Non-ferrous metals, such as aluminum, brass, and bronze, are typically melted using specialized furnaces designed for their specific properties and melting requirements. The most commonly used furnaces include gas-fired or electric resistance crucible furnaces, reverberatory furnaces, and induction furnaces. These furnaces are chosen based on factors like metal quality, energy efficiency, flexibility, and operational scale. For instance, electric resistance heated 'globar' aluminum wet bath reverberatory furnaces are preferred for high-quality applications due to their efficiency and low melt losses, while tilting crucible furnaces are favored for their flexibility in handling frequent alloy changes. Larger operations often utilize gas-fired central melting furnaces or induction furnaces for their capacity and efficiency.
Key Points Explained:
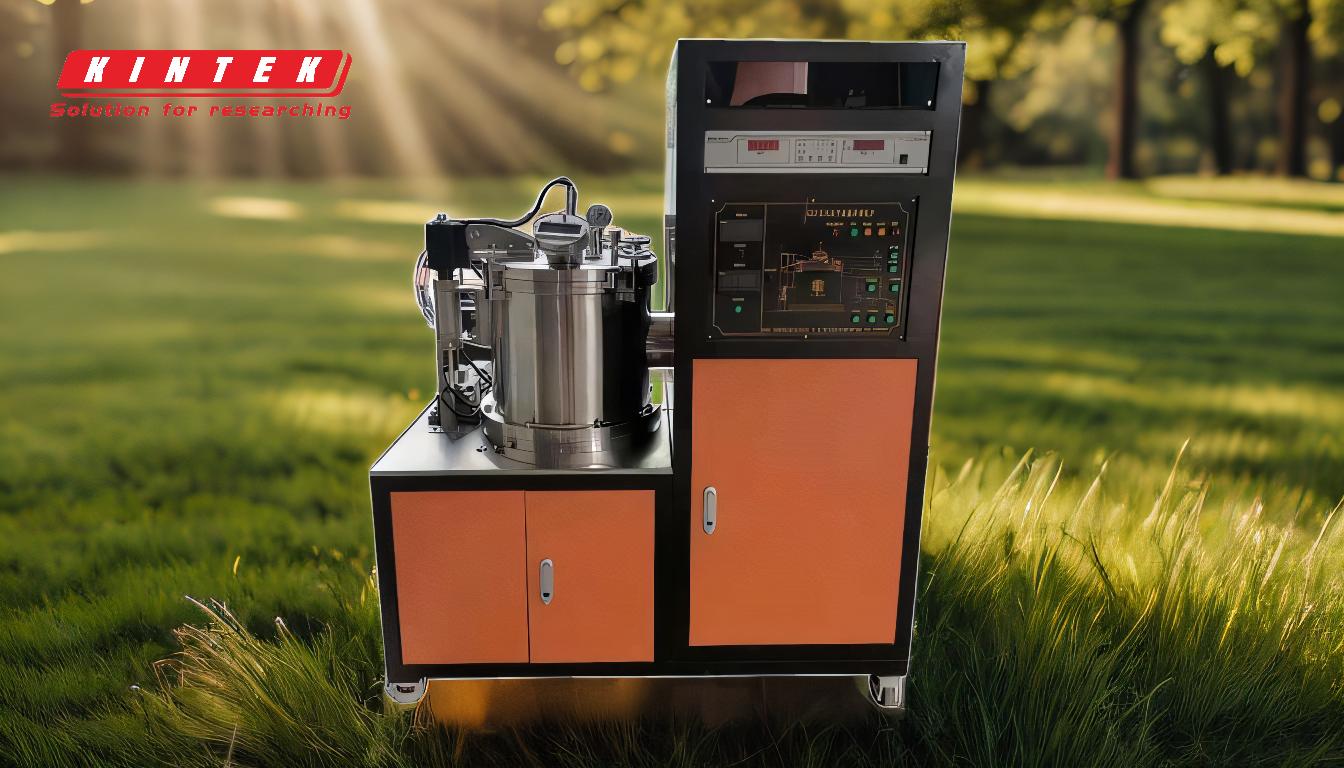
-
Crucible Furnaces:
- Types: Gas-fired, oil-fired, electric resistance, and electric induction.
