Heat treatment is a critical process in metallurgy and materials science, and the choice of furnace plays a significant role in determining the quality and efficiency of the treatment. The most commonly used furnace for heat treatment is the vacuum furnace, which offers numerous advantages such as high thermal efficiency, rapid temperature control, and the ability to prevent oxidation and decarburization. Other types of furnaces, such as lab furnaces, are also used for specific applications like annealing, hardening, and sintering. The operating process of these furnaces must be carefully managed to ensure optimal results, reduce failure rates, and extend the furnace's lifespan. Vertical vacuum furnaces, in particular, are highly regarded for their cleanliness, repeatability, and reliability in heat treatment processes.
Key Points Explained:
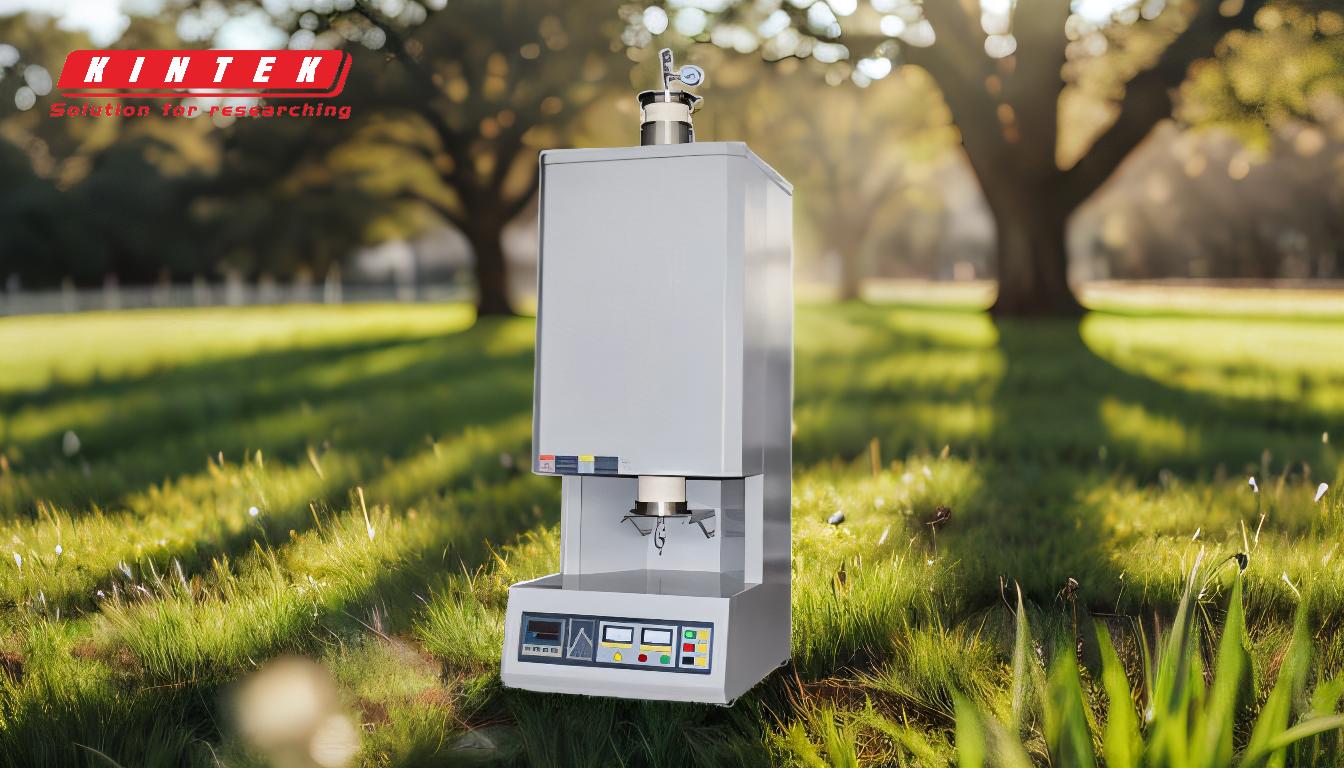
-
Vacuum Furnace for Heat Treatment:
- High Thermal Efficiency: Vacuum furnaces are designed to maximize thermal efficiency, ensuring that heat is evenly distributed and effectively utilized during the heat treatment process.
