Both muffle and tube furnaces are widely used in laboratory and industrial settings for high-temperature applications, but they differ significantly in design, functionality, and suitability for specific tasks. A muffle furnace is designed with a large, enclosed chamber, making it ideal for heating bulkier samples or materials that require uniform heating in an air environment. In contrast, a tube furnace features a cylindrical heating zone and is better suited for applications requiring precise temperature control, gas flow management, and specialized atmospheres. While both can achieve high temperatures, their structural differences influence their use cases, cost, and operational efficiency.
Key Points Explained:
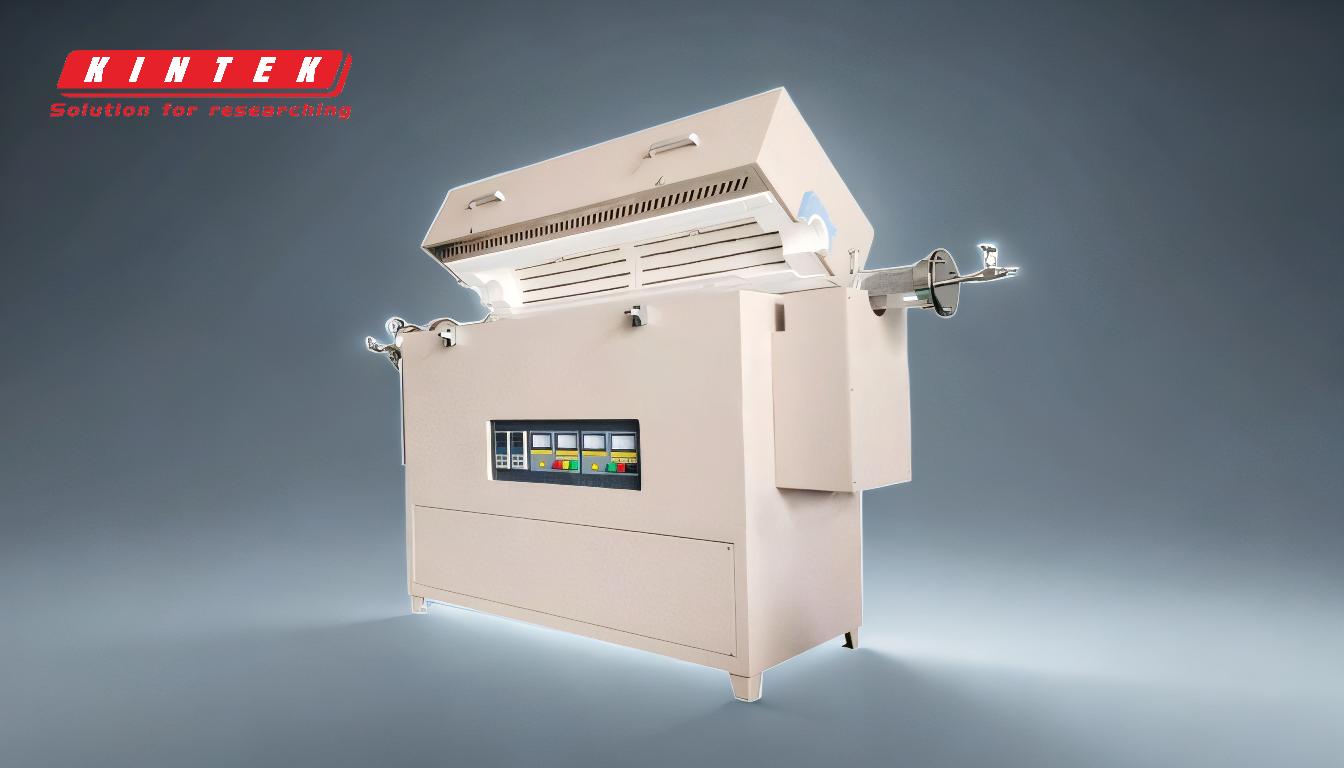
-
Design and Structure:
- Muffle Furnace: Features a large, box-like chamber with a front-loading door. This design allows for easy placement of samples directly into the heating zone, making it suitable for bulkier or irregularly shaped materials.
- Tube Furnace: Utilizes a cylindrical heating tube, often with an upper or side-loading mechanism. This design is more compact and allows for precise control of temperature gradients and gas flow, making it ideal for experiments requiring controlled atmospheres.
-
Heating Zone and Sample Placement:
- Muffle Furnace: Offers a larger heating zone, which simplifies sample placement and is advantageous for heating larger or multiple samples simultaneously. However, it lacks the ability to control the atmosphere within the chamber.
- Tube Furnace: Has a smaller, cylindrical heating zone, which can make sample placement more challenging. However, its design allows for better control of temperature gradients and gas flow, making it suitable for specialized applications.
-
Temperature Control and Atmosphere Management:
- Muffle Furnace: Typically operates in an air environment and is limited to air calcination. It provides uniform heating but lacks the ability to manage gas flow or create specialized atmospheres.
- Tube Furnace: Excels in precise temperature control and atmosphere management. It can pass gases through the tube, enabling processes like inert gas annealing, oxidation, or reduction. This makes it more versatile for advanced applications.
-
Applications:
- Muffle Furnace: Best suited for general heating applications, such as ashing, sintering, or heat treatment of materials that do not require controlled atmospheres. Its larger chamber is ideal for bulk processing.
- Tube Furnace: Ideal for specialized applications, such as chemical vapor deposition, catalyst testing, or experiments requiring precise control of temperature and gas composition.
-
Cost and Maintenance:
- Muffle Furnace: Generally more affordable and easier to maintain due to its simpler design and lack of gas management systems.
- Tube Furnace: More expensive due to its advanced features, such as gas flow control and higher temperature capabilities. It also requires more maintenance to ensure proper gas handling and temperature regulation.
-
Operational Considerations:
- Muffle Furnace: Easier to operate for routine tasks, with minimal setup required. Its front-loading door simplifies loading and unloading samples.
- Tube Furnace: Requires more setup and expertise, particularly for managing gas flow and temperature gradients. Its cylindrical design may complicate sample placement but offers greater flexibility for specialized experiments.
In summary, the choice between a muffle furnace and a tube furnace depends on the specific requirements of the application. A muffle furnace is better for general heating tasks with larger samples, while a tube furnace is more suitable for advanced applications requiring precise temperature and atmosphere control. Understanding these differences ensures optimal selection for your heating needs.
Summary Table:
Feature | Muffle Furnace | Tube Furnace |
---|---|---|
Design | Large, box-like chamber with front door | Cylindrical heating tube |
Heating Zone | Larger, suitable for bulkier samples | Smaller, precise for controlled atmospheres |
Temperature Control | Uniform heating in air environment | Precise control with gas flow management |
Applications | General heating, ashing, sintering | Specialized processes like CVD, catalyst testing |
Cost | More affordable, easier maintenance | More expensive, advanced features |
Ease of Use | Simple setup, front-loading design | Requires expertise for gas and temperature control |
Need help choosing the right furnace for your application? Contact us today for expert advice!