Physical Vapor Deposition (PVD) coating is a vacuum-based process where a solid material is vaporized and then deposited as a thin film onto a substrate. This method is widely used across various industries due to its ability to produce durable, high-quality coatings that enhance the lifespan and performance of products. PVD coatings are applied in a vacuum chamber to ensure cleanliness and precision, and reactive gases can be introduced to alter the coating's properties. The process is environmentally friendly, as it avoids the use of toxic substances, making it a sustainable alternative to traditional coating methods like chrome plating.
Key Points Explained:
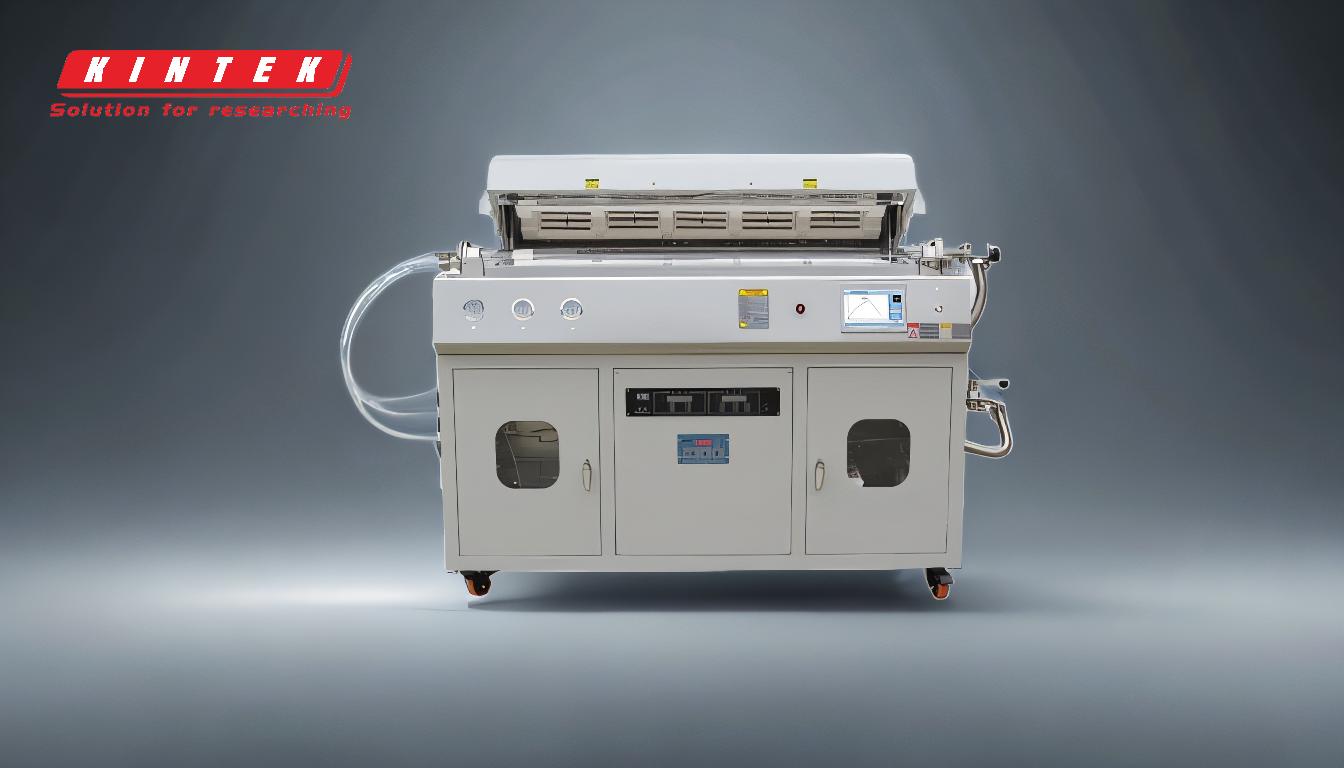
-
Definition and Process of PVD Coating:
- PVD coating involves vaporizing a solid material in a vacuum chamber, which then condenses to form a thin film on a substrate.
- The process occurs under very low pressure (high vacuum) and at relatively low temperatures, ensuring the formation of uniform and high-quality coatings.
- Techniques for vaporizing the material include using a heated crucible, electron beam, ion bombardment from a plasma, or a cathodic arc.
-
Applications of PVD Coating:
- PVD coatings are widely used in decorative and functional applications across various industries.
- Common applications include:
- Jewelry: Enhances durability and aesthetic appeal.
- Door and Window Hardware: Provides corrosion resistance and improves longevity.
- Kitchen and Bathroom Fixtures: Used on faucets, nozzles, and showerheads for both durability and visual appeal.
- Automotive Components: Extends the lifespan of car parts like wheels and pistons.
- Medical Equipment: Improves the performance and durability of surgical tools.
- Sporting Goods: Used in golf clubs and other equipment to enhance performance.
-
Advantages of PVD Coating:
- Durability: PVD coatings can significantly extend the lifespan of products, sometimes by up to ten times, making them last more than 25 years in some cases.
- Environmental Friendliness: Unlike chrome plating, PVD coating does not produce toxic substances, making it a greener alternative.
- Versatility: Suitable for depositing various metals, non-metals, and compound films on planar surfaces.
-
Comparison with Other Coating Methods:
- PVD coating is often compared to chrome plating, but it offers several advantages:
- Non-Toxic: PVD does not involve harmful chemicals, making it safer for both the environment and workers.
- Thinner Coatings: PVD produces very thin coatings, which can be more precise and uniform compared to traditional methods.
- Enhanced Performance: Products with PVD coatings often exhibit better resistance to wear, corrosion, and other forms of degradation.
- PVD coating is often compared to chrome plating, but it offers several advantages:
-
Technical Aspects:
- Vacuum Environment: The use of a vacuum chamber ensures that the coating process is free from contaminants, resulting in high-quality finishes.
- Reactive Gases: Introducing reactive gases during the process can modify the composition of the vaporized material, allowing for the creation of coatings with specific properties.
- Low Temperatures: The relatively low temperatures used in PVD coating make it suitable for a wide range of substrates, including those that might be sensitive to higher temperatures.
In summary, PVD coating is a versatile and environmentally friendly process that offers numerous benefits across a wide range of applications. Its ability to produce durable, high-quality coatings makes it an attractive option for industries looking to enhance the performance and longevity of their products.
Summary Table:
Aspect | Details |
---|---|
Definition | Vaporizes solid material in a vacuum to deposit a thin film on a substrate. |
Applications | Jewelry, automotive parts, medical tools, sporting goods, and more. |
Advantages | Durable, eco-friendly, versatile, and enhances product performance. |
Comparison | Non-toxic, thinner coatings, and better performance than chrome plating. |
Technical Features | Vacuum environment, reactive gases, and low-temperature processing. |
Interested in PVD coating for your products? Contact us today to learn more!