Brazing stainless steel requires careful preparation, the right choice of filler metals, and appropriate heating methods to ensure a strong and durable joint. The process involves cleaning the stainless steel to remove contaminants, selecting a suitable filler metal based on the application, and choosing a brazing method that aligns with the desired outcome. Common methods include flame, induction, or furnace heating, with options like vacuum brazing or brazing under a reducing atmosphere. Proper inspection of the brazed joint is also crucial to ensure quality and performance.
Key Points Explained:
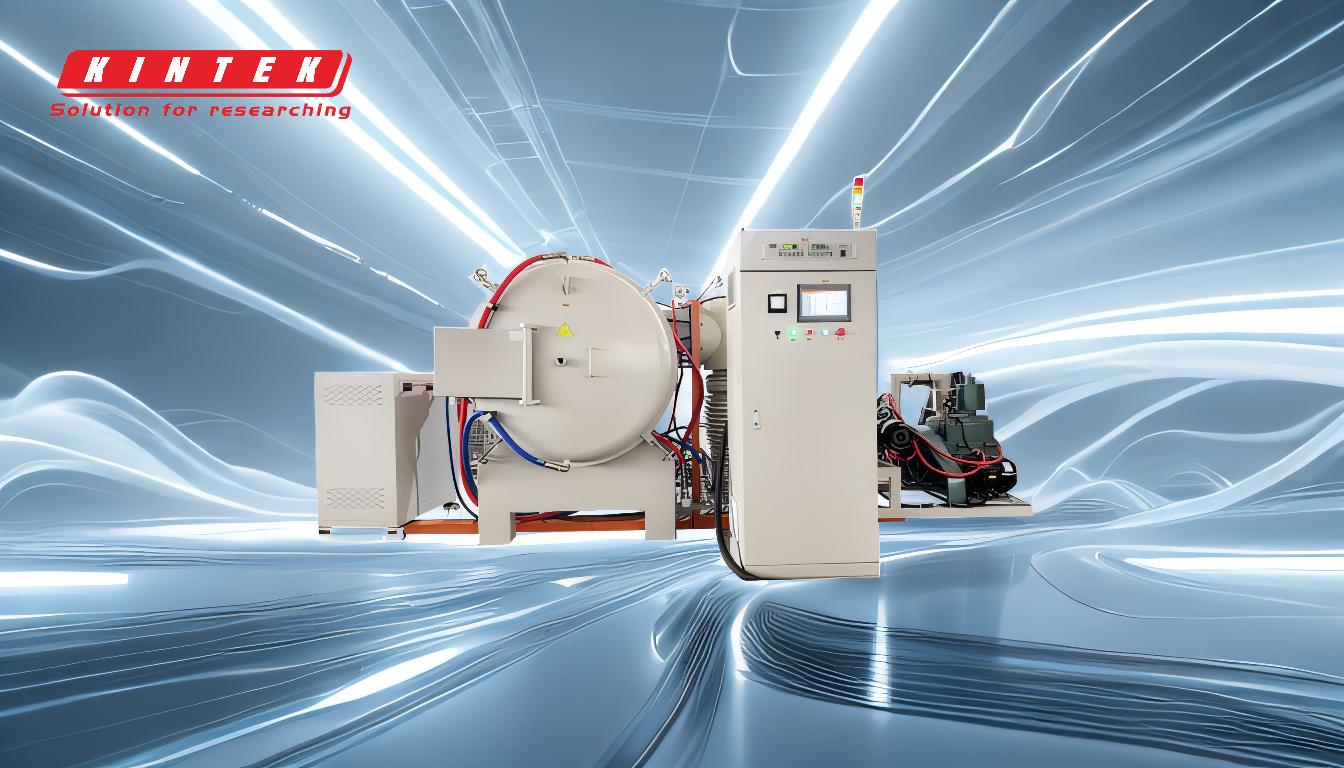
-
Cleaning and Preparation:
- Before brazing, stainless steel must be thoroughly cleaned to remove grease, oil, and other contaminants. This step is critical because any residue can interfere with the brazing process and weaken the joint. Cleaning is typically done using solvents or chemical solutions, and the brazing process should begin immediately after cleaning to prevent recontamination.
-
Filler Metals:
- The choice of filler metal depends on the specific requirements of the application. Commonly used filler metals for stainless steel include:
- Tin-lead solder: Suitable for low-temperature applications.
- Silver-based filler metals: Offer good strength and corrosion resistance.
- Copper-based filler metals: Provide high thermal conductivity.
- Manganese-based filler metals: Ideal for high-temperature applications.
- Nickel-based filler metals: Excellent for high-strength and corrosion-resistant joints.
- Precious metal filler metals: Used in specialized applications requiring high reliability.
- The choice of filler metal depends on the specific requirements of the application. Commonly used filler metals for stainless steel include:
-
Atmosphere and Environment:
- The brazing environment plays a significant role in the quality of the joint. Common methods include:
- Brazing in air with flux: Flux is used to prevent oxidation and improve wetting.
- Brazing under a reducing atmosphere: Dry hydrogen or wet hydrogen can be used to remove oxides and improve joint quality.
- Vacuum brazing: This method eliminates the need for flux and is ideal for high-purity applications.
- The brazing environment plays a significant role in the quality of the joint. Common methods include:
-
Heating Methods:
- Brazing stainless steel can be performed using various heating methods, including:
- Flame brazing: Suitable for small-scale or manual operations.
- Induction brazing: Provides precise and localized heating.
- Furnace brazing: Ideal for large-scale or batch processing, often used in conjunction with vacuum or controlled atmospheres.
- Brazing stainless steel can be performed using various heating methods, including:
-
Post-Brazing Inspection:
- After brazing, the joint must be inspected to ensure it meets the required standards. This includes checking for proper filler metal flow, joint integrity, and absence of defects such as cracks or voids. Non-destructive testing methods like X-ray or ultrasonic inspection may be used for critical applications.
By following these steps and considerations, you can achieve a high-quality brazed joint in stainless steel that meets the demands of your specific application.
Summary Table:
Step | Details |
---|---|
Cleaning | Remove grease, oil, and contaminants using solvents or chemical solutions. |
Filler Metals | Choose based on application (e.g., silver-based for strength, nickel for corrosion resistance). |
Atmosphere | Options include air with flux, reducing atmosphere, or vacuum brazing. |
Heating Methods | Flame, induction, or furnace brazing for precise or large-scale operations. |
Inspection | Check for proper filler flow, joint integrity, and defects using X-ray or ultrasonic methods. |
Need expert guidance for brazing stainless steel? Contact us today to ensure flawless results!