- Applications: Commonly used for melting non-ferrous metals like aluminum, brass, and bronze.
- Advantages: Flexibility in handling frequent alloy changes, relatively small footprint, and suitability for smaller operations.
- Examples: Stationary bale-out crucible furnaces and hydraulic tilting crucible furnaces.
-
Reverberatory Furnaces:
- Types: Wet bath reverberatory furnaces and dry hearth reverberatory furnaces.
- Applications: Preferred for applications requiring high metal quality, such as electric motor rotor casting.
- Advantages: High energy efficiency (60-65%), superior metal quality, and low melt losses (less than 3%).
- Examples: Electric resistance heated 'globar' aluminum wet bath reverberatory furnaces.
-
Induction Furnaces:
- Principle: Use electromagnetic induction to heat and melt metals.
- Applications: Suitable for melting a wide range of non-ferrous metals, including aluminum and copper alloys.
- Advantages: High efficiency, precise temperature control, and minimal contamination.
- Examples: Electric induction furnaces used in larger capacity operations.
-
Central Melting Furnaces:
- Types: Gas-fired wet well reverberatory furnaces, dry hearth furnaces, and stack type furnaces.
- Applications: Used by larger, single alloy users for melting aluminum, which is then transferred to machine holding furnaces.
- Advantages: High capacity and efficiency, suitable for large-scale operations.
- Examples: Gas-fired central melting furnaces used in foundries.
-
High-Temperature Furnaces:
- Types: Tube furnaces, vacuum furnaces, box furnaces, and muffle furnaces.
- Applications: Used for high-temperature processes like fusion, sintering, melting, and testing.
- Advantages: Temperature uniformity and suitability for specialized applications.
- Examples: Furnaces equipped with strategically positioned heating elements for uniform heat distribution.
-
Electric Arc Furnaces:
- Principle: Use an electric arc to generate heat for melting.
- Applications: Primarily used for melting ferrous metals but can also be adapted for non-ferrous metals.
- Advantages: High melting capacity and ability to handle large volumes of metal.
- Examples: Electric arc furnaces used in steelmaking and metal smelting.
-
Gas-Fired Dry Hearth Furnaces:
- Applications: Used in permanent mould casting and larger capacity operations.
- Advantages: Efficient melting with minimal metal loss, suitable for continuous operations.
- Examples: Gas-fired dry hearth furnaces used in aluminum casting.
-
Stack Melters:
- Applications: Used in larger operations for melting aluminum and other non-ferrous metals.
- Advantages: High throughput and efficiency, suitable for large-scale production.
- Examples: Gas-fired stack melters used in foundries.
In summary, the choice of furnace for melting non-ferrous metals depends on the specific requirements of the application, including the type of metal, desired metal quality, operational scale, and energy efficiency. Crucible furnaces, reverberatory furnaces, and induction furnaces are among the most commonly used, each offering unique advantages tailored to different melting needs.
Summary Table:
Furnace Type | Applications | Advantages | Examples |
---|---|---|---|
Crucible Furnaces | Melting aluminum, brass, bronze | Flexible, small footprint, suitable for small operations | Stationary bale-out, hydraulic tilting crucible furnaces |
Reverberatory Furnaces | High-quality applications (e.g., rotor casting) | High energy efficiency (60-65%), superior metal quality, low melt losses (<3%) | Electric resistance heated 'globar' aluminum wet bath reverberatory furnaces |
Induction Furnaces | Wide range of non-ferrous metals | High efficiency, precise temperature control, minimal contamination | Electric induction furnaces for large capacity operations |
Central Melting Furnaces | Large-scale aluminum melting | High capacity, efficiency for large operations | Gas-fired wet well reverberatory, dry hearth furnaces |
High-Temperature Furnaces | Fusion, sintering, melting, testing | Temperature uniformity, specialized applications | Tube, vacuum, box, and muffle furnaces |
Need help choosing the right furnace for your non-ferrous metals? Contact our experts today!