Sintering is a critical process in manufacturing that involves heating compressed metal or ceramic powders to form complex structural parts. To ensure the quality and consistency of the sintered products, protective gases are used to create an inert atmosphere, preventing oxidation and decarburization. The most commonly used gases in sintering are hydrogen, nitrogen, and carbon monoxide. These gases help maintain atmospheric pressure, control the sintering environment, and ensure consistent performance. Nitrogen is particularly effective in preventing oxidation in high-heat zones, while hydrogen and carbon monoxide are used for their reducing properties. The choice of gas depends on the material being sintered and the desired outcomes.
Key Points Explained:
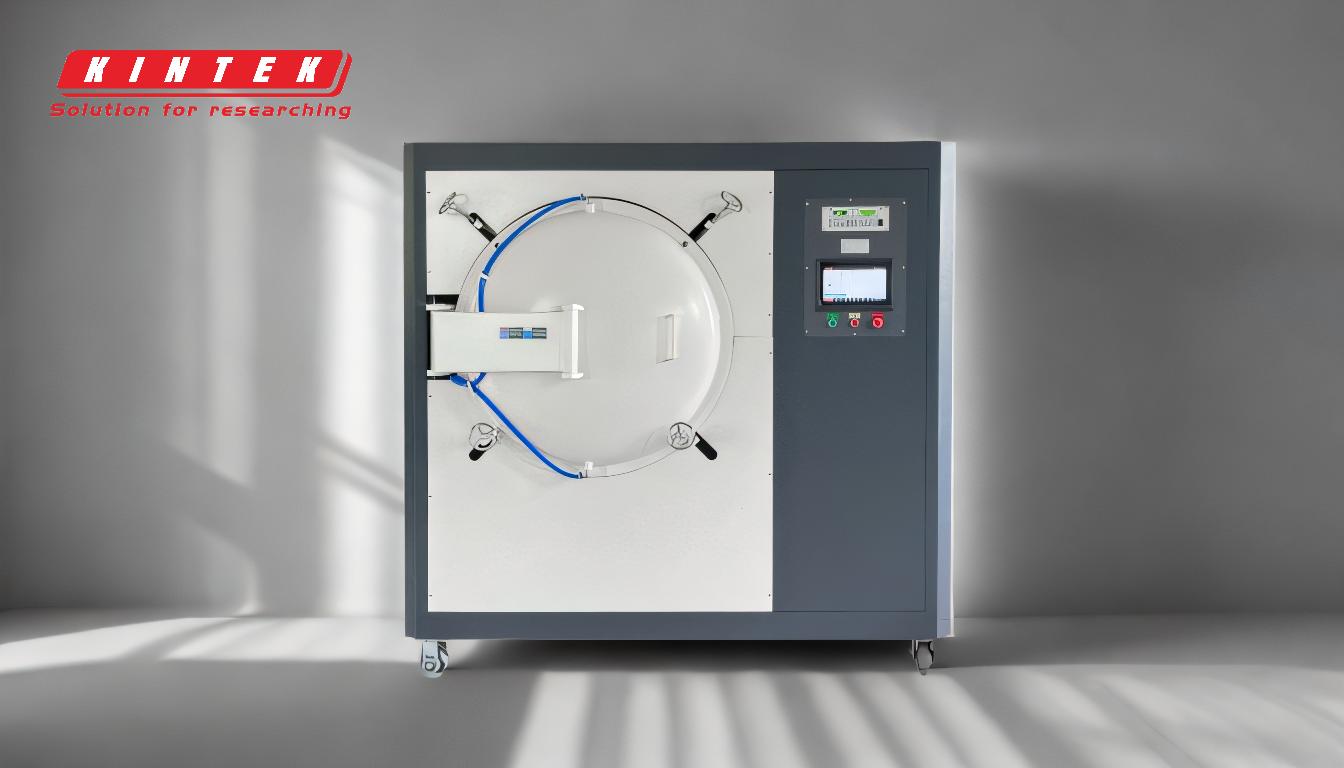
-
Purpose of Protective Gases in Sintering:
- Preventing Oxidation: Protective gases create an inert atmosphere that prevents hot metals from reacting with oxygen, which can lead to oxidation and degradation of the material.
