Using a furnace, whether for industrial or laboratory purposes, involves several hazards that must be carefully managed to ensure safety. These hazards include fire risks, burns, electrical dangers, and exposure to harmful gases or chemicals. Proper precautions, such as ensuring equipment is well-maintained, following safety protocols, and using appropriate safety features, are essential to mitigate these risks. Below, we explore the key hazards and safety measures in detail.
Key Points Explained:
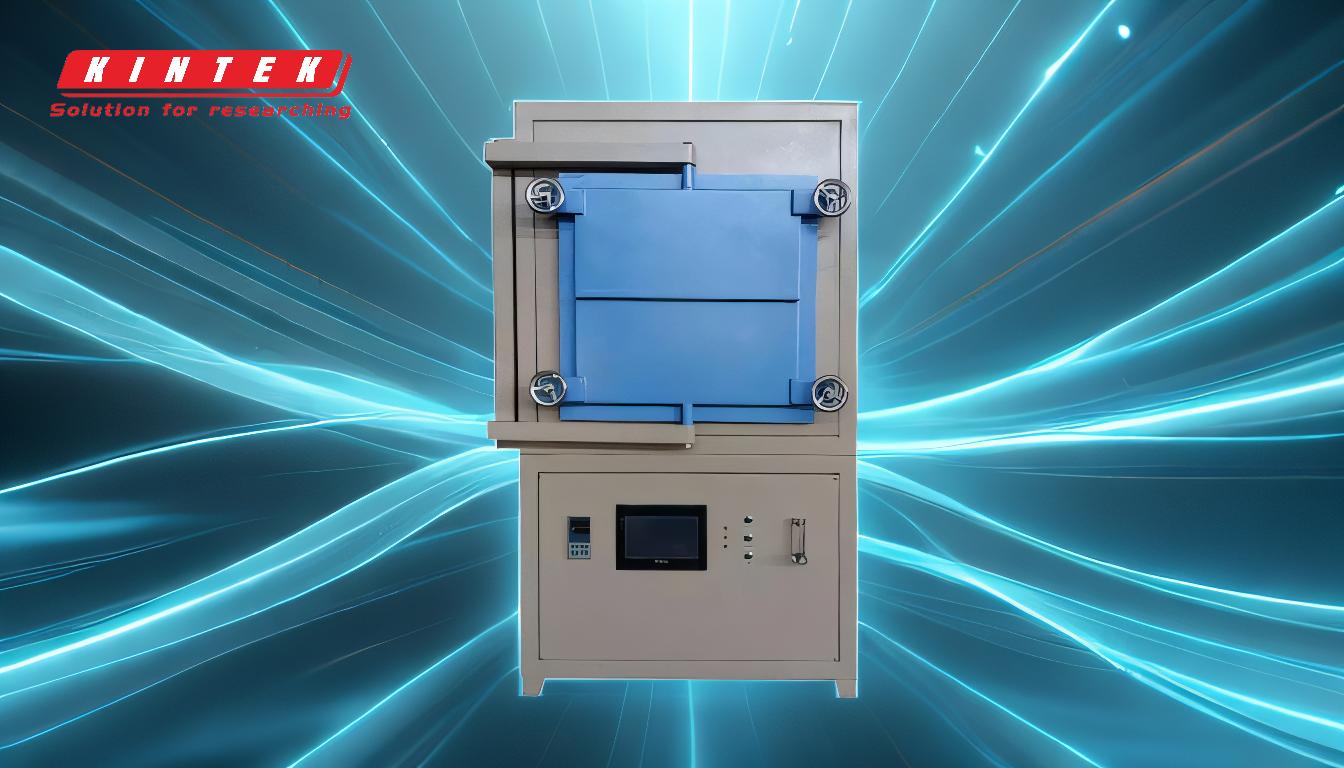
-
Fire Risks
- Furnaces operate at high temperatures, which can pose a significant fire hazard, especially if flammable materials are nearby or if the furnace is used for experiments involving combustible gases like hydrogen.
