Brazing is a metal-joining process that requires specific equipment to ensure a strong and clean bond. The primary goal is to create an environment free from oxidants, oxygen, and moisture, which can compromise the quality of the brazed joint. Below is a detailed explanation of the equipment and conditions necessary for successful brazing.
Key Points Explained:
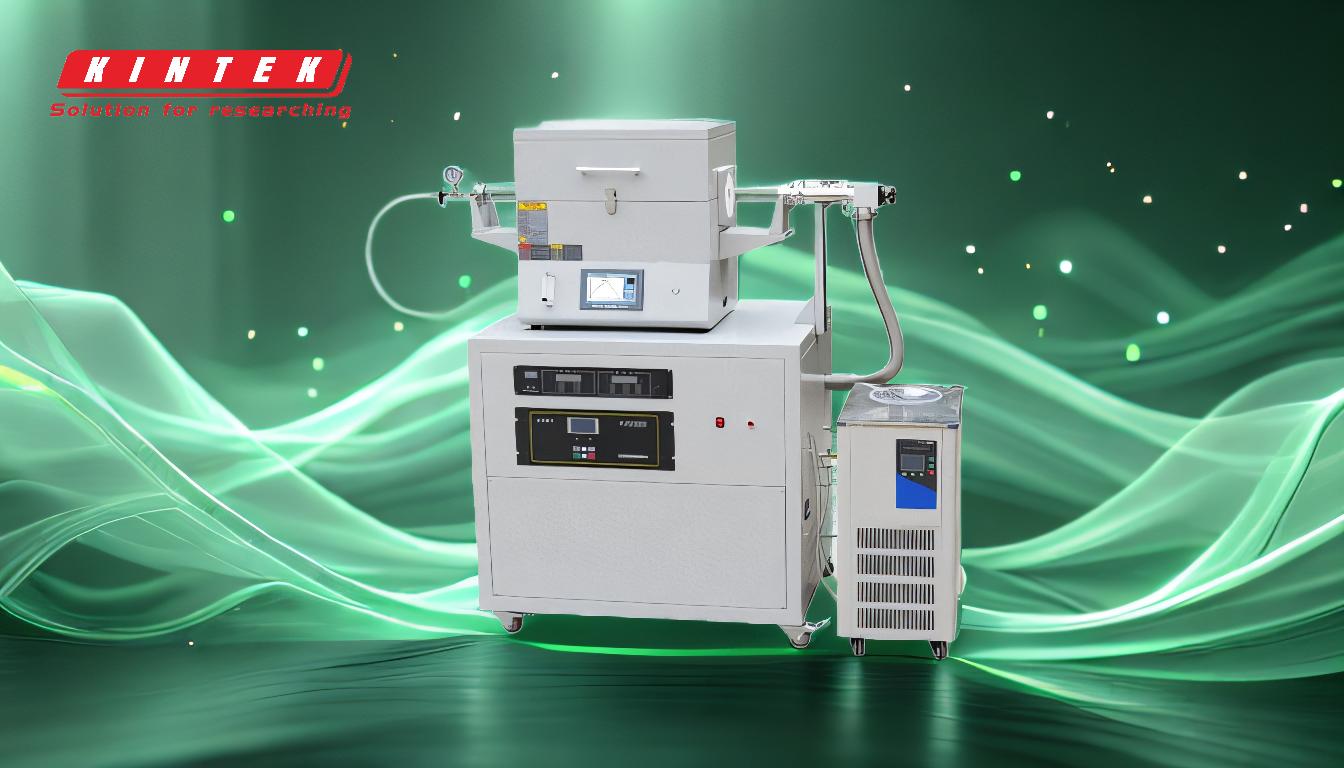
-
Atmosphere Control:
- Neutral Gas Environment: Brazing requires a neutral gas atmosphere, typically pure nitrogen, to prevent oxidation. This ensures that the metal surfaces remain clean and free from contaminants during the heating process.
- Oxygen Content: The oxygen content in the brazing atmosphere must be kept below 100 ppm (parts per million). High oxygen levels can lead to oxidation, which weakens the bond and affects the integrity of the joint.
- Humidity Control: The humidity level must be maintained below -40°C dew point. Moisture in the atmosphere can introduce hydrogen, which can cause embrittlement and other defects in the brazed joint.
-
Heating Equipment:
- Furnaces: For controlled brazing processes, especially in industrial settings, furnaces are used. These furnaces can be either batch or continuous types, depending on the production requirements. They provide uniform heating and precise temperature control, which is crucial for achieving consistent brazing results.
- Torches: For smaller or more localized brazing tasks, a brazing torch is often used. These torches can be powered by various fuels, including propane, acetylene, or natural gas. The choice of torch depends on the specific application and the materials being joined.
-
Temperature Control:
- Thermocouples and Pyrometers: Accurate temperature measurement is critical in brazing. Thermocouples and pyrometers are used to monitor and control the temperature within the brazing environment. This ensures that the materials reach the optimal brazing temperature without overheating, which could damage the components.
-
Flux Application:
- Flux: Flux is used to clean the metal surfaces and prevent oxidation during the brazing process. It is applied before heating and helps the filler metal flow smoothly into the joint. The type of flux used depends on the materials being brazed and the specific brazing method.
-
Filler Materials:
- Brazing Alloys: The filler material, or brazing alloy, is chosen based on the base metals being joined. Common brazing alloys include silver, copper, and aluminum-based alloys. The filler material must have a lower melting point than the base metals to ensure it flows properly without melting the components.
-
Cooling Systems:
- Controlled Cooling: After brazing, controlled cooling is necessary to prevent thermal stress and cracking. This can be achieved through natural cooling in a controlled atmosphere or by using cooling chambers that gradually reduce the temperature.
-
Safety Equipment:
- Protective Gear: Operators must wear appropriate protective gear, including heat-resistant gloves, safety glasses, and protective clothing, to protect against burns and other hazards associated with high-temperature processes.
- Ventilation: Proper ventilation is essential to remove any harmful fumes generated during the brazing process, especially when using fluxes that may release toxic gases.
By ensuring that all these elements are in place, you can achieve a high-quality brazed joint that is strong, durable, and free from defects.
Summary Table:
Category | Equipment/Requirements |
---|---|
Atmosphere Control | Neutral gas (e.g., nitrogen), oxygen content <100 ppm, humidity < -40°C dew point |
Heating Equipment | Furnaces (batch/continuous), brazing torches (propane, acetylene, natural gas) |
Temperature Control | Thermocouples, pyrometers for precise temperature monitoring |
Flux Application | Flux to clean surfaces and prevent oxidation |
Filler Materials | Brazing alloys (e.g., silver, copper, aluminum-based) with lower melting points |
Cooling Systems | Controlled cooling (natural or chamber-based) to prevent thermal stress |
Safety Equipment | Heat-resistant gloves, safety glasses, protective clothing, proper ventilation |
Achieve flawless brazing results with the right equipment—contact our experts today for guidance!