Pyrolysis is a thermal decomposition process that breaks down organic materials at high temperatures in the absence of oxygen. The equipment used in pyrolysis is designed to handle this process efficiently, ensuring safety, energy efficiency, and environmental compliance. Key equipment includes the feeding system, pyrolysis reactor, discharging system, syn-gas recycling system, and de-dusting system. The pyrolysis reactor is the core component where the thermal decomposition occurs, and it comes in various designs such as batch, fixed-bed, and fluidized-bed reactors. Supporting systems ensure raw material delivery, heat supply, gas recycling, and emission control, making the process sustainable and compliant with environmental standards.
Key Points Explained:
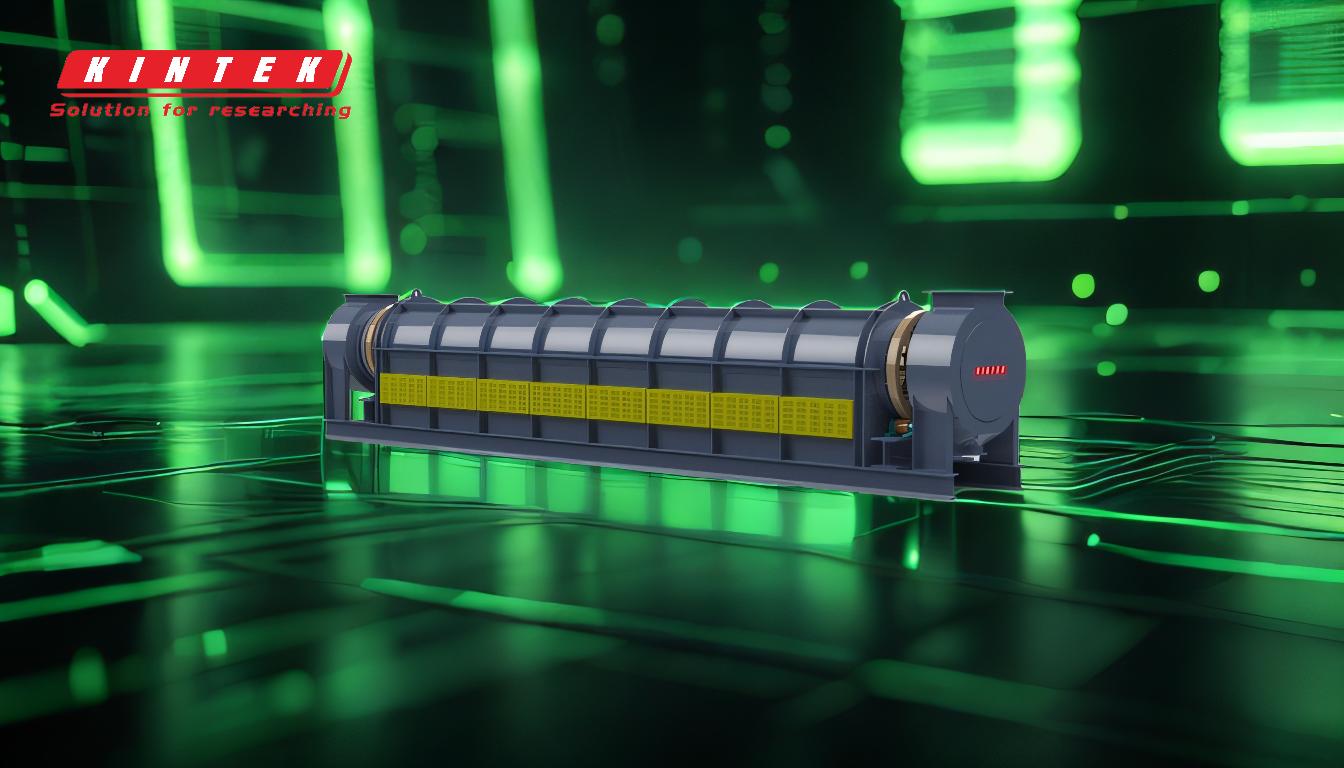
-
Feeding System
- The feeding system is responsible for delivering raw materials into the pyrolysis reactor in a fully sealed and automated manner.