- Preventing Decarburization: In the case of carbon-containing materials, protective gases help prevent the loss of carbon, which can weaken the material.
- Maintaining Atmospheric Pressure: These gases help maintain the necessary pressure within the sintering furnace, ensuring consistent sintering conditions.
-
Commonly Used Gases in Sintering:
-
Hydrogen (H₂):
- Properties: Hydrogen is a highly reducing gas, which means it can remove oxygen from metal oxides, preventing oxidation.
- Applications: It is often used in sintering processes where reducing conditions are required, such as in the sintering of stainless steel or other alloys.
- Advantages: Hydrogen-based atmospheres can result in more consistent performance and better surface quality.
- Disadvantages: Hydrogen is highly flammable, requiring careful handling and safety measures.
-
Nitrogen (N₂):
- Properties: Nitrogen is an inert gas, meaning it does not react with most materials, making it ideal for creating an inert atmosphere.
- Applications: It is commonly used in the high-heat zones of sintering furnaces to prevent oxidation. Nitrogen is injected through angularly adjusted ports or as transverse laminar jet streams.
- Advantages: Nitrogen is cost-effective, readily available, and safe to use.
- Disadvantages: While effective in preventing oxidation, nitrogen does not have reducing properties, so it may not be suitable for all materials.
-
Carbon Monoxide (CO):
- Properties: Carbon monoxide is a reducing gas that can also act as a carburizing agent, adding carbon to the material being sintered.
- Applications: It is used in sintering processes where both reducing and carburizing effects are desired, such as in the sintering of iron-based materials.
- Advantages: Carbon monoxide can improve the mechanical properties of the sintered material by increasing its carbon content.
- Disadvantages: Carbon monoxide is toxic and requires careful handling and ventilation.
-
-
Selection of Gases Based on Material and Process Requirements:
- Material Considerations: The choice of gas depends on the material being sintered. For example, hydrogen is often used for stainless steel, while nitrogen is preferred for non-reactive materials.
- Process Requirements: The desired outcome of the sintering process also influences the choice of gas. For instance, if carburization is required, carbon monoxide may be the best option.
- Safety and Cost: Safety considerations and cost are also important factors. Nitrogen is generally safer and more cost-effective than hydrogen or carbon monoxide.
-
Injection Methods for Protective Gases:
- Angularly Adjusted Ports: Nitrogen is often injected into the furnace through angularly adjusted ports, ensuring even distribution and effective coverage of the sintering material.
- Transverse Laminar Jet Streams: This method involves injecting the gas in a laminar flow pattern, which helps create a uniform inert atmosphere and prevents localized oxidation.
-
Impact of Gas Selection on Sintering Performance:
- Consistency: The use of appropriate protective gases can lead to more consistent sintering results, with fewer defects and better mechanical properties.
- Surface Quality: Hydrogen-based atmospheres, in particular, can improve the surface quality of sintered parts by reducing surface oxides.
- Mechanical Properties: The choice of gas can also affect the mechanical properties of the sintered material, such as hardness, strength, and toughness.
In summary, the selection of gases in sintering is a critical factor that influences the quality, consistency, and performance of the final product. Hydrogen, nitrogen, and carbon monoxide are the most commonly used gases, each offering unique advantages and challenges. The choice of gas should be based on the material being sintered, the desired outcomes, and safety considerations. Proper injection methods and gas management are also essential to ensure effective sintering and high-quality results.
Summary Table:
Gas | Properties | Applications | Advantages | Disadvantages |
---|---|---|---|---|
Hydrogen (H₂) | Highly reducing gas, prevents oxidation by removing oxygen from metal oxides | Sintering of stainless steel and alloys | Consistent performance, better surface quality | Highly flammable, requires careful handling |
Nitrogen (N₂) | Inert gas, does not react with most materials | High-heat zones to prevent oxidation | Cost-effective, readily available, safe to use | No reducing properties, may not suit all materials |
Carbon Monoxide (CO) | Reducing gas, acts as a carburizing agent | Sintering of iron-based materials where carburization is needed | Improves mechanical properties by increasing carbon content | Toxic, requires careful handling and ventilation |
Need help selecting the right gas for your sintering process? Contact our experts today!