A calcining kiln is a specialized type of rotary kiln designed to perform calcination, a thermal process that involves heating materials to high temperatures to induce chemical dissociation or remove bound moisture. This process is crucial in industries such as cement production, metallurgy, and chemical manufacturing. Calcining kilns are engineered to achieve precise temperature control and efficient heat transfer, ensuring optimal chemical reactions. They typically feature advanced burners, heat recuperators, and customizable designs to accommodate various materials and fuel sources. These kilns play a vital role in producing inorganic materials like calcium oxide and are integral to processes requiring high-temperature thermal treatment.
Key Points Explained:
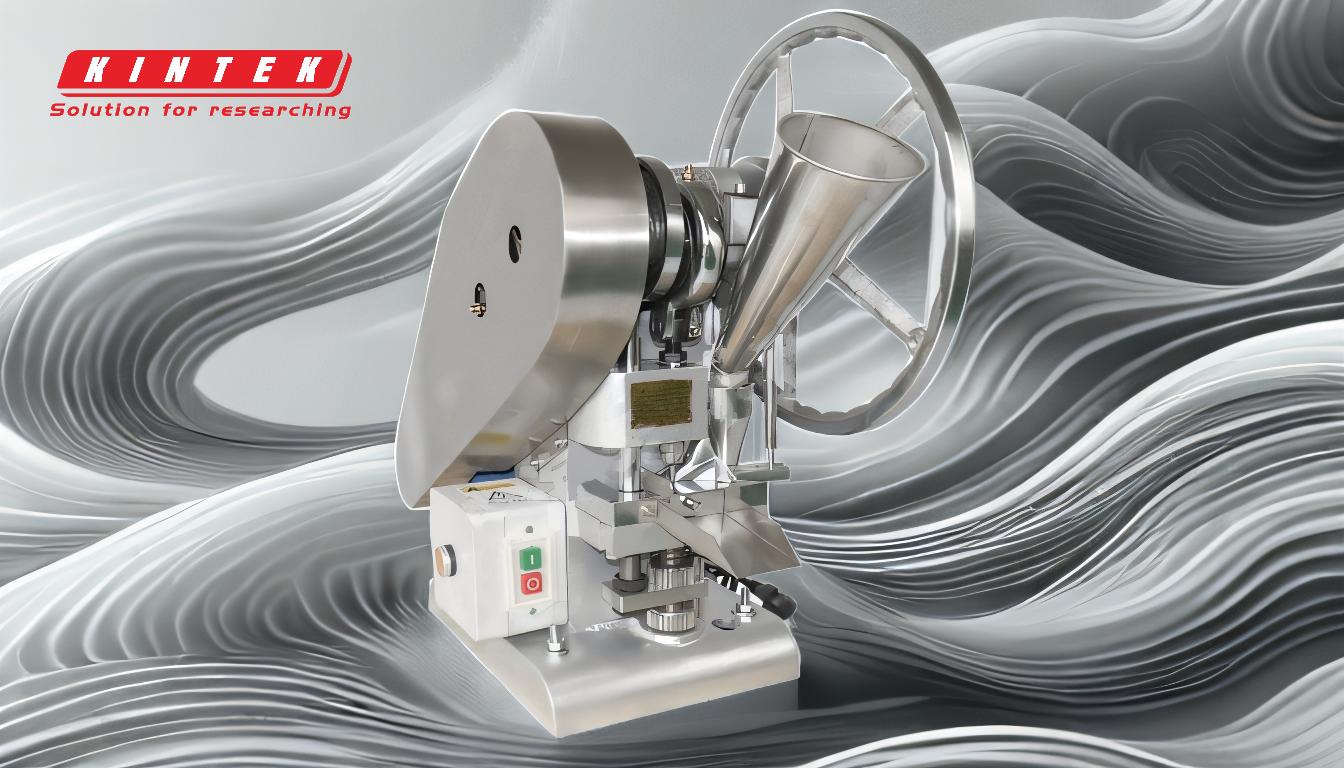
-
Definition and Purpose of Calcination:
- Calcination is a thermal process that heats materials to high temperatures to achieve chemical dissociation or remove bound moisture.
- It is commonly used in the production of inorganic materials, such as converting calcium carbonate (CaCO₃) into calcium oxide (CaO) and carbon dioxide (CO₂).
- This process is essential in industries like cement manufacturing, metallurgy, and chemical processing.
-
Design and Structure of Calcining Kilns:
- Calcining kilns are typically rotary kilns, which are long, horizontal cylinders tilted on their axis to facilitate material movement.
- They are designed to achieve high bed temperatures necessary for chemical reactions, ensuring efficient processing.
- Key structural features include burners, heat recuperators, and cooling systems to optimize thermal efficiency.
-
Burner Systems:
- Burners in calcining kilns supply the energy required for the calcination process.
- They are often mounted on the discharge end housing and can accommodate various fuel sources, including natural gas, propane, diesel, and pulverized coal.
- Selecting the right burner is critical for ensuring efficient and consistent heating.
-
Thermal Efficiency and Heat Recuperation:
- Calcining kilns are designed to maximize thermal efficiency by incorporating heat recuperators, such as pre-heaters, which recover energy from exhaust gases to preheat the feed material.
- Coolers are used to lower the temperature of the processed material for safe handling while also recuperating energy for other uses, such as preheating combustion air.
-
Temperature Control and Customization:
- Calcining kilns offer precise temperature control, often through advanced control systems like TAP control touchscreens.
- They can be customized to meet specific process requirements, including heat patterns, air cooling mechanisms, and measures to prevent metal contamination or gas leakage.
- Customization options ensure the kiln can handle a wide range of materials and processes.
-
Applications and Industry Use:
- Calcining kilns are widely used in industries that require high-temperature processing, such as cement production, where they convert limestone into lime.
- They are also used in metallurgy for ore processing and in chemical manufacturing for producing materials like borax and other inorganic compounds.
-
Environmental and Operational Advantages:
- Modern calcining kilns, such as electric rotary kilns, offer clean and efficient alternatives to traditional fossil fuel-based processes.
- They enable industries to capture and reuse CO₂ emissions, contributing to sustainability efforts.
- The design and operation of these kilns focus on reducing energy consumption and minimizing environmental impact.
By understanding these key points, purchasers and operators of calcining kilns can make informed decisions about selecting, customizing, and operating these critical pieces of equipment to meet their specific industrial needs.
Summary Table:
Key Feature | Description |
---|---|
Purpose | Heats materials to induce chemical dissociation or remove moisture. |
Design | Rotary kilns with burners, heat recuperators, and cooling systems. |
Burner Systems | Supports multiple fuel sources for efficient and consistent heating. |
Thermal Efficiency | Uses heat recuperators and coolers to maximize energy recovery. |
Temperature Control | Advanced systems like TAP control for precise heat management. |
Applications | Cement production, metallurgy, and chemical manufacturing. |
Environmental Benefits | Reduces energy consumption and captures CO₂ emissions for reuse. |
Discover how a calcining kiln can optimize your industrial processes—contact our experts today!