- It ensures a continuous supply of feedstock, which is critical for maintaining the efficiency of the pyrolysis process.
- The system is designed to handle various types of materials, including biomass, plastics, and rubber, depending on the application.
-
- The pyrolysis reactor is the heart of the pyrolysis system, where high-temperature thermal decomposition occurs.
- It is designed to operate in low-oxygen conditions to prevent combustion and ensure the breakdown of materials into biochar, bio-oil, and syn gases.
- Types of reactors include:
- Batch Reactors: Simple, sealed vessels ideal for small-scale operations requiring energy stability.
- Fixed-Bed Reactors: Heat is applied from the walls, and the substrate is stacked on the bed for thermal decomposition.
- Fluidized-Bed Reactors: Use a fluid medium to enhance heat transfer and are more efficient for large-scale operations.
-
Discharging System
- This system transports the solid residue, such as carbon black or biochar, out of the reactor.
- It often includes water-cooling pipes to cool the residue before storage or further processing.
- The design ensures safe handling of high-temperature materials and minimizes heat loss.
-
Syn-Gas Recycling System
- The syn-gas recycling system captures and recycles combustible gases produced during pyrolysis.
- These gases can be used to heat the reactor, making the process self-sustaining and reducing external energy requirements.
- This system enhances the overall energy efficiency of the pyrolysis process.
-
De-Dusting System
- The de-dusting system purifies the emission gases to meet environmental standards, such as EU emission regulations.
- It removes particulate matter and harmful compounds from the exhaust gases, ensuring compliance with environmental laws.
- This system is critical for minimizing the environmental impact of pyrolysis operations.
-
Supporting Components
- Driving Device: Powers the reactor and other mechanical components.
- Base and Casing: Provide structural support and insulation to maintain high temperatures within the reactor.
- Main Furnace: Houses the reactor and ensures efficient heat distribution.
-
Applications and Outputs
- Pyrolysis produces three main outputs:
- Biochar: A carbon-rich solid used as a soil amendment or fuel.
- Bio-Oil: A liquid emulsion containing oxygenated organic compounds, suitable for fuel or chemical production.
- Syn Gases: Combustible gases used for energy recovery.
- The equipment is versatile and can be adapted for various feedstocks, including biomass, plastics, and tires.
- Pyrolysis produces three main outputs:
In summary, the equipment used in pyrolysis is designed to handle the thermal decomposition of organic materials efficiently and sustainably. The pyrolysis reactor is the central component, supported by feeding, discharging, gas recycling, and de-dusting systems. Each piece of equipment plays a critical role in ensuring the process is energy-efficient, environmentally compliant, and capable of producing valuable outputs like biochar, bio-oil, and syn gases.
Summary Table:
Component | Function | Key Features |
---|---|---|
Feeding System | Delivers raw materials into the reactor in a sealed, automated manner. | Handles biomass, plastics, rubber; ensures continuous feedstock supply. |
Pyrolysis Reactor | Core component for thermal decomposition in low-oxygen conditions. | Types: batch, fixed-bed, fluidized-bed; produces biochar, bio-oil, syn gases. |
Discharging System | Transports solid residue (e.g., biochar) out of the reactor. | Includes water-cooling pipes for safe handling and heat retention. |
Syn-Gas Recycling | Captures and recycles combustible gases for reactor heating. | Enhances energy efficiency; reduces external energy needs. |
De-Dusting System | Purifies emission gases to meet environmental standards. | Removes particulate matter and harmful compounds; ensures compliance. |
Supporting Components | Includes driving devices, base, casing, and main furnace. | Provides structural support, insulation, and efficient heat distribution. |
Ready to optimize your pyrolysis process? Contact our experts today to learn more about the right equipment for your needs!