When hydraulic pressure is too low in a system, particularly in equipment like a hydraulic hot press, it can lead to a range of operational issues. These issues can affect the quality of the output, the efficiency of the machine, and even pose safety risks. Below is a detailed explanation of the implications of low hydraulic pressure and how it impacts the performance of hydraulic systems.
Key Points Explained:
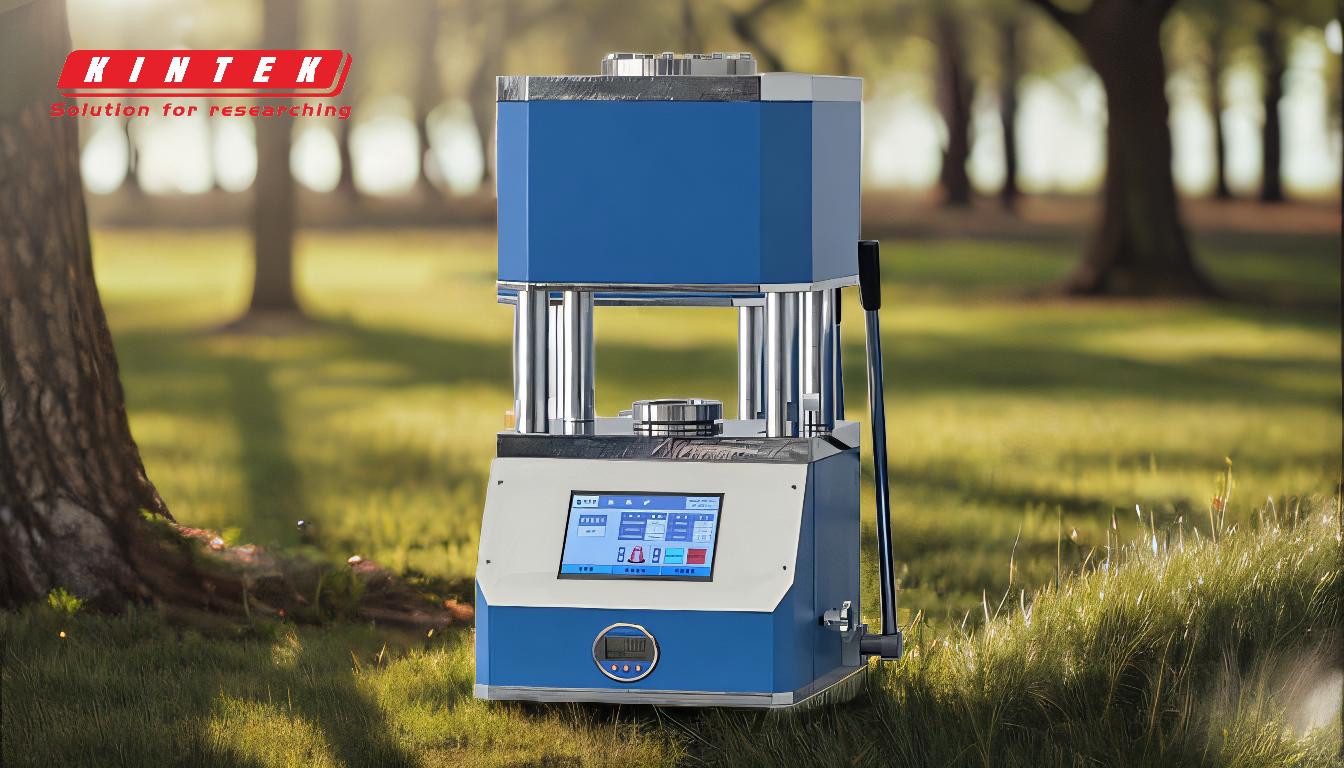
-
Inadequate Pressure for Proper Adhesion:
- Explanation: In applications like heat pressing rhinestones, spangles, or white toner transfers, precise pressure is essential for proper adhesion. If the hydraulic pressure is too low, the pressure applied to the material will be insufficient, leading to poor adhesion and potentially causing the materials to peel off or fail to transfer correctly.
