Debinding is a critical step in the manufacturing processes of powder metallurgy and ceramic injection molding. It involves the removal of binders—temporary materials used to hold particles together during the shaping process—from a green part. This process ensures that the final product, after sintering, achieves the desired structural integrity and material properties. Debinding can be performed through various methods, including thermal, solvent, catalytic, or wicking processes, each tailored to the specific binder system and material requirements.
Key Points Explained:
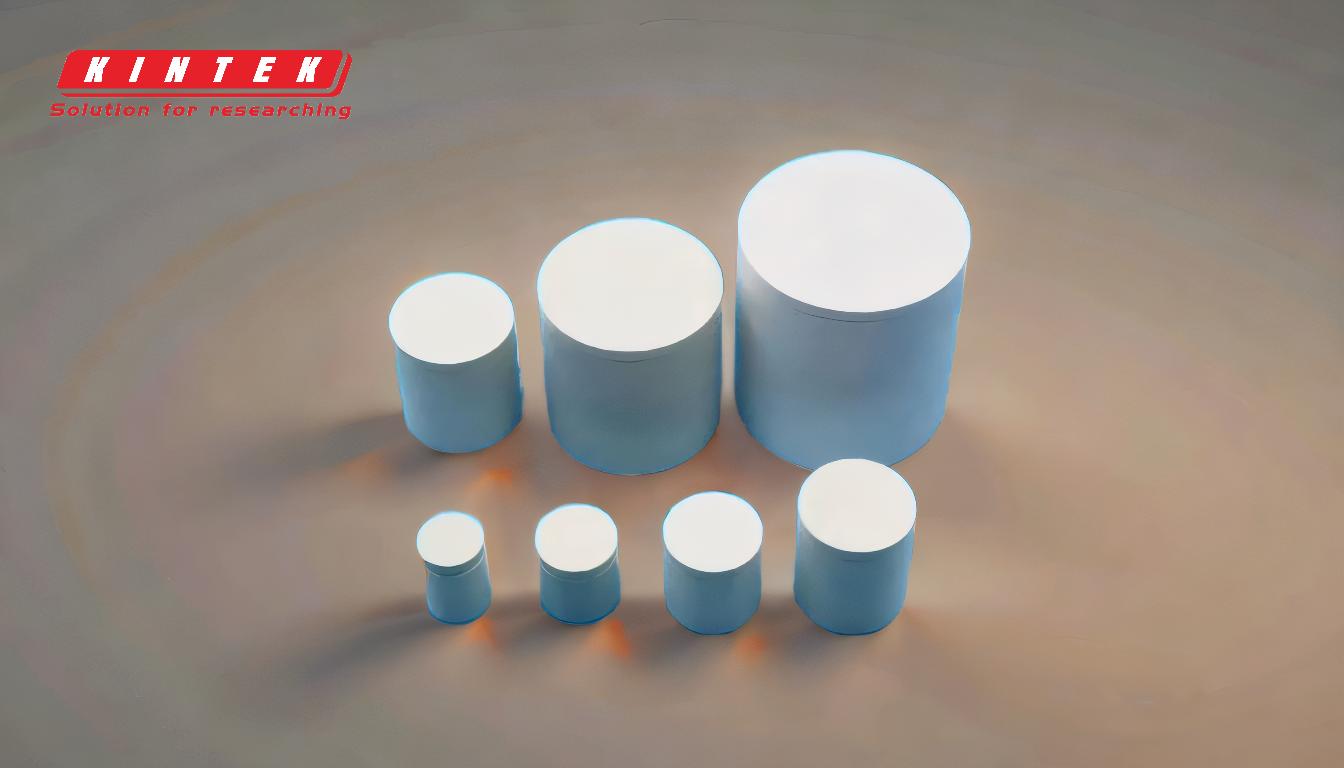
-
Definition of Debinding:
- Debinding refers to the removal of binders from a green part, which is a shaped but unsintered component. Binders are organic or polymeric materials added to powders to facilitate shaping and handling during the initial stages of manufacturing.
-
Purpose of Debinding:
- The primary goal is to eliminate the binder without damaging the part's structure. This ensures that the remaining powder particles can be sintered into a dense, strong final product. Incomplete or improper debinding can lead to defects such as cracking, bloating, or uneven shrinkage.
-
Types of Debinding Methods:
- Thermal Debinding: Involves heating the part to decompose the binder into gaseous byproducts. This method is widely used but requires careful control of temperature and heating rates to avoid part damage.
- Solvent Debinding: Uses a liquid solvent to dissolve the binder. This method is faster than thermal debinding but requires proper handling of solvents and disposal of waste.
- Catalytic Debinding: Utilizes a catalyst to break down the binder chemically. This method is highly efficient but is limited to specific binder systems.
- Wicking Debinding: Involves placing the part in a porous medium that absorbs the binder as it melts or evaporates. This method is slower but minimizes part distortion.
-
Factors Influencing Debinding:
- Binder Composition: The choice of binder affects the debinding method and parameters. For example, binders with low thermal stability are better suited for thermal debinding.
- Part Geometry: Complex geometries may require slower debinding rates to prevent stress buildup and cracking.
- Material Properties: The thermal and chemical stability of the powder material must be considered to avoid degradation during debinding.
-
Challenges in Debinding:
- Residual Binder: Incomplete removal can lead to defects during sintering. Proper process control is essential to ensure complete debinding.
- Part Distortion: Rapid or uneven binder removal can cause warping or cracking. Gradual and controlled debinding is necessary to maintain part integrity.
- Environmental Concerns: Solvent and thermal debinding methods can produce harmful byproducts, requiring proper ventilation and waste management.
-
Applications of Debinding:
- Debinding is commonly used in industries such as automotive, aerospace, medical devices, and electronics. It is essential for producing high-performance components like gears, bearings, and implants.
-
Future Trends in Debinding:
- Advances in binder systems, such as water-soluble or biodegradable binders, are reducing environmental impacts.
- Innovations in debinding equipment, such as microwave-assisted debinding, are improving efficiency and reducing processing times.
By understanding the principles and methods of debinding, manufacturers can optimize their processes to produce high-quality components with minimal defects and environmental impact.
Summary Table:
Aspect | Details |
---|---|
Definition | Removal of binders from a green part to prepare for sintering. |
Purpose | Eliminate binders without damaging the part for structural integrity. |
Methods | Thermal, Solvent, Catalytic, Wicking. |
Key Factors | Binder composition, part geometry, material properties. |
Challenges | Residual binder, part distortion, environmental concerns. |
Applications | Automotive, aerospace, medical devices, electronics. |
Future Trends | Eco-friendly binders, microwave-assisted debinding. |
Optimize your debinding process with expert guidance—contact us today!