CVD (Chemical Vapor Deposition) and PVD (Physical Vapor Deposition) are advanced coating techniques used to deposit thin films on substrates, enhancing their functionality, durability, and resistance to external factors. While both methods aim to improve substrate performance, they differ significantly in their processes, bonding mechanisms, and suitability for specific materials. CVD involves chemical reactions at high temperatures, creating strong diffusion bonds, but it may not be suitable for temperature-sensitive materials. PVD, on the other hand, operates under vacuum conditions, making it versatile for a broader range of materials but with comparatively weaker bonds. Understanding these differences is crucial for selecting the appropriate technique based on the substrate and desired outcomes.
Key Points Explained:
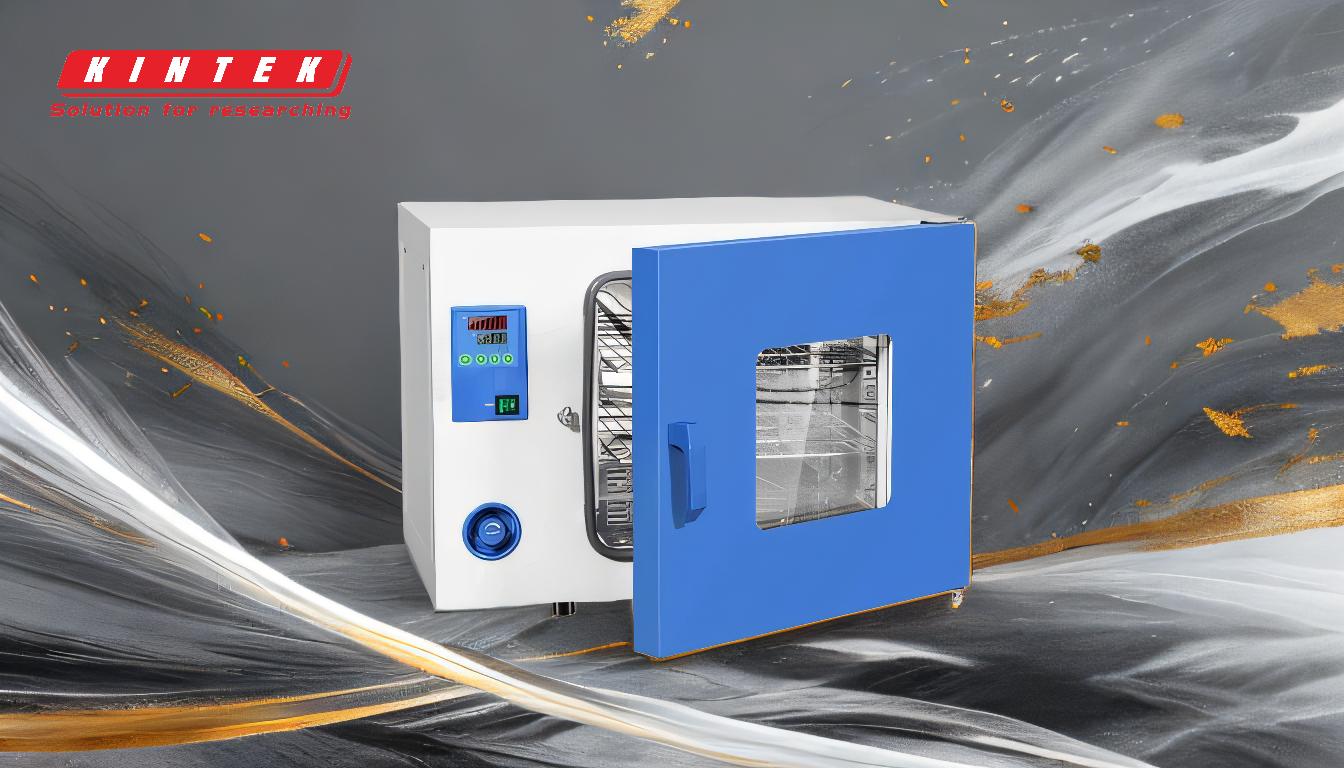
-
Definition and Purpose of CVD and PVD:
- CVD (Chemical Vapor Deposition): A process where a substrate is exposed to volatile precursors, which react or decompose to form a thin film on the substrate. This method is widely used to enhance substrate functionality, introduce new properties, and provide protection.
- PVD (Physical Vapor Deposition): A technique where material is physically vaporized from a solid source and deposited onto a substrate. PVD is used for similar purposes as CVD but relies on physical processes rather than chemical reactions.
-
Key Differences Between CVD and PVD:
-
Process Mechanism:
- CVD: Involves chemical reactions at high temperatures, allowing for non-line-of-sight deposition. This results in uniform layer structures and thickness homogeneity.
- PVD: Relies on physical vaporization and deposition, which is a line-of-sight process. This can lead to less uniform coatings compared to CVD.
-
Bonding Strength:
- CVD: Creates a diffusion-type bond between the coating and substrate, which is generally stronger and more durable.
- PVD: Forms a mechanical bond, which is typically weaker than the diffusion bond created by CVD.
-
Temperature Requirements:
- CVD: Requires high processing temperatures, which can limit its use with temperature-sensitive substrates.
- PVD: Operates under vacuum conditions and at lower temperatures, making it suitable for a wider range of materials, including those sensitive to heat.
-
Process Mechanism:
-
Applications and Suitability:
- CVD: Ideal for applications requiring strong, durable coatings and uniform thickness, such as in semiconductor manufacturing, protective coatings, and high-temperature environments.
- PVD: Suitable for applications where lower processing temperatures are necessary, such as in the coating of plastics, optical components, and decorative finishes.
-
Advantages and Limitations:
-
CVD Advantages:
- Stronger bonding and more durable coatings.
- Non-line-of-sight process ensures uniform coating thickness.
-
CVD Limitations:
- High processing temperatures restrict use with temperature-sensitive materials.
-
PVD Advantages:
- Lower processing temperatures allow for use with a broader range of materials.
- Versatile and suitable for complex geometries.
-
PVD Limitations:
- Weaker bonding compared to CVD.
- Line-of-sight process can result in less uniform coatings.
-
CVD Advantages:
-
Choosing Between CVD and PVD:
- The choice between CVD and PVD depends on the specific requirements of the application, including the substrate material, desired coating properties, and processing constraints. For high-strength, durable coatings on heat-resistant substrates, CVD is often preferred. For temperature-sensitive materials or applications requiring lower processing temperatures, PVD is the better option.
By understanding these key points, equipment and consumable purchasers can make informed decisions about which coating technique best suits their needs, ensuring optimal performance and cost-effectiveness.
Summary Table:
Aspect | CVD (Chemical Vapor Deposition) | PVD (Physical Vapor Deposition) |
---|---|---|
Process Mechanism | Chemical reactions at high temperatures; non-line-of-sight deposition | Physical vaporization and deposition; line-of-sight process |
Bonding Strength | Strong diffusion-type bond | Mechanical bond (weaker than CVD) |
Temperature | High processing temperatures; not suitable for heat-sensitive materials | Lower temperatures; suitable for heat-sensitive materials |
Applications | Semiconductor manufacturing, protective coatings, high-temperature environments | Plastics, optical components, decorative finishes |
Advantages | Stronger bonding, uniform coating thickness | Lower temperatures, versatile for complex geometries |
Limitations | High temperatures limit use with heat-sensitive materials | Weaker bonding, less uniform coatings |
Need help choosing the right coating technique for your application? Contact our experts today!