A chamber furnace, often referred to as a muffle or box furnace, is a specialized heating device designed for precise temperature control and uniform heating within a closed chamber. It is widely used in laboratories for applications such as drying, baking, curing, ashing, and heat treatment of materials. The furnace features heating elements on the perimeter of the chamber, ensuring even heat distribution. Constructed with refractory materials, it can maintain high temperatures for extended periods without degradation. Modern chamber furnaces include advanced features like intelligent temperature control algorithms, over-temperature protection, and user-friendly interfaces, making them essential equipment for laboratory and industrial applications.
Key Points Explained:
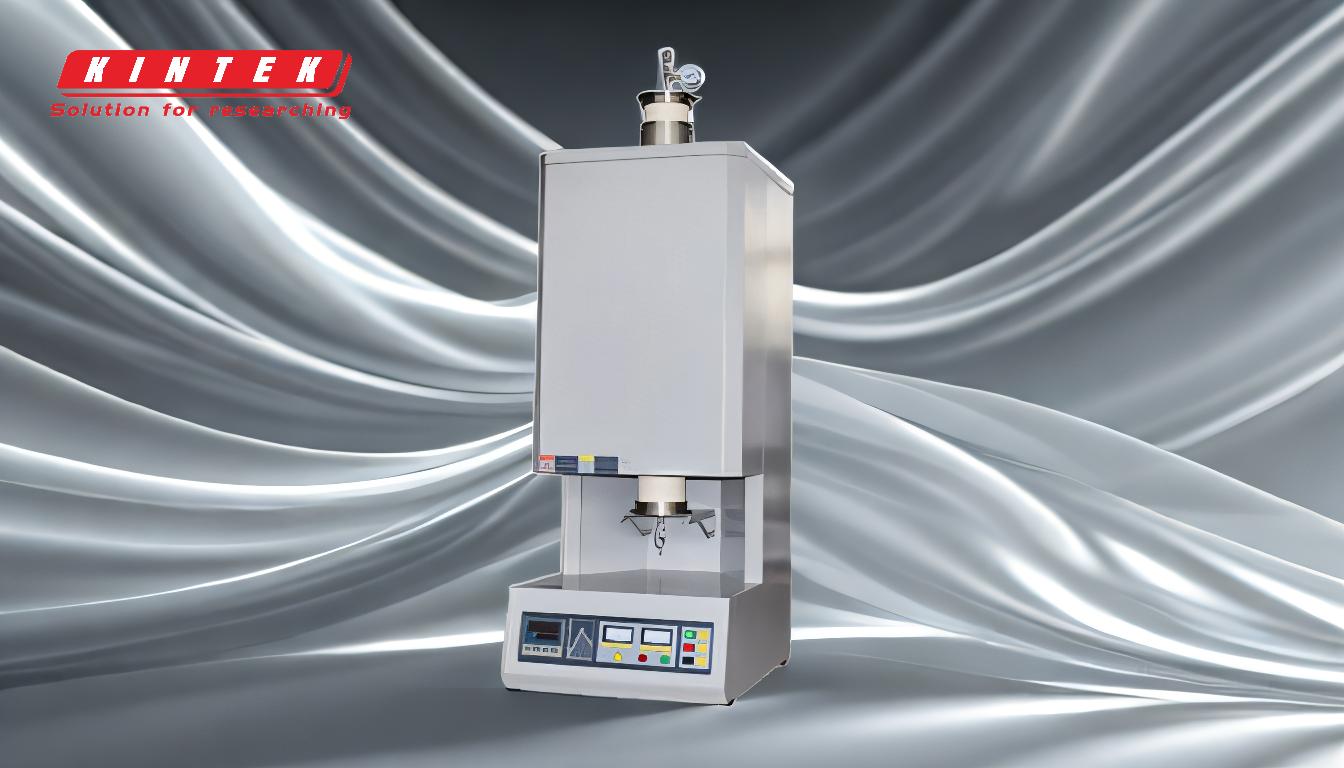
-
Definition and Purpose:
- A chamber furnace is a closed-box heating device used in laboratories and industrial settings for precise and uniform heating of materials.
- Its primary purpose is to perform tasks such as drying, baking, curing, ashing, and heat treatment, making it a versatile tool for material processing.
-
Design and Construction:
- The furnace is typically box-shaped, with internal dimensions ranging from 10 to 50 cm on each side, making it compact yet spacious enough for various sample sizes.
- It features a triple-walled design with zirconia fiberboard insulation, ensuring a cool exterior for user safety and zero skin temperature during operation.
- Heating elements are strategically placed on the perimeter of the chamber to provide uniform heat distribution.
-
Key Features:
- Temperature Control: Equipped with intelligent adjustment algorithms, the furnace ensures precise temperature regulation, which is critical for laboratory applications.
- Safety Mechanisms: Automatic protection alarms for over-temperature, over-current, and leakage enhance operational safety.
- User-Friendly Interface: Many models come with computer interfaces and integrated software for easy operation and monitoring.
- Durability: Constructed with refractory materials, the furnace can withstand high temperatures and continuous operation for months without degradation.
-
Applications:
- Drying: Removes moisture from samples without causing thermal degradation.
- Baking: Heats samples without dehumidification, often used in material testing.
- Curing: Alters the physical or chemical properties of samples, commonly used in polymer and composite processing.
- Ashing: Burns off organic material from samples, leaving behind inorganic residue for analysis.
- Heat Treatment: Used in metallurgy and material science to alter the properties of metals and alloys.
-
Advantages Over Other Furnace Types:
- Compared to tube furnaces, chamber furnaces offer larger working spaces, making them suitable for bulkier samples.
- The box-shaped design with a side door allows for quick and easy access to the chamber, improving workflow efficiency.
- The uniform heating capability ensures consistent results across all samples placed within the chamber.
-
Operational Workflow:
- The user sets a desired temperature (setpoint) on the furnace controller.
- The furnace gradually heats the chamber, applying heat evenly to the samples inside.
- Advanced models may include programmable heating cycles for complex processes.
-
Safety and Maintenance:
- The triple-walled construction and insulation ensure safe operation by maintaining a cool exterior.
- Regular maintenance, such as checking heating elements and insulation, ensures long-term reliability and performance.
In summary, a chamber furnace is an indispensable tool in laboratories and industries, offering precise temperature control, uniform heating, and advanced safety features. Its robust design and versatility make it suitable for a wide range of applications, from material testing to heat treatment processes.
Summary Table:
Key Aspect | Details |
---|---|
Definition | Closed-box heating device for precise and uniform heating in labs. |
Design | Box-shaped, triple-walled with zirconia fiberboard insulation. |
Key Features | Intelligent temperature control, safety mechanisms, user-friendly interface. |
Applications | Drying, baking, curing, ashing, heat treatment. |
Advantages | Larger workspace, uniform heating, durable construction. |
Safety & Maintenance | Cool exterior, regular maintenance for long-term reliability. |
Ready to enhance your lab's capabilities? Contact us today to find the perfect chamber furnace for your needs!