-
Prevention Measures:
- Ensure the furnace is placed in a well-ventilated area away from flammable substances.
- Use specialized furnaces designed for handling dangerous gases, as ordinary tube furnaces may not be suitable.
- Install fire suppression systems and ensure fire extinguishers are readily accessible.
-
Burns and Physical Injuries
- The high temperatures of furnaces can cause severe burns if operators come into contact with hot surfaces or materials.
-
Prevention Measures:
- Always wear appropriate personal protective equipment (PPE), such as heat-resistant gloves and safety goggles.
- Avoid touching the furnace or workpieces immediately after operation; allow them to cool sufficiently.
- Use tools like tongs or insulated handles to handle hot materials.
-
Electrical Hazards
- Furnaces often involve high-voltage components, which can pose electrical risks if not properly managed.
-
Prevention Measures:
- Ensure the furnace's electrical system is regularly inspected and maintained.
- Check that insulation resistance and grounding are adequate to prevent electrical shocks.
- Turn off the power before making any adjustments or performing maintenance.
-
Exposure to Harmful Gases and Chemicals
- Certain furnace processes, such as vacuum furnaces or those involving hydrogen treatment, can release hazardous gases or byproducts.
-
Prevention Measures:
- Use furnaces with proper ventilation systems to prevent the accumulation of harmful gases.
- Ensure the furnace is operated in a well-ventilated area or under a fume hood.
- Follow specific safety protocols for handling dangerous gases, such as using pure nitrogen or other inert gases when required.
-
Vacuum Furnace-Specific Hazards
- Vacuum furnaces have additional risks, such as pressure-related issues and the need for airtight seals.
-
Prevention Measures:
- Regularly check the furnace's sealing system, including vacuum grease and seal rings, to maintain airtightness.
- Ensure the pressure rise rate does not exceed specified limits to avoid equipment failure.
- Use rapid cooling devices and avoid inappropriate cooling gases (e.g., nitrogen for titanium alloys) to prevent chemical reactions.
-
Equipment Maintenance and Safety Features
- Proper maintenance and the use of advanced safety features can significantly reduce risks.
-
Prevention Measures:
- Choose furnaces with safety features like auto-recovery after power failure, overheat prevention devices, and key lock functions.
- Regularly inspect and maintain the furnace's water, gas, and electrical systems to ensure they are functioning correctly.
- Follow manufacturer guidelines for cleaning and maintenance to prevent malfunctions.
-
Operational Safety Protocols
- Adhering to established safety procedures is critical to minimizing hazards.
-
Prevention Measures:
- Train all operators on proper furnace usage and emergency procedures.
- Avoid opening the furnace door while it is hot, and use caution when loading or unloading materials.
- Ensure all safety devices, such as alarms and interlock protections, are operational before use.
By understanding these hazards and implementing the corresponding safety measures, operators can significantly reduce the risks associated with using furnaces. Proper training, regular maintenance, and adherence to safety protocols are essential for ensuring a safe working environment.
Summary Table:
Hazard | Prevention Measures |
---|---|
Fire Risks | - Place in well-ventilated areas, use specialized furnaces, install fire suppression. |
Burns and Physical Injuries | - Wear PPE, allow materials to cool, use insulated tools. |
Electrical Hazards | - Inspect electrical systems, ensure proper grounding, turn off power before maintenance. |
Harmful Gases and Chemicals | - Use ventilation systems, operate under fume hoods, follow gas safety protocols. |
Vacuum Furnace-Specific Hazards | - Check seals, monitor pressure rise rates, use appropriate cooling gases. |
Equipment Maintenance | - Choose furnaces with safety features, inspect water/gas/electrical systems regularly. |
Operational Safety | - Train operators, avoid opening hot doors, ensure safety devices are functional. |
Ensure your furnace operations are safe and efficient—contact our experts today for personalized advice!