Vapor deposition is a process used to create thin films or coatings on a substrate by depositing vaporized material onto its surface. This technique is widely used in industries such as semiconductors, optics, and protective coatings. The process involves converting a solid or liquid material into a vapor, which then condenses onto a substrate to form a thin, uniform layer. There are two main types of vapor deposition: physical vapor deposition (PVD) and chemical vapor deposition (CVD). PVD involves physically vaporizing the material, while CVD relies on chemical reactions to deposit the material. Both methods require controlled environments, often involving vacuum chambers, precise temperature regulation, and specific gas pressures. The result is a highly durable, corrosion-resistant, and temperature-tolerant coating.
Key Points Explained:
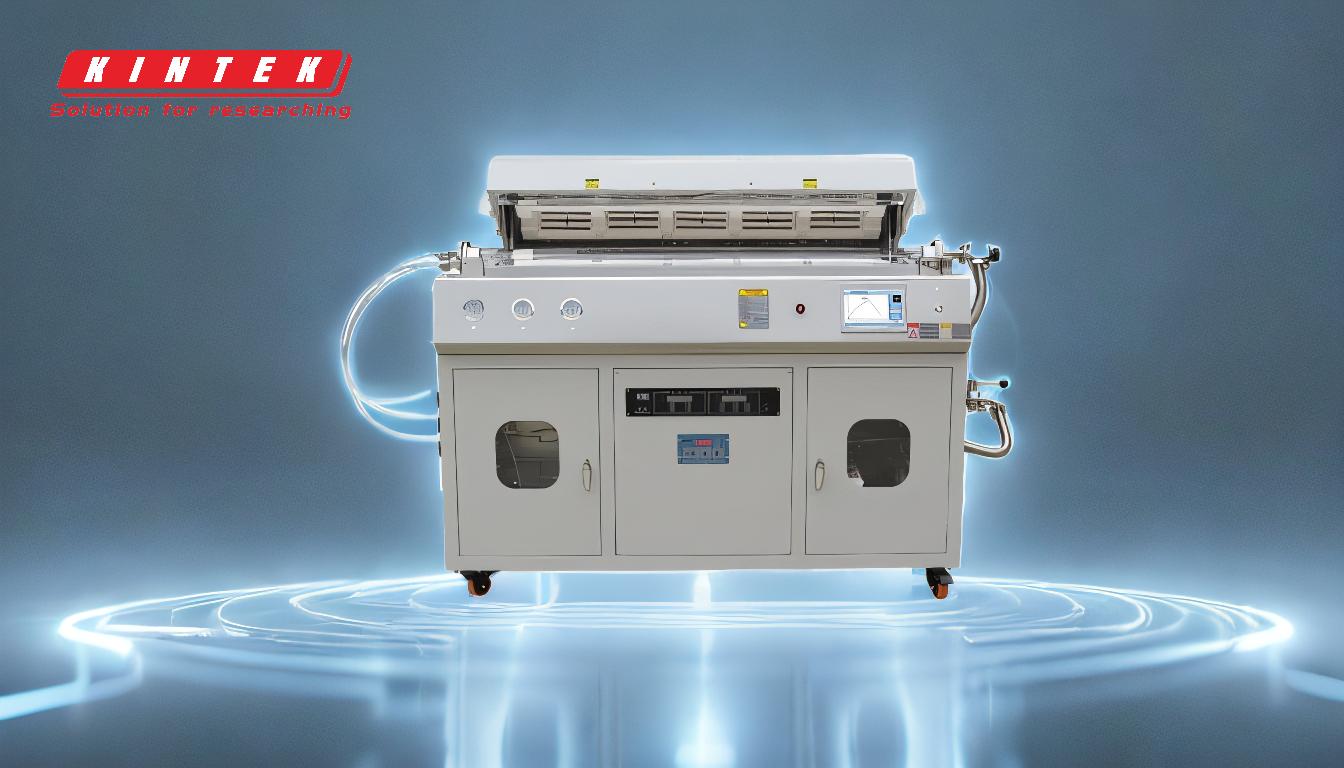
-
Overview of Vapor Deposition:
- Vapor deposition is a process where materials are deposited onto a substrate in the form of a thin film.
- The material is first vaporized and then condensed onto the substrate, creating a uniform layer.
- This technique is essential in industries like semiconductors, optics, and protective coatings.
