The Spark Plasma Sintering (SPS) process is an advanced powder metallurgy technique that utilizes electric current and pressure to synthesize materials in a single step. It is also known by other names such as Pulsed Electric Current Sintering (PECS), Field Assisted Sintering Technique (FAST), or Plasma-Activated Sintering (PAS). The process involves a modified hot pressing setup where an electric current flows directly through the pressing die (typically graphite) and the component, enabling rapid heating and short processing times. SPS is characterized by precise control over temperature, pressure, and heating rate, allowing for the creation of materials with unique microstructures and properties. The process operates in a vacuum or controlled atmosphere to prevent oxidation and ensure material purity. It typically involves four main stages: vacuum creation, pressure application, resistive heating, and cooling. The "spark plasma effect" plays a key role in inhibiting particle growth and facilitating the formation of unique material compositions.
Key Points Explained:
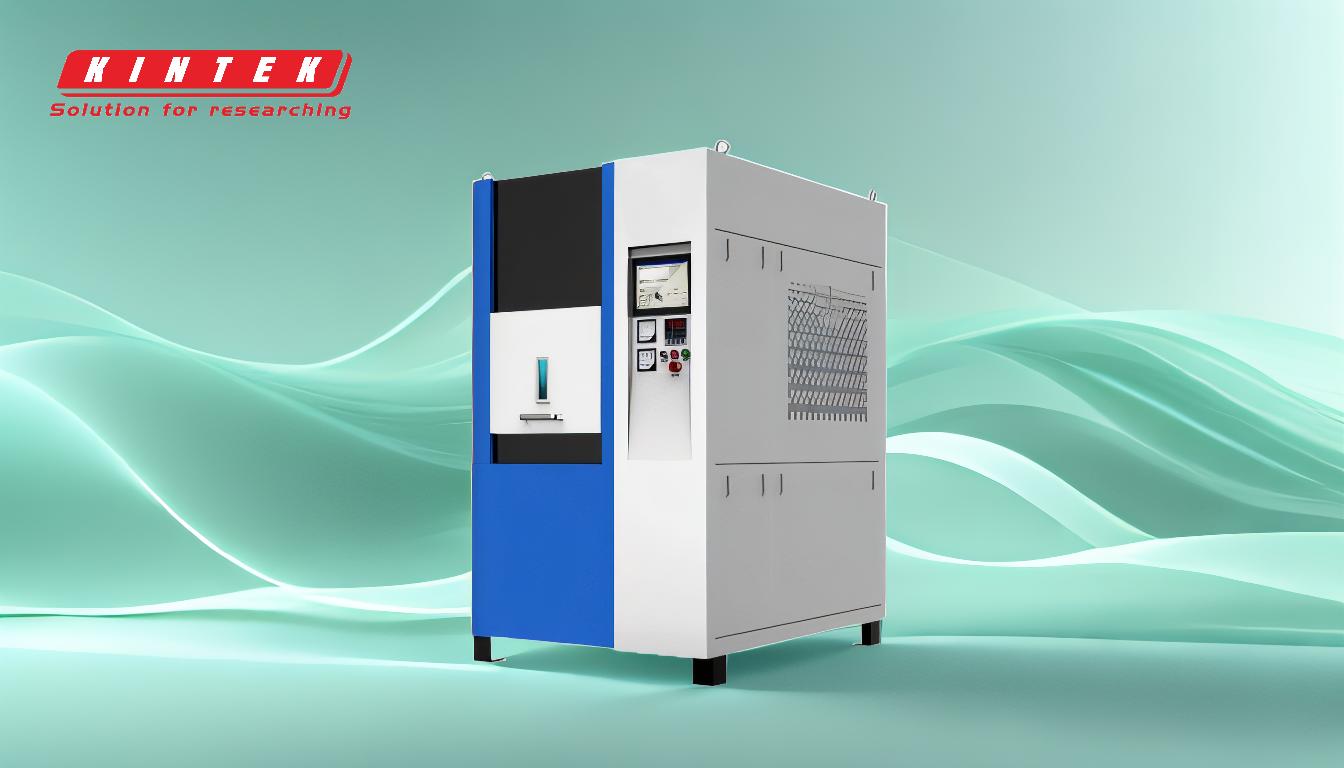
-
Definition and Alternative Names:
- SPS stands for Spark Plasma Sintering, an advanced powder metallurgy technique.
- It is also known as Pulsed Electric Current Sintering (PECS), Field Assisted Sintering Technique (FAST), or Plasma-Activated Sintering (PAS).
-
Core Mechanism:
- The process is based on a modified hot pressing setup.
- An electric current flows directly through the pressing die (usually graphite) and the component, enabling rapid heating and short processing times.
-
Key Features:
- High Heating Rates: Achieves very fast heating times due to pulsed currents.
- Short Processing Times: The entire sintering cycle is completed quickly.
- Low Sintering Temperatures: Allows for sintering at lower temperatures compared to traditional methods.
- Precise Control: Temperature, pressure, and heating rate can be precisely controlled.
-
Stages of the SPS Process:
- Vacuum Creation: The process begins by removing gas and creating a vacuum to prevent oxidation.
- Pressure Application: Pressure is applied to the powder material to facilitate densification.
- Resistive Heating: An electric current is passed through the material, causing localized high temperatures and spark discharges.
- Cooling: The material is cooled down after sintering to stabilize its microstructure.
-
Spark Plasma Effect:
- The spark discharge generated during the process causes localized high temperatures, leading to evaporation and melting on the surface of powder particles.
- This effect forms a neck around the contact area between particles, inhibiting particle growth and enabling the creation of materials with unique compositions and properties.
-
Operating Environment:
- The process operates in a vacuum or controlled atmosphere to ensure material purity and prevent oxidation.
-
Control and Programming:
- The SPS process is controlled and programmed using a touch screen, which facilitates precise control over the sintering cycle.
-
Applications and Benefits:
- Enables the fabrication of materials with unique microstructures and properties.
- Suitable for synthesizing both traditional and new materials in a single step.
- Reduces processing time and energy consumption compared to conventional sintering methods.
By understanding these key points, one can appreciate the efficiency and versatility of the SPS process in material synthesis and its potential for creating advanced materials with tailored properties.
Summary Table:
Key Aspect | Details |
---|---|
Alternative Names | Pulsed Electric Current Sintering (PECS), Field Assisted Sintering Technique (FAST), Plasma-Activated Sintering (PAS) |
Core Mechanism | Modified hot pressing setup with electric current flowing through graphite die and component |
Key Features | High heating rates, short processing times, low sintering temperatures, precise control |
Stages | 1. Vacuum creation 2. Pressure application 3. Resistive heating 4. Cooling |
Spark Plasma Effect | Inhibits particle growth, enables unique material compositions and properties |
Operating Environment | Vacuum or controlled atmosphere to prevent oxidation |
Applications | Fabrication of materials with unique microstructures and properties |
Ready to explore how Spark Plasma Sintering can revolutionize your material synthesis? Contact us today for expert guidance!