- Impact: This can result in defective products, increased waste, and the need for rework, which can be costly and time-consuming.
-
Reduced Efficiency and Performance:
- Explanation: Hydraulic systems rely on adequate pressure to function efficiently. Low pressure can cause the system to operate sluggishly, reducing the speed and effectiveness of the machine. For example, in a hydraulic hot press, low pressure can lead to longer cycle times and inconsistent results.
- Impact: Reduced efficiency can lead to slower production rates and increased energy consumption, as the system may need to work harder to achieve the desired results.
-
Increased Wear and Tear on Components:
- Explanation: When hydraulic pressure is too low, the system may compensate by running components at higher speeds or for longer durations. This can lead to increased wear and tear on hydraulic cylinders, pumps, and seals.
- Impact: Over time, this can result in more frequent maintenance requirements, higher repair costs, and potential downtime for the equipment.
-
Risk of System Failure:
- Explanation: Consistently operating at low hydraulic pressure can strain the system, potentially leading to catastrophic failure. Components such as hydraulic hoses, valves, and pumps are designed to operate within specific pressure ranges. Operating outside these ranges can cause them to fail prematurely.
- Impact: System failure can lead to unplanned downtime, costly repairs, and potential safety hazards for operators.
-
Inconsistent Product Quality:
- Explanation: In manufacturing processes that require precise pressure, such as heat pressing, low hydraulic pressure can lead to inconsistent product quality. Variations in pressure can cause differences in the final product, such as uneven adhesion or incomplete transfers.
- Impact: Inconsistent quality can lead to customer dissatisfaction, increased returns, and damage to the brand's reputation.
-
Safety Concerns:
- Explanation: Low hydraulic pressure can also pose safety risks. For instance, if the pressure is too low, the machine may not hold the material securely, leading to slippage or misalignment during operation. This can result in accidents or injuries to operators.
- Impact: Safety incidents can lead to legal liabilities, increased insurance costs, and potential harm to employees.
-
Difficulty in Achieving Desired Results:
- Explanation: In applications where precise pressure is critical, such as in the production of high-quality prints or transfers, low hydraulic pressure can make it difficult to achieve the desired results. This is especially true for materials that require a specific amount of pressure to bond correctly.
- Impact: The inability to achieve the desired results can lead to increased material waste, higher production costs, and potential delays in meeting customer orders.
Conclusion:
Maintaining the correct hydraulic pressure is essential for the optimal performance of hydraulic systems, especially in precision applications like those involving a hydraulic hot press. Low hydraulic pressure can lead to a host of problems, including poor product quality, reduced efficiency, increased wear and tear, and safety risks. Regular monitoring and maintenance of hydraulic systems are crucial to ensure that they operate within the required pressure ranges, thereby avoiding these issues and ensuring consistent, high-quality output.
Summary Table:
Issue | Explanation | Impact |
---|---|---|
Inadequate Adhesion | Insufficient pressure leads to poor material adhesion. | Defective products, increased waste, and rework costs. |
Reduced Efficiency | Low pressure causes sluggish operation and longer cycle times. | Slower production, higher energy consumption, and inconsistent results. |
Increased Wear and Tear | Components run harder, leading to faster degradation. | Frequent maintenance, higher repair costs, and equipment downtime. |
Risk of System Failure | Operating outside pressure ranges strains components, risking failure. | Unplanned downtime, costly repairs, and safety hazards. |
Inconsistent Product Quality | Variations in pressure cause uneven adhesion or incomplete transfers. | Customer dissatisfaction, increased returns, and brand reputation damage. |
Safety Concerns | Low pressure may cause material slippage or misalignment, risking accidents. | Legal liabilities, higher insurance costs, and potential employee harm. |
Difficulty Achieving Results | Precise pressure is critical for high-quality outputs; low pressure hinders it. | Increased material waste, higher costs, and delays in meeting orders. |
Ensure your hydraulic system operates at peak performance—contact our experts today to avoid costly downtime and safety risks!