-
Types of Vapor Deposition:
-
Physical Vapor Deposition (PVD):
- Involves physically vaporizing the target material, often using heat or high-energy ions.
- The vaporized material is then deposited onto the substrate.
- Common PVD methods include sputtering and thermal evaporation.
- PVD is known for creating durable, corrosion-resistant coatings that can withstand high temperatures.
-
Chemical Vapor Deposition (CVD):
- Relies on chemical reactions to deposit the material onto the substrate.
- The substrate is placed in a reaction chamber filled with a gaseous form of the coating material.
- The gas reacts with the substrate or decomposes to form a solid coating.
- CVD can produce highly uniform and conformal coatings, making it ideal for complex geometries.
-
Physical Vapor Deposition (PVD):
-
Key Processes in Vapor Deposition:
-
Low-Pressure Chemical Vapor Deposition (LPCVD):
- A type of CVD that operates at reduced pressures to improve film uniformity and reduce impurities.
- Commonly used in semiconductor manufacturing.
-
Low-Pressure Plasma Spraying (LPPS):
- Uses plasma to activate reactive gases and deposit materials.
- Often used for creating coatings with specific mechanical or electrical properties.
-
Thermal Vapor Deposition:
- Involves heating a solid material in a high vacuum chamber to produce vapor pressure.
- The vaporized material then condenses onto the substrate to form a thin film.
- Typically operates at temperatures between 250 to 350 degrees Celsius.
-
Low-Pressure Chemical Vapor Deposition (LPCVD):
-
Components of a Vapor Deposition System:
-
Heat Source:
- Used to vaporize the target material in PVD or to activate chemical reactions in CVD.
-
Vacuum Chamber:
- Provides a controlled environment with low pressure to prevent contamination and ensure uniform deposition.
-
Target Material:
- The material to be deposited, which can be a metal, semiconductor, or other solid.
-
Substrate:
- The surface onto which the material is deposited, often made of glass, silicon, or other materials.
-
Gas Supply:
- In CVD, reactive gases are introduced into the chamber to facilitate the deposition process.
-
Temperature Control:
- Precise regulation of substrate and chamber temperature is crucial for achieving the desired film properties.
-
Heat Source:
-
Applications of Vapor Deposition:
-
Semiconductors:
- Used to deposit thin films of materials like silicon, silicon dioxide, and metals onto semiconductor wafers.
-
Optics:
- Applied to create anti-reflective coatings, mirrors, and other optical components.
-
Protective Coatings:
- Provides wear-resistant, corrosion-resistant, and thermal barrier coatings for tools, aerospace components, and medical devices.
-
Decorative Coatings:
- Used in the automotive and jewelry industries to create aesthetically pleasing finishes.
-
Semiconductors:
-
Advantages of Vapor Deposition:
-
High Precision:
- Allows for the deposition of extremely thin and uniform films, often at the nanoscale.
-
Versatility:
- Can deposit a wide range of materials, including metals, ceramics, and polymers.
-
Durability:
- Produces coatings that are highly resistant to wear, corrosion, and high temperatures.
-
Scalability:
- Suitable for both small-scale laboratory research and large-scale industrial production.
-
High Precision:
-
Challenges and Considerations:
-
Cost:
- Equipment and operational costs can be high, especially for advanced techniques like CVD.
-
Complexity:
- Requires precise control of parameters such as temperature, pressure, and gas flow.
-
Material Limitations:
- Not all materials can be easily vaporized or deposited using these methods.
-
Environmental Concerns:
- Some processes involve hazardous gases or high energy consumption, requiring careful handling and disposal.
-
Cost:
In summary, vapor deposition is a versatile and precise method for creating thin films and coatings with a wide range of applications. By understanding the different types of vapor deposition, key processes, and system components, one can appreciate the technology's role in modern manufacturing and materials science.
Summary Table:
Aspect | Details |
---|---|
Types | - Physical Vapor Deposition (PVD) |
- Chemical Vapor Deposition (CVD) | |
Key Processes | - Low-Pressure Chemical Vapor Deposition (LPCVD) |
- Low-Pressure Plasma Spraying (LPPS)
- Thermal Vapor Deposition | | Applications | - Semiconductors
- Optics
- Protective Coatings
- Decorative Coatings | | Advantages | - High Precision
- Versatility
- Durability
- Scalability | | Challenges | - High Cost
- Complexity
- Material Limitations
- Environmental Concerns |
Interested in vapor deposition for your applications? Contact us today to learn more!