A carbonization furnace is a specialized equipment used to convert organic materials like biomass, wood, and agricultural residues into charcoal through a process called carbonization. This process involves heating the raw materials in an oxygen-limited environment to break down complex organic compounds into carbon-rich charcoal. Carbonization furnaces are essential in industries that produce charcoal for fuel, filtration, or industrial applications. The process typically involves sealing the material in the furnace, heating it to high temperatures, and cooling it before extracting the charcoal. These furnaces are distinct from sintering furnaces, which are used for compacting and forming materials like metals or ceramics under heat and pressure.
Key Points Explained:
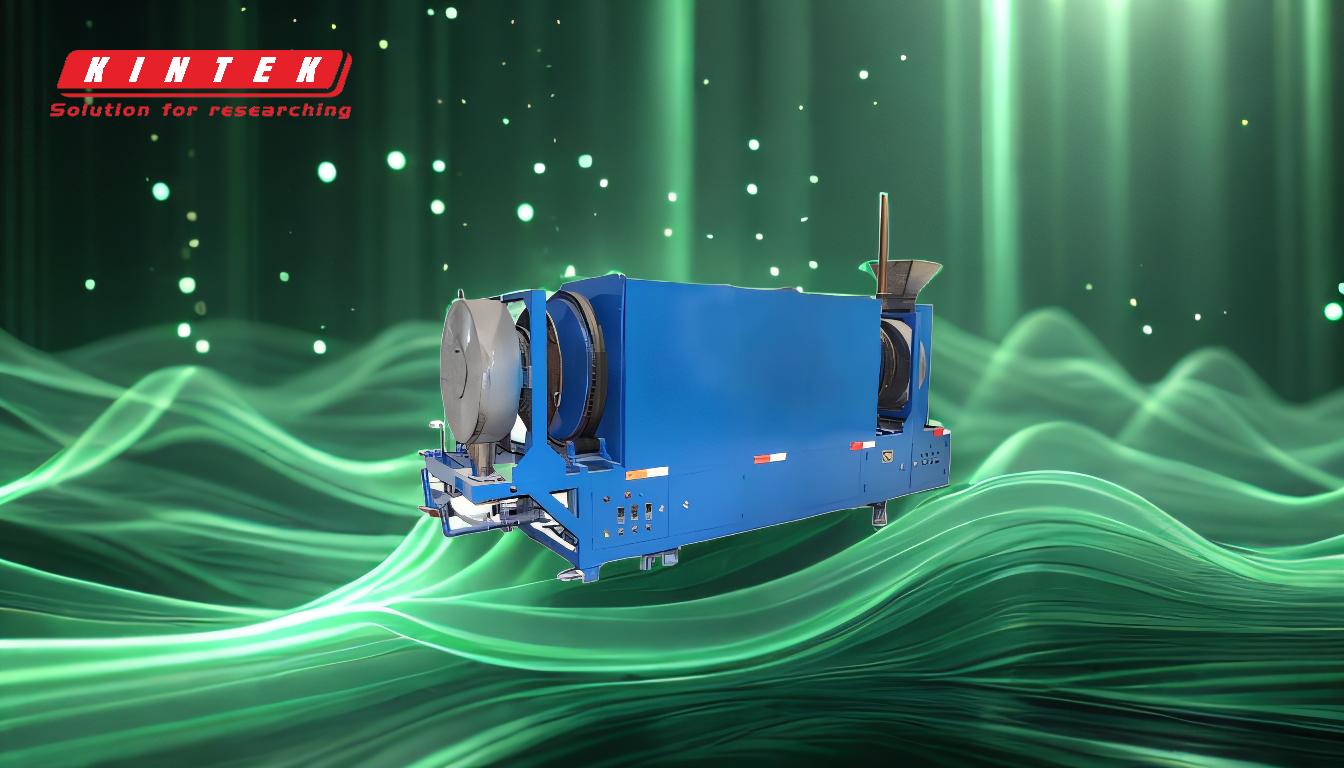
-
Definition and Purpose of a Carbonization Furnace:
- A carbonization furnace is designed to convert organic materials such as biomass, wood, and agricultural residues into charcoal.
- The process involves heating the materials in an oxygen-limited environment to prevent combustion and instead promote the breakdown of organic compounds into carbon-rich charcoal.
- This equipment is widely used in industries that require charcoal for fuel, filtration, or industrial processes.
-
Materials Suitable for Carbonization:
- Biomass briquettes made from sawdust, crop straws, rice husks, bamboo shavings, and grasses are commonly used.
- Woods and forestry residues like pine wood, willow wood, and bamboo are also ideal raw materials for carbonization.
- These materials are chosen for their high carbon content and availability.
-
The Carbonization Process:
- Step 1: Loading the Material: The raw material is placed inside the furnace.
- Step 2: Sealing the Furnace: The furnace is sealed to create an oxygen-limited environment, which is crucial for the carbonization process.
- Step 3: Heating: The material is heated to high temperatures, typically between 300°C and 600°C, to break down the organic compounds.
- Step 4: Cooling and Extraction: After carbonization, the furnace is allowed to cool, and the resulting charcoal is extracted.
-
Applications of Carbonization Furnaces:
- Charcoal Production: Used to produce charcoal for cooking, heating, and industrial applications.
- Biochar Production: Carbonized biomass can be used as biochar for soil improvement and carbon sequestration.
- Filtration: Charcoal produced in these furnaces is often used in water and air filtration systems due to its high adsorption capacity.
-
Comparison with Sintering Furnaces:
- While carbonization furnaces are used for organic materials, sintering furnaces are designed for processing inorganic materials like metals and ceramics.
- Sintering involves compacting powdered materials under heat and pressure to form solid structures, whereas carbonization focuses on thermal decomposition of organic matter.
-
Advantages of Carbonization Furnaces:
- Efficiency: They provide a controlled environment for efficient conversion of organic waste into valuable charcoal.
- Sustainability: Utilizes renewable resources like biomass and agricultural residues, reducing waste and promoting sustainability.
- Versatility: Can process a wide range of organic materials, making it suitable for various industries.
-
Key Considerations for Purchasing a Carbonization Furnace:
- Capacity: Choose a furnace that matches your production needs.
- Temperature Control: Ensure the furnace offers precise temperature control for consistent results.
- Durability: Look for furnaces made from high-quality materials to withstand high temperatures and prolonged use.
- Safety Features: Opt for furnaces with safety mechanisms to prevent accidents during operation.
By understanding the functionality, applications, and benefits of carbonization furnaces, purchasers can make informed decisions when selecting equipment for their specific needs.
Summary Table:
Aspect | Details |
---|---|
Purpose | Converts organic materials into charcoal through carbonization. |
Materials Used | Biomass, wood, agricultural residues (e.g., sawdust, rice husks, bamboo). |
Process Steps | 1. Load material. 2. Seal furnace. 3. Heat (300°C–600°C). 4. Cool and extract. |
Applications | Charcoal production, biochar for soil, water/air filtration. |
Key Advantages | Efficient, sustainable, versatile, and durable. |
Purchase Considerations | Capacity, temperature control, durability, safety features. |
Ready to transform organic waste into valuable resources? Contact us today to find the perfect carbonization furnace for your needs!