- Rapid Temperature Control: These furnaces can quickly achieve the desired temperature and cool down rapidly, which is essential for precise heat treatment cycles.
- Prevention of Oxidation and Decarburization: The vacuum environment prevents the material from oxidizing or losing carbon, which is crucial for maintaining the material's integrity and mechanical properties.
- Surface Purification: The vacuum process removes surface impurities such as phosphorus chips, grease, and gases, resulting in a bright, clean surface.
- Reduced Thermal Stress and Deformation: The controlled environment minimizes thermal stress and deformation, leading to higher product pass rates and reduced costs.
- Improved Mechanical Properties: The heat treatment in a vacuum furnace enhances the mechanical properties and service life of the treated materials.
- Environmental Safety: Vacuum furnaces operate in a clean, pollution-free environment, making them safe for operators and environmentally friendly.
-
Lab Furnaces for Specific Applications:
- Annealing: Lab furnaces are used to soften materials, making them more workable and reducing internal stresses.
- Hardening: These furnaces are essential for increasing the hardness and strength of materials through controlled heating and cooling processes.
- Sintering: Lab furnaces are used to bond powdered materials into a solid mass by heating them below their melting point.
- Tempering: This process involves reheating hardened materials to a specific temperature to reduce brittleness and improve toughness.
- Atmosphere Processing: Lab furnaces can be used to create specific atmospheric conditions, such as inert or reducing environments, to achieve desired material properties.
-
Operating Process of Vacuum Furnaces:
- Correct Operating Procedures: Mastering the correct operating process is crucial to ensure that the heat treatment effect meets expectations. This includes proper loading of materials, setting the correct temperature and time parameters, and following safety protocols.
- Reducing Failure Rates: Proper operation helps reduce the failure rate of the furnace and the materials being treated, leading to more consistent and reliable results.
- Extending Service Life: Following the correct operating procedures can extend the service life of the vacuum furnace, reducing maintenance costs and downtime.
-
Vertical Vacuum Furnaces:
- Cleanliness: Vertical vacuum furnaces are designed to maintain a clean environment, which is essential for high-quality heat treatment.
- Repeatability and Reliability: These furnaces offer excellent process parameters and temperature uniformity, ensuring consistent results across multiple batches.
- Bright Oxide-Free Treatment: Vertical vacuum furnaces are capable of producing bright, oxide-free surfaces on most metals and alloys, which is important for aesthetic and functional purposes.
- Safe Operation and Easy Maintenance: These furnaces are designed for safe operation and easy maintenance, making them user-friendly and reducing operational risks.
- Removal of Surface Volatiles: The vacuum environment effectively removes surface volatiles, ensuring that the treated materials are free from contaminants.
In conclusion, the choice of furnace for heat treatment depends on the specific requirements of the material and the desired outcome. Vacuum furnaces, particularly vertical ones, are highly effective for a wide range of heat treatment processes due to their efficiency, reliability, and ability to produce high-quality results. Lab furnaces also play a crucial role in specific applications, offering versatility and precision in controlled environments. Proper operation and maintenance of these furnaces are essential to achieving optimal results and extending their service life.
Summary Table:
Furnace Type | Key Features | Applications |
---|---|---|
Vacuum Furnace | High thermal efficiency, rapid temperature control, prevents oxidation/degradation | General heat treatment, surface purification, improved mechanical properties |
Lab Furnace | Versatile, precise temperature control, specific atmosphere processing | Annealing, hardening, sintering, tempering, atmosphere processing |
Vertical Vacuum Furnace | Cleanliness, repeatability, reliability, bright oxide-free treatment | High-quality heat treatment, safe operation, removal of surface volatiles |
Ready to enhance your heat treatment process? Contact our experts today for tailored solutions!