Rotary furnaces are versatile heating systems used in various industrial applications, including metal processing, chemical reactions, and waste treatment. The type of fuel a rotary furnace uses depends on its design, application, and operational requirements. Common fuels include natural gas, propane, diesel, and electricity. Each fuel type has its advantages, such as cost-efficiency, temperature control, or environmental considerations. The choice of fuel impacts the furnace's performance, energy efficiency, and operational costs. Understanding the fuel options and their implications is crucial for selecting the right rotary furnace for specific industrial needs.
Key Points Explained:
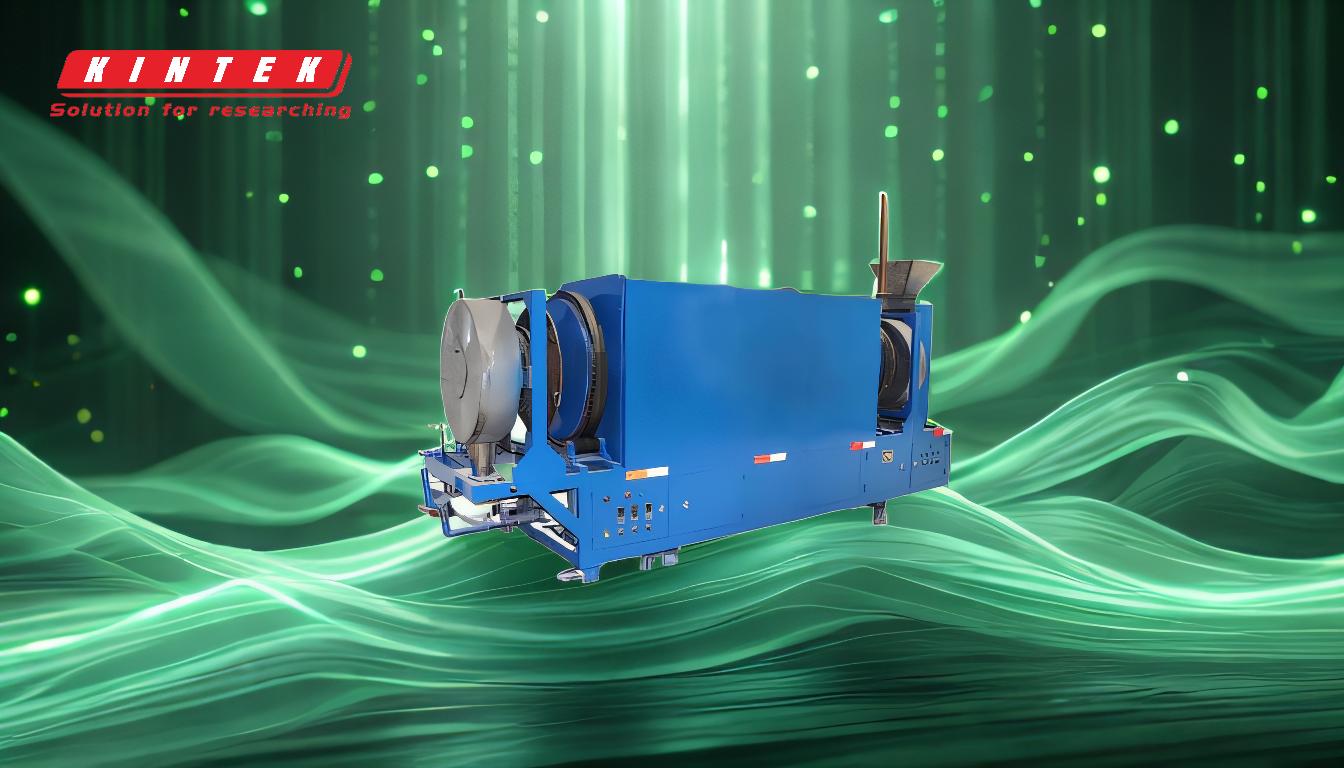
-
Types of Fuels Used in Rotary Furnaces:
- Natural Gas: A widely used fuel due to its availability, cost-effectiveness, and clean combustion. It provides consistent heat and is suitable for high-temperature applications.
- Propane: Often used in areas where natural gas is not accessible. It offers similar benefits to natural gas but may have higher operational costs.
- Diesel: Commonly used in mobile or portable rotary furnaces. It provides high energy output but may produce more emissions compared to gas fuels.
- Electricity: Electric rotary furnaces use heating elements to generate heat. They are ideal for applications requiring precise temperature control and are environmentally friendly, as they produce no direct emissions.
-
Factors Influencing Fuel Choice:
- Application Requirements: The type of material being processed and the required temperature range influence fuel selection. For example, high-temperature metal melting may require natural gas or propane.
- Operational Costs: The cost of fuel and its availability in the region play a significant role in decision-making.
- Environmental Considerations: Fuels like natural gas and electricity are preferred for their lower environmental impact compared to diesel.
- Furnace Design: Some rotary furnaces are specifically designed to operate with certain fuels, limiting flexibility in fuel choice.
-
Advantages of Electric Rotary Furnaces:
- Precision: Electric furnaces offer excellent temperature control, making them suitable for sensitive processes.
- Clean Operation: They produce no direct emissions, reducing environmental impact.
- Low Maintenance: Electric heating elements have fewer moving parts, resulting in lower maintenance requirements.
-
Advantages of Gas-Powered Rotary Furnaces:
- High Energy Output: Gas fuels provide high heat output, making them suitable for demanding industrial applications.
- Cost-Effectiveness: Natural gas is often cheaper than electricity, reducing operational costs.
- Versatility: Gas-powered furnaces can handle a wide range of materials and processes.
-
Considerations for Fuel Selection:
- Energy Efficiency: Evaluate the efficiency of the fuel in converting energy to heat.
- Infrastructure: Ensure that the necessary infrastructure (e.g., gas lines or electrical connections) is available.
- Regulatory Compliance: Consider local regulations regarding emissions and fuel usage.
By understanding these key points, purchasers can make informed decisions about the type of rotary furnace and fuel that best meet their operational and environmental needs. For more details on rotating furnace designs and applications, visit (rotating furnace)[/topic/rotating-furnace].
Summary Table:
Fuel Type | Advantages | Common Applications |
---|---|---|
Natural Gas | Cost-effective, clean combustion, consistent heat | High-temperature metal processing |
Propane | Accessible where natural gas isn’t, similar benefits to natural gas | Remote or portable applications |
Diesel | High energy output, suitable for mobile furnaces | Waste treatment, portable setups |
Electricity | Precise temperature control, environmentally friendly, low maintenance | Sensitive chemical processes |
Need help selecting the right fuel for your rotary furnace? Contact our experts today for personalized advice!