A reducing or oxidizing atmosphere refers to the chemical nature of a gaseous environment, particularly in terms of its ability to facilitate oxidation or reduction reactions. A reducing atmosphere is characterized by a lack of oxygen and the presence of reducing gases like hydrogen, carbon monoxide, or hydrogen sulfide, which prevent oxidation. Conversely, an oxidizing atmosphere contains abundant oxygen or other oxidizing agents, promoting oxidation reactions. These atmospheres are critical in various industrial processes, such as metallurgy, semiconductor manufacturing, and heat treatment, where controlling the chemical environment ensures desired material properties and prevents unwanted reactions.
Key Points Explained:
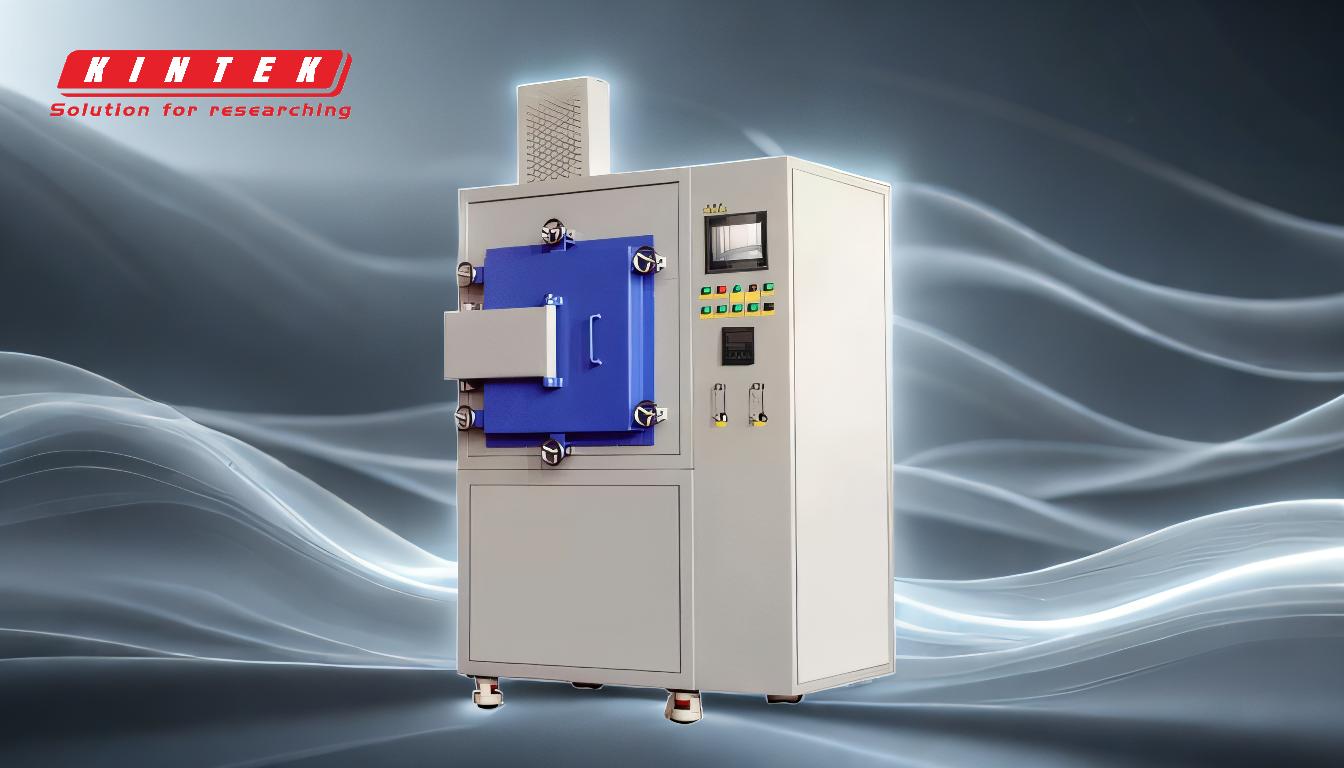
-
Definition of a Reducing Atmosphere:
- A reducing atmosphere is a gaseous environment where oxygen and other oxidizing gases are minimized or removed.
