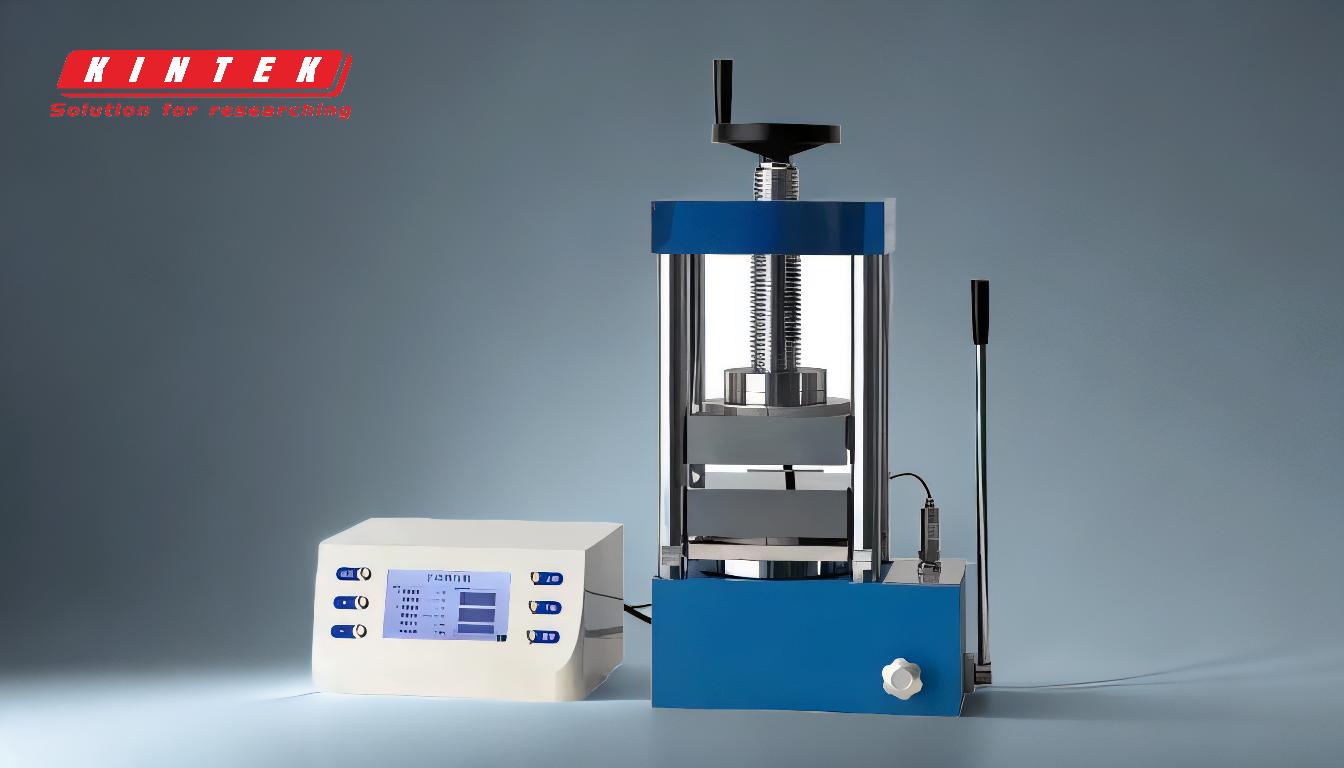
-
Fluid Friction:
- Explanation: As hydraulic fluid flows through the system, it encounters resistance from the walls of hoses, pipes, and other components. This resistance causes the fluid molecules to rub against each other and the surfaces, generating heat.
- Impact: High fluid friction can lead to significant heat buildup, especially in systems with long or narrow passages. Using smooth, appropriately sized hoses and pipes can reduce this friction.
- Mitigation: Selecting the right viscosity of hydraulic fluid and ensuring proper flow rates can minimize fluid friction and associated heat generation.
-
Mechanical Friction:
- Explanation: Mechanical components such as pumps, motors, and cylinders have moving parts that rub against each other. This friction generates heat as a byproduct of mechanical energy conversion.
- Impact: Excessive mechanical friction can lead to component wear, reduced efficiency, and increased operating temperatures.
- Mitigation: Regular lubrication, proper alignment, and using high-quality components can reduce mechanical friction and heat generation.
-
Pressure Drops Across Valves and Orifices:
- Explanation: When hydraulic fluid passes through valves, orifices, or other restrictions, it experiences a pressure drop. This pressure drop converts potential energy into heat.
- Impact: Frequent or significant pressure drops can lead to substantial heat generation, especially in systems with complex control circuits.
- Mitigation: Optimizing valve sizing, reducing unnecessary restrictions, and using efficient control strategies can minimize pressure drops and associated heat.
-
Inefficient Pump Operation:
- Explanation: Hydraulic pumps can generate heat if they operate outside their optimal efficiency range. Overloading, cavitation, or running at excessive speeds can all contribute to heat buildup.
- Impact: Inefficient pump operation not only generates heat but also reduces the overall performance and lifespan of the pump.
- Mitigation: Ensuring the pump is correctly sized for the system, maintaining proper fluid levels, and avoiding cavitation can improve efficiency and reduce heat generation.
-
External Heat Sources:
- Explanation: Hydraulic systems operating in high-temperature environments or near heat sources can absorb external heat, further increasing the system's temperature.
- Impact: External heat can exacerbate internal heat generation, leading to overheating and potential system failure.
- Mitigation: Insulating the system, providing adequate ventilation, and using heat exchangers can help manage external heat influences.
-
System Design and Maintenance:
- Explanation: Poor system design, such as undersized components or inadequate cooling, can lead to excessive heat generation. Lack of maintenance, such as dirty filters or worn-out seals, can also contribute to inefficiencies and heat buildup.
- Impact: A poorly designed or maintained system will operate less efficiently and generate more heat, leading to increased wear and potential failures.
- Mitigation: Proper system design, regular maintenance, and timely replacement of worn components are essential for minimizing heat generation and ensuring long-term system reliability.
By understanding these key points, hydraulic system designers and operators can take proactive measures to reduce heat generation, improve efficiency, and extend the lifespan of the system.
Summary Table:
Cause of Heat | Explanation | Impact | Mitigation |
---|---|---|---|
Fluid Friction | Resistance from fluid flow through hoses, pipes, and components. | Significant heat buildup, especially in long or narrow passages. | Use smooth, appropriately sized hoses and pipes; select the right fluid viscosity. |
Mechanical Friction | Friction from moving parts like pumps, motors, and cylinders. | Component wear, reduced efficiency, and increased operating temperatures. | Regular lubrication, proper alignment, and high-quality components. |
Pressure Drops | Energy loss when fluid passes through valves, orifices, or restrictions. | Substantial heat generation in systems with complex control circuits. | Optimize valve sizing, reduce unnecessary restrictions, and use efficient controls. |
Inefficient Pump Operation | Overloading, cavitation, or running pumps outside optimal efficiency ranges. | Reduced pump performance, lifespan, and increased heat generation. | Proper pump sizing, maintain fluid levels, and avoid cavitation. |
External Heat Sources | Heat absorbed from high-temperature environments or nearby heat sources. | Exacerbates internal heat, leading to overheating and potential failure. | Insulate the system, provide ventilation, and use heat exchangers. |
System Design & Maintenance | Poor design (undersized components, inadequate cooling) or lack of maintenance. | Increased wear, inefficiencies, and heat buildup. | Proper design, regular maintenance, and timely replacement of worn components. |
Need help optimizing your hydraulic system to reduce heat generation? Contact our experts today for tailored solutions!