PVD stands for Physical Vapor Deposition, a process used in engineering to deposit thin films of material onto a substrate. This technique involves converting a solid material into vapor in a vacuum environment and then condensing it onto a target surface. PVD is widely used to enhance surface properties such as hardness, wear resistance, and chemical stability, and it is commonly applied to metals, ceramics, and polymers. The process includes stages like evaporation, transportation, reaction, and deposition, and it is often used as an alternative to electroplating. PVD coatings are known for their durability, precision, and ability to tailor material properties for specific applications.
Key Points Explained:
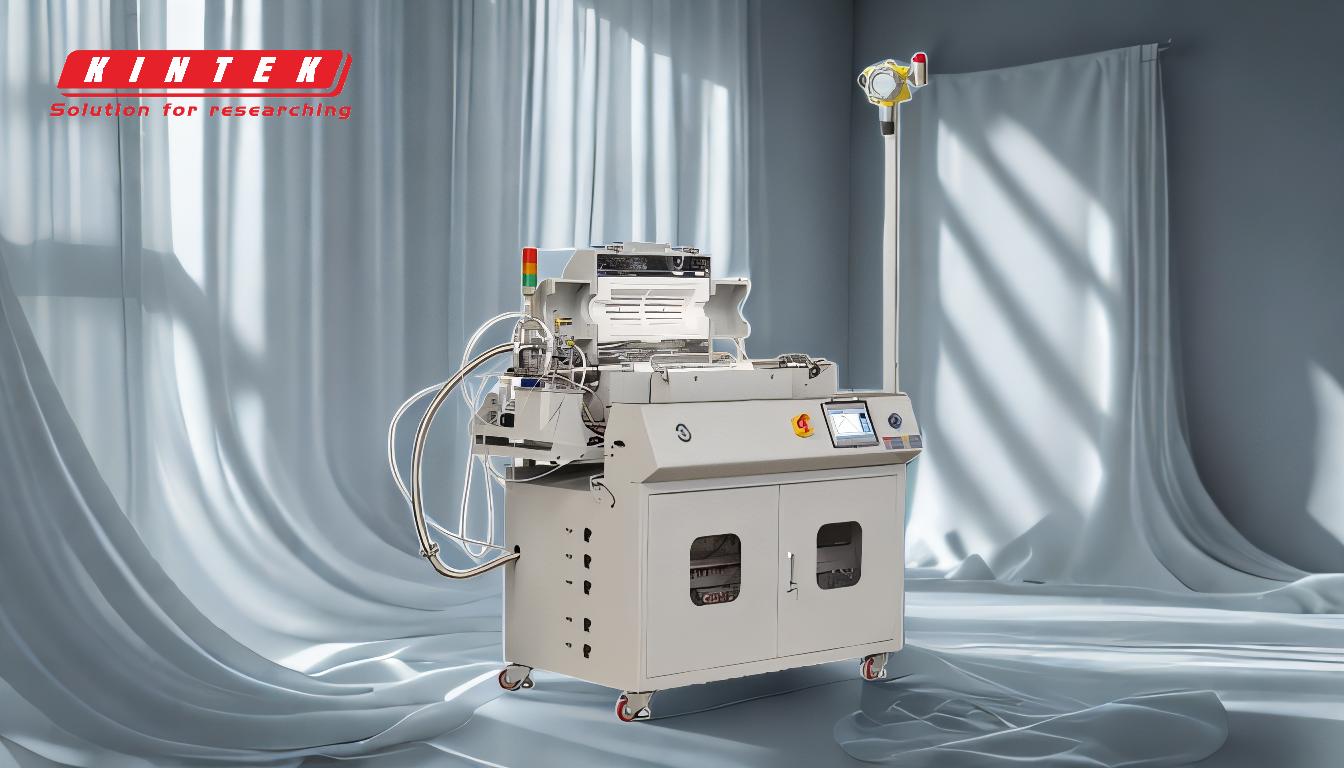
-
Definition of PVD:
- PVD stands for Physical Vapor Deposition, a thin film deposition process.
- It involves converting a solid material into vapor and then depositing it onto a substrate to form a thin, durable coating.
- This process is carried out in a vacuum chamber, ensuring precise control over the deposition environment.
-
Applications of PVD:
- PVD is used to coat metals, ceramics, and polymers, enhancing their surface properties.
- Common applications include improving hardness, wear resistance, and chemical stability of materials.
- It is also used in industries like jewelry manufacturing to create decorative finishes and in engineering for functional coatings.
-
Stages of the PVD Process:
- Evaporation: The solid material (target) is vaporized using techniques like cathodic arc or electron beam sources.
- Transportation: The vaporized material is transported through the vacuum environment to the substrate.
- Reaction: Reactive gases like nitrogen or oxygen may be introduced to form compound coatings with specific properties.
- Deposition: The vapor condenses onto the substrate, forming a thin, uniform coating.
-
Advantages of PVD Coatings:
- PVD coatings are extremely thin (0.5 – 5 μm) but highly durable.
- They significantly improve surface properties such as hardness, wear resistance, and chemical stability.
- The process allows for precise control over coating composition and properties, making it highly customizable for specific applications.
-
Comparison to Electroplating:
- PVD is considered a superior alternative to electroplating due to its ability to produce more durable and precise coatings.
- Unlike electroplating, which involves liquid solutions, PVD is a dry process, reducing environmental impact and waste.
-
Technical Details:
- PVD processes typically occur at a working pressure between 10^-2 to 10^-4 mbar.
- Energetic positively charged ions bombard the substrate to promote high-density coatings.
- Reactive gases can be introduced during deposition to create compound coatings with tailored properties.
-
Industrial Relevance:
- PVD is widely used in industries requiring high-performance coatings, such as aerospace, automotive, and medical devices.
- The ability to tailor coatings for specific applications makes PVD a versatile and valuable technology in modern engineering.
By understanding these key points, one can appreciate the significance of PVD in engineering and its role in advancing material science and surface engineering technologies.
Summary Table:
Aspect | Details |
---|---|
Definition | PVD stands for Physical Vapor Deposition, a thin film deposition process. |
Applications | Enhances hardness, wear resistance, and chemical stability of materials. |
Process Stages | Evaporation, transportation, reaction, and deposition. |
Advantages | Durable, precise, and customizable coatings for specific applications. |
Comparison | Superior to electroplating with reduced environmental impact. |
Technical Details | Works at 10^-2 to 10^-4 mbar with reactive gases for tailored properties. |
Industrial Relevance | Widely used in aerospace, automotive, and medical device industries. |
Unlock the potential of PVD coatings for your projects—contact our experts today!