Chemical vapor deposition (CVD) is a manufacturing process used to produce high-quality solid materials by depositing thin films onto a substrate in a vacuum environment. This method is widely employed in industries such as semiconductors, optics, and coatings due to its ability to create materials with precise properties. The process involves the use of chemical reactions in a controlled environment to deposit layers of material onto a substrate. Additionally, the concept of vacuum plays a crucial role in processes like short path vacuum distillation, where it reduces the boiling point of materials, enabling efficient separation and purification of heat-sensitive compounds.
Key Points Explained:
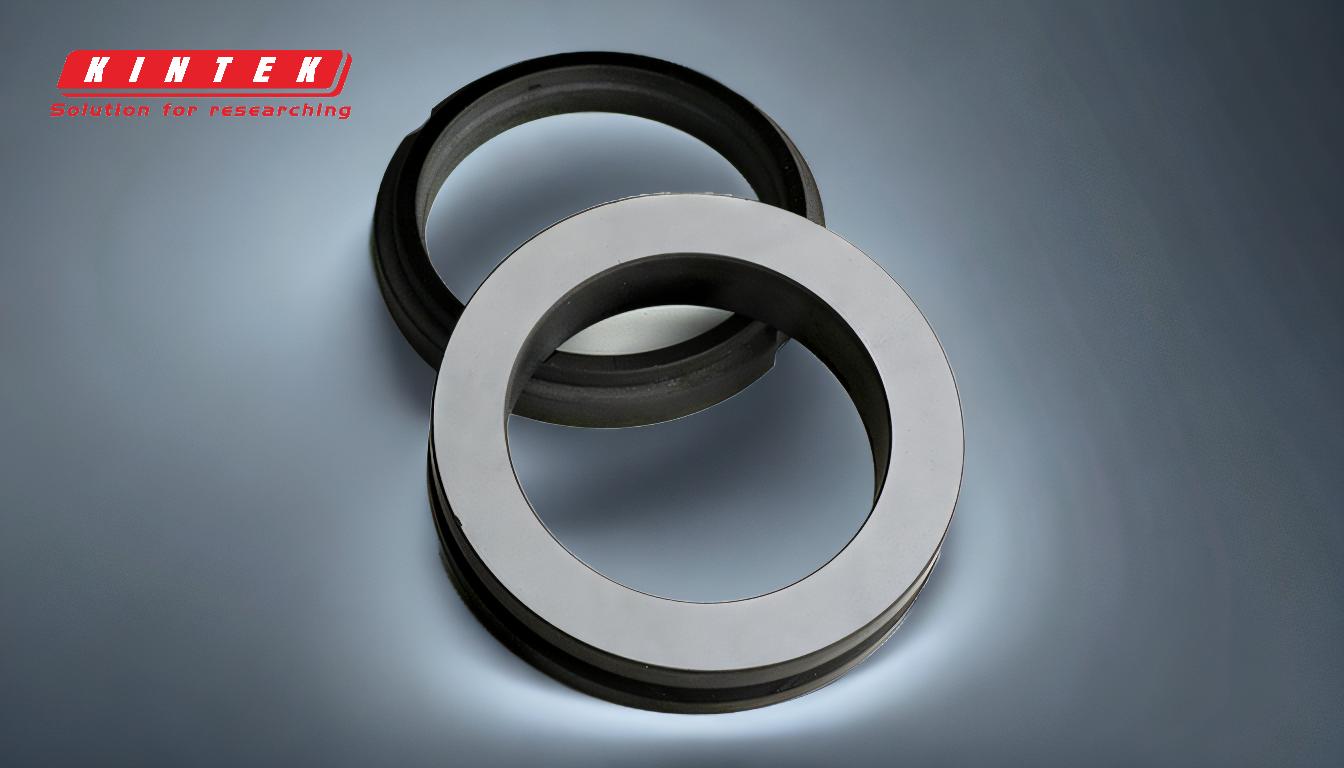
-
Definition of CVD (Chemical Vapor Deposition):
- CVD is a vacuum deposition technique used to create high-performance solid materials. It involves the chemical reaction of gaseous precursors to form a thin film on a substrate. This method is essential in industries requiring precise material properties, such as semiconductors and coatings.
-
Role of Vacuum in CVD:
- The vacuum environment in CVD ensures that the deposition process occurs in a controlled atmosphere, free from contaminants. This is critical for achieving high-quality, uniform films with desired properties.
-
Short Path Vacuum Distillation:
- Short path vacuum distillation is a technique used to purify and separate compounds, especially those that are heat-sensitive. The vacuum reduces the atmospheric pressure inside the system, lowering the boiling point of the material. This allows for efficient distillation of heavier molecules and prevents thermal degradation. Learn more about short path vacuum distillation.
-
How Vacuum Enhances Distillation:
- By lowering the operating pressure, vacuum conditions enable the distillation process to occur at lower temperatures. This is particularly beneficial for heat-sensitive materials, as it minimizes the risk of decomposition or damage during the process.
-
Mechanism of Vacuum in Distillation:
- In short path distillation, the vacuum unit connects the evaporation chamber and the condenser. It draws vapors from the evaporating flask into the condenser, facilitating the separation and condensation of gas-phase components back into liquids. This mechanism ensures efficient and rapid distillation.
-
Applications of CVD and Short Path Distillation:
- CVD is widely used in the production of semiconductors, optical coatings, and advanced materials. Short path vacuum distillation is commonly applied in the purification of essential oils, pharmaceuticals, and other heat-sensitive compounds.
By understanding the principles of CVD and the role of vacuum in processes like short path distillation, manufacturers can optimize their techniques to produce high-quality materials and compounds efficiently.
Summary Table:
Aspect | Details |
---|---|
Definition of CVD | A vacuum deposition technique for creating high-performance solid materials. |
Role of Vacuum in CVD | Ensures a controlled, contaminant-free environment for uniform film growth. |
Short Path Vacuum Distillation | Purifies heat-sensitive compounds by lowering boiling points under vacuum. |
Applications | Semiconductors, optical coatings, pharmaceuticals, and essential oils. |
Optimize your manufacturing processes with CVD and vacuum techniques—contact our experts today!