Magnetron sputtering is a versatile and widely used physical vapor deposition (PVD) technique that deposits thin coatings (ranging from 0.1 µm to 5 µm) onto substrates for various functional applications. It involves generating plasma in a vacuum chamber using a magnetic field, which ionizes the target material, causing it to sputter or vaporize and deposit onto the substrate. This process is used across industries such as optics, electronics, medical devices, and textiles, enabling applications like anti-reflective coatings, semiconductor chips, wear-resistant coatings, and antimicrobial textiles. The technology offers precise control over film thickness, composition, and properties, making it a critical tool in modern manufacturing and research.
Key Points Explained:
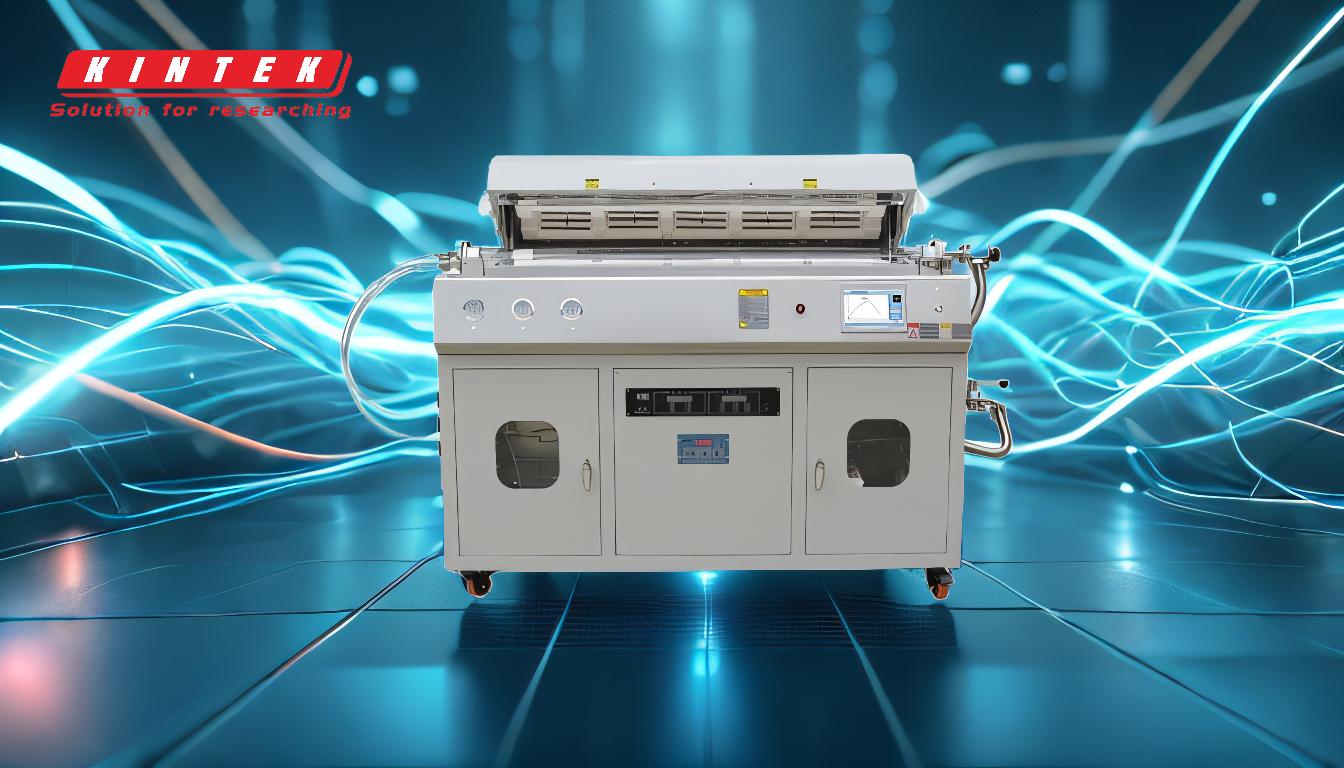
-
Basic Mechanism of Magnetron Sputtering:
- Magnetron sputtering operates by creating a plasma in a vacuum chamber using a magnetic field. This plasma ionizes the target material, causing it to sputter or vaporize and deposit onto a substrate.
- The magnetic field traps electrons near the target, increasing the efficiency of ionization and deposition. This allows for faster deposition rates and better control over the coating process.
- The process does not require the source material to melt or evaporate, making it compatible with a wide range of materials, including metals, alloys, and compounds.
-
Types of Magnetron Sputtering:
- DC Magnetron Sputtering: Uses a direct current power supply and is suitable for conducting materials. It is widely used due to its simplicity and high deposition rates.
- RF Magnetron Sputtering: Uses a high-frequency radio frequency power supply and is ideal for insulating materials. It allows for better control over film quality and is often used for more complex applications.
-
Applications in Various Industries:
- Optics: Used to create anti-reflective coatings, mirrors, and optical filters. The precise control over thickness and refractive index makes it ideal for applications in laser lenses, spectroscopy, and cable communications.
- Electronics: Enhances the durability of electronic components such as gate dielectrics, sensors, and printed circuit boards. It is also used in the production of thin-film solar cells and semiconductor chips.
- Medical Devices: Applied in the manufacture of angioplasty devices, anti-rejection coatings, radiation capsules, and dental implants. The process ensures biocompatibility and durability in medical applications.
- Textiles: Provides functional coatings such as antimicrobial, antistatic, and electroconductive properties, improving the performance of fabrics in various applications.
-
Advantages of Magnetron Sputtering:
- Material Compatibility: Works with nearly all materials, including metals, alloys, and compounds, without altering their composition.
- Precision and Control: Allows for precise control over film thickness, composition, and properties, ensuring high-quality coatings.
- Versatility: Suitable for a wide range of applications across industries, from optics and electronics to medical devices and textiles.
- Efficiency: The magnetic field enhances ionization and deposition rates, making the process faster and more efficient.
-
Technological Evolution:
- Magnetron sputtering has evolved significantly, with advancements in reactive DC sputtering, pulsed sputtering, and high ionization processes. These developments have improved deposition rates, film quality, and the ability to work with more complex materials.
-
Functional Benefits in Specific Applications:
- Anti-Reflective Coatings: Used in displays and optical components to reduce glare and improve light transmission.
- Wear-Resistant Coatings: Applied to machine parts to enhance durability and reduce friction.
- Barrier Layers: Used in OLEDs and solar cells to protect sensitive components from environmental factors.
- Solar Control Coatings: Applied to glass to improve energy efficiency in buildings.
Magnetron sputtering is a critical technology that enables the production of high-performance coatings and thin films across a wide range of industries. Its ability to precisely control film properties and work with diverse materials makes it indispensable in modern manufacturing and research.
Summary Table:
Aspect | Details |
---|---|
Mechanism | Uses plasma in a vacuum chamber with a magnetic field to sputter target material onto substrates. |
Types | DC Magnetron Sputtering (conductive materials), RF Magnetron Sputtering (insulating materials). |
Applications | Optics (anti-reflective coatings), Electronics (semiconductors), Medical Devices (biocompatible coatings), Textiles (antimicrobial properties). |
Advantages | Material compatibility, precise control, versatility, and high efficiency. |
Technological Evolution | Advancements in reactive DC sputtering, pulsed sputtering, and high ionization processes. |
Learn how magnetron sputtering can revolutionize your applications—contact our experts today!