A furnace used in melting non-ferrous metals, such as aluminum, is a specialized piece of equipment designed to efficiently and uniformly heat and melt metals for casting or other industrial processes. The most common types include induction melting furnaces, crucible furnaces, reverberatory furnaces, and vertical melting furnaces. These furnaces vary in design, heat source, and operational efficiency, catering to different production scales and requirements. Induction furnaces, for instance, use electromagnetic induction for heating and are highly efficient, while crucible furnaces are preferred for their flexibility in alloy changes. Vertical melting furnaces are ideal for small to medium-sized operations due to their compact design and high thermal efficiency. Each type of furnace is equipped with advanced features like temperature control, safety mechanisms, and energy-saving technologies to ensure reliable and cost-effective operation.
Key Points Explained:
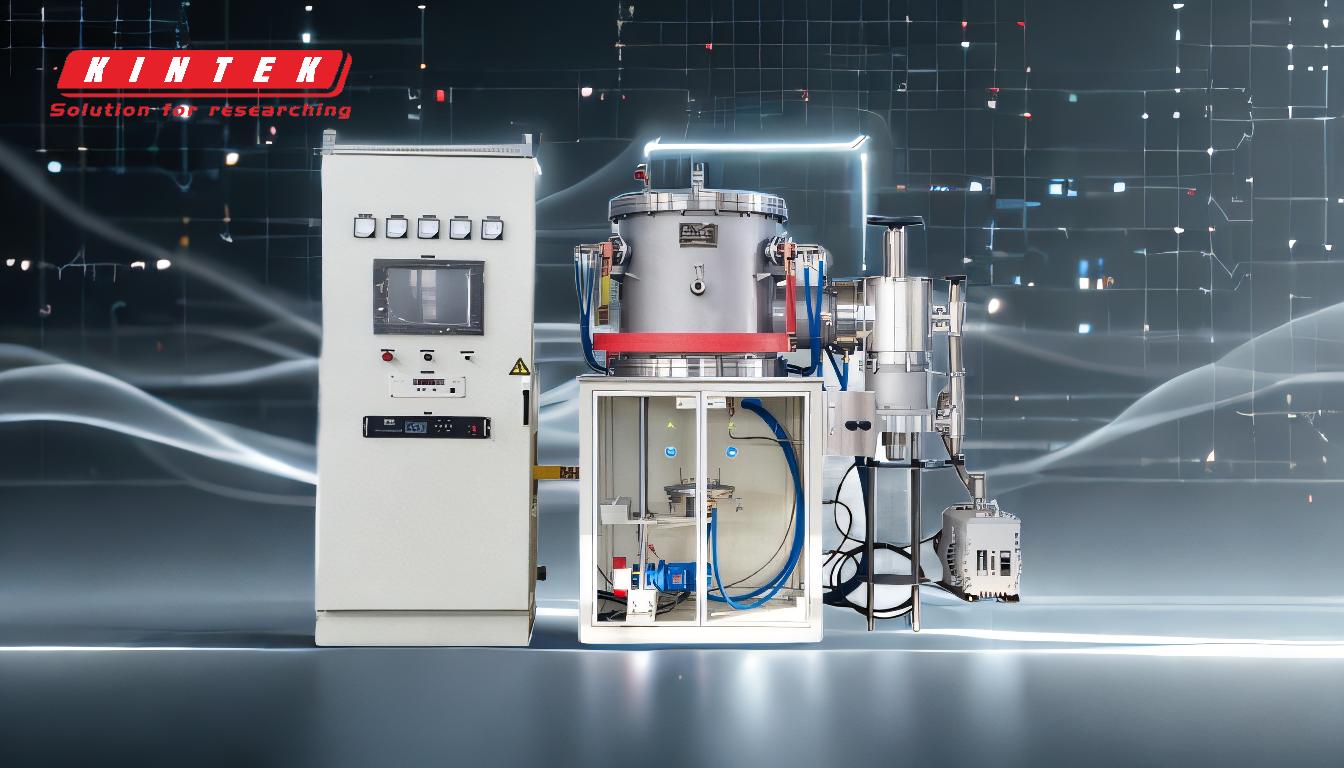
-
Types of Furnaces for Non-Ferrous Metal Melting
- Induction Melting Furnaces: These furnaces use electromagnetic induction to generate heat, making them highly efficient and suitable for continuous operation. They are compact, energy-efficient, and feature advanced safety mechanisms like overcurrent and overheating protection.
- Crucible Furnaces: Commonly used in foundries, these furnaces are flexible and ideal for frequent alloy changes. They can be heated by natural gas, oil, electric resistance, or induction.
- Reverberatory Furnaces: These are used for larger capacity operations and are typically gas-fired or electric resistance-based. They are designed for high-volume melting.
- Vertical Melting Furnaces: These are compact and efficient, often used in small and medium-sized enterprises. They feature a vertical flue design that enhances thermal efficiency and energy performance.
-
Key Features and Advantages
- Efficiency: Induction furnaces have an effective output power of over 95%, while vertical furnaces achieve thermal efficiencies exceeding 50%.
- Flexibility: Crucible furnaces allow for easy alloy changes and extended shutdowns, making them versatile for foundries.
- Compact Design: Induction and vertical furnaces are lightweight, movable, and occupy minimal space, making them ideal for smaller operations.
- Safety and Reliability: Modern furnaces come with comprehensive protection functions, such as overvoltage, overcurrent, and water shortage alarms, ensuring safe and durable operation.
- Energy Savings: Advanced designs reduce energy consumption and environmental impact, making them cost-effective and sustainable.
-
Applications and Suitability
- Induction Furnaces: Best for continuous, high-efficiency operations requiring uniform melting and minimal downtime.
- Crucible Furnaces: Ideal for foundries with frequent alloy changes and smaller production scales.
- Vertical Furnaces: Suitable for small to medium-sized enterprises and die-casting industries due to their compact size and high thermal efficiency.
- Reverberatory Furnaces: Designed for large-scale industrial operations requiring high-volume melting.
-
Operational Considerations
- Heat Sources: Furnaces can be powered by natural gas, oil, electric resistance, or induction, depending on the specific requirements and operational scale.
- Temperature Control: Advanced furnaces feature precise temperature regulation and display functions for current, voltage, and time, ensuring optimal melting conditions.
- Maintenance and Durability: Robust construction and integrated protection systems minimize downtime and ensure long-term reliability.
By understanding these key points, a purchaser can make an informed decision based on their specific needs, such as production scale, energy efficiency, and operational flexibility.
Summary Table:
Type | Key Features | Best For |
---|---|---|
Induction Furnaces | Electromagnetic heating, >95% efficiency, compact, advanced safety mechanisms | Continuous, high-efficiency operations with minimal downtime |
Crucible Furnaces | Flexible alloy changes, natural gas/oil/electric heating, versatile | Foundries with frequent alloy changes and smaller production scales |
Reverberatory Furnaces | Gas-fired/electric resistance, high-volume melting | Large-scale industrial operations requiring high-volume melting |
Vertical Furnaces | Compact, >50% thermal efficiency, vertical flue design | Small to medium-sized enterprises and die-casting industries |
Ready to choose the perfect furnace for your needs? Contact our experts today for personalized advice!