- It contains reducing agents such as hydrogen (H₂), carbon monoxide (CO), and hydrogen sulfide (H₂S), which donate electrons and prevent oxidation.
- Example: In metallurgical processes, a reducing atmosphere is used to extract metals from their ores by removing oxygen from metal oxides.
-
Definition of an Oxidizing Atmosphere:
- An oxidizing atmosphere is rich in oxygen or other oxidizing agents, promoting oxidation reactions.
- Oxidation involves the loss of electrons, often leading to the formation of oxides or other oxidized compounds.
- Example: Combustion processes, such as burning fuels, occur in an oxidizing atmosphere where oxygen reacts with hydrocarbons to produce carbon dioxide and water.
-
Key Differences Between Reducing and Oxidizing Atmospheres:
- Oxygen Content: A reducing atmosphere has low or no oxygen, while an oxidizing atmosphere has high oxygen levels.
- Chemical Reactions: Reducing atmospheres facilitate reduction (gain of electrons), whereas oxidizing atmospheres promote oxidation (loss of electrons).
- Applications: Reducing atmospheres are used in processes like annealing and metal refining, while oxidizing atmospheres are essential for combustion and chemical synthesis.
-
Industrial Applications of Reducing Atmospheres:
- Metallurgy: Used in the production of metals like iron and steel, where reducing gases remove oxygen from metal ores.
- Semiconductor Manufacturing: Prevents oxidation of silicon wafers during high-temperature processing.
- Heat Treatment: Protects metals from oxidation during annealing or sintering processes.
-
Industrial Applications of Oxidizing Atmospheres:
- Combustion Processes: Essential for burning fuels in engines, power plants, and industrial furnaces.
- Chemical Synthesis: Used in the production of chemicals like sulfuric acid and nitric acid, where oxidation reactions are required.
- Waste Incineration: Ensures complete combustion of waste materials to minimize harmful emissions.
-
Importance of Controlling Atmosphere in Industrial Processes:
- Material Properties: The atmosphere can significantly affect the mechanical, electrical, and chemical properties of materials.
- Reaction Control: Proper atmosphere control ensures desired chemical reactions occur while preventing unwanted side reactions.
- Energy Efficiency: Optimizing the atmosphere can reduce energy consumption and improve process efficiency.
-
Examples of Reducing and Oxidizing Gases:
- Reducing Gases: Hydrogen (H₂), carbon monoxide (CO), methane (CH₄), and hydrogen sulfide (H₂S).
- Oxidizing Gases: Oxygen (O₂), ozone (O₃), chlorine (Cl₂), and nitrogen dioxide (NO₂).
-
Safety Considerations:
- Reducing Atmospheres: Gases like hydrogen and carbon monoxide are flammable and toxic, requiring proper ventilation and monitoring.
- Oxidizing Atmospheres: High oxygen levels increase the risk of fire and explosions, necessitating careful handling and storage.
By understanding the principles of reducing and oxidizing atmospheres, industries can optimize processes, enhance material properties, and ensure safety in various applications.
Summary Table:
Aspect | Reducing Atmosphere | Oxidizing Atmosphere |
---|---|---|
Oxygen Content | Low or no oxygen | High oxygen levels |
Chemical Reactions | Facilitates reduction (gain of electrons) | Promotes oxidation (loss of electrons) |
Applications | Metallurgy, semiconductor manufacturing, annealing | Combustion, chemical synthesis, waste incineration |
Common Gases | Hydrogen (H₂), carbon monoxide (CO) | Oxygen (O₂), ozone (O₃) |
Safety Considerations | Flammable and toxic gases (e.g., H₂, CO) | High fire and explosion risks |
Need expert advice on optimizing your industrial processes with the right atmosphere? Contact us today to learn more!