Sintering in powder metallurgy is a critical heat treatment process that transforms compacted metal powders into dense, strong, and functional components. By heating the "green" compacted part at temperatures just below the melting point of the metal, sintering bonds the powder particles, reduces porosity, and enhances mechanical properties such as strength and structural integrity. This process also allows for controlled shrinkage and fine-tuning of material properties through adjustments in temperature and cooling rates. Sintering is highly versatile and cost-effective, enabling the production of complex parts like gears, bearings, and electrical contacts across various industries.
Key Points Explained:
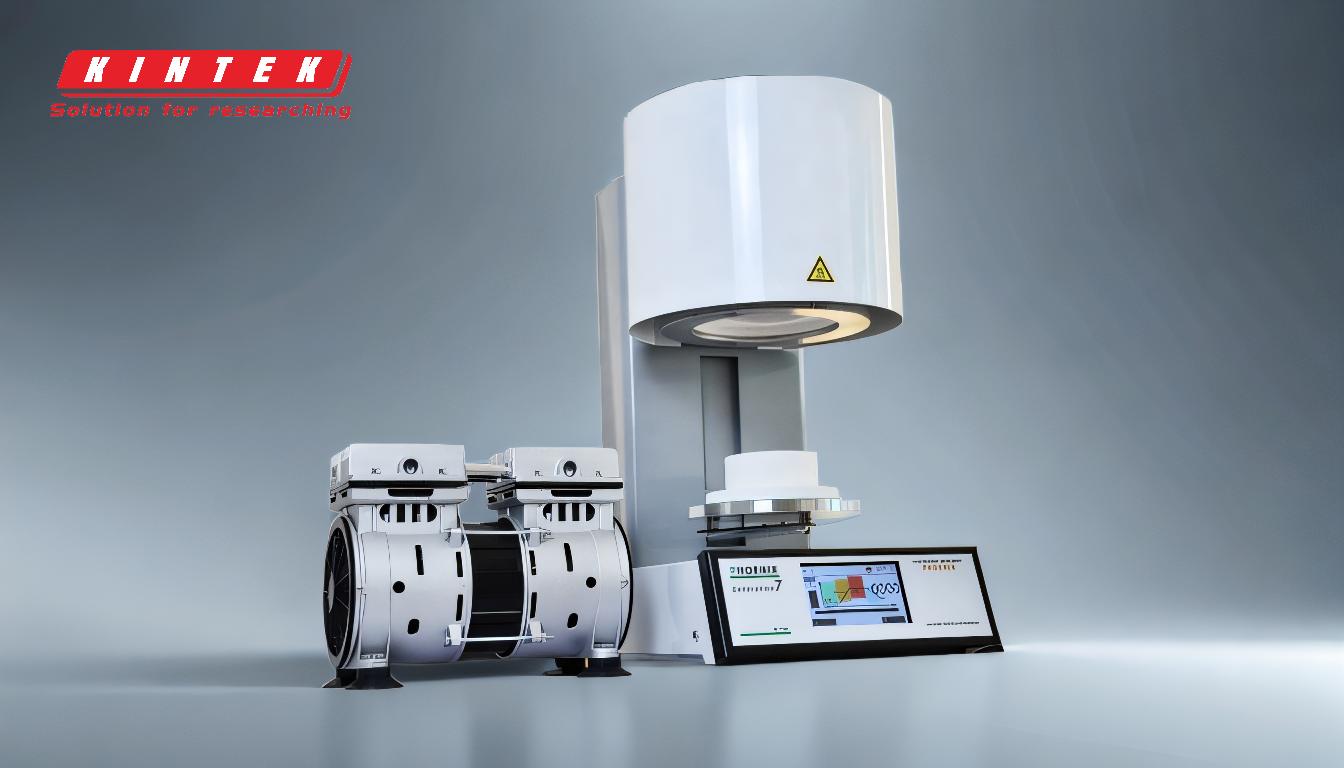
-
Definition and Purpose of Sintering:
- Sintering is a heat treatment process used in powder metallurgy to transform compacted metal powders (green parts) into dense, strong, and functional components.
- The primary purpose is to bond powder particles, reduce porosity, and enhance the mechanical and physical properties of the material, such as strength, density, and structural integrity.
-
The Sintering Process:
- The green compact is placed in a sintering furnace and heated to temperatures just below the melting point of the metal.
- The controlled atmosphere in the furnace prevents oxidation and ensures proper bonding of particles.
- During sintering, the particles bond together through diffusion, leading to reduced porosity and increased density.
- The process also involves controlled shrinkage, which is accounted for during the initial compaction stage.
-
Key Outcomes of Sintering:
- Increased Strength and Density: Sintering bonds the powder particles, eliminating porous spaces and enhancing the part's mechanical strength.
- Reduced Porosity: The process reduces the number of voids in the material, improving its structural integrity.
- Controlled Shrinkage: Sintering causes minor shrinkage, which is predictable and accounted for during the design and compaction phases.
- Final Dimensions and Properties: The part achieves its final dimensions and desired mechanical properties, which can be fine-tuned by adjusting the cooling rate.
-
Advantages of Sintering:
- Cost-Effectiveness: Sintering is a cost-efficient method for producing complex parts with minimal material waste.
- Versatility: It is used across various industries to manufacture a wide range of components, including gears, bearings, electrical contacts, and more.
- Material Efficiency: The process allows for the use of metal powders, which can be precisely controlled to achieve specific material properties.
-
Applications of Sintering:
- Sintering is widely used in industries such as automotive, aerospace, electronics, and manufacturing to produce high-performance components.
- Common products include gears, couplings, pulleys, rotors, sprockets, cams, and armatures.
-
Controlled Atmosphere and Temperature:
- The sintering process requires a controlled atmosphere to prevent oxidation and ensure proper bonding of particles.
- The temperature is carefully maintained just below the melting point of the metal to avoid melting while enabling particle bonding.
-
Role in Powder Metallurgy:
- Sintering is the final and most critical step in powder metallurgy, as it transforms the compacted powder into a functional part with the desired properties.
- It ensures the part meets the required mechanical and physical specifications for its intended application.
By understanding the sintering process, manufacturers can produce high-quality, durable, and precise components efficiently and cost-effectively. This process is essential for the success of powder metallurgy in modern manufacturing.
Summary Table:
Aspect | Details |
---|---|
Purpose | Bonds powder particles, reduces porosity, and enhances mechanical strength. |
Process | Heating green compacts below melting point in a controlled atmosphere. |
Key Outcomes | Increased strength, reduced porosity, controlled shrinkage, final dimensions. |
Advantages | Cost-effective, versatile, material-efficient. |
Applications | Automotive, aerospace, electronics, manufacturing. |
Controlled Conditions | Controlled atmosphere and precise temperature. |
Role in Powder Metallurgy | Final step to achieve functional parts with desired properties. |
Discover how sintering can enhance your manufacturing process—contact us today for expert guidance!