A resistance furnace is an industrial heating device that utilizes electric current to generate heat, primarily through Joule heating, where electrical energy is converted into thermal energy. It is widely used across various industries, including ceramics, metallurgy, electronics, and chemical processing, for applications such as heat treatment, sintering, annealing, and material testing. Resistance furnaces are categorized into direct heating and indirect heating types, with the latter being more common. They operate across a wide temperature range, from medium (300°C–1,050°C) to high (1,050°C–1,350°C), depending on the application. These furnaces are versatile, efficient, and essential for processes requiring precise temperature control and uniform heating.
Key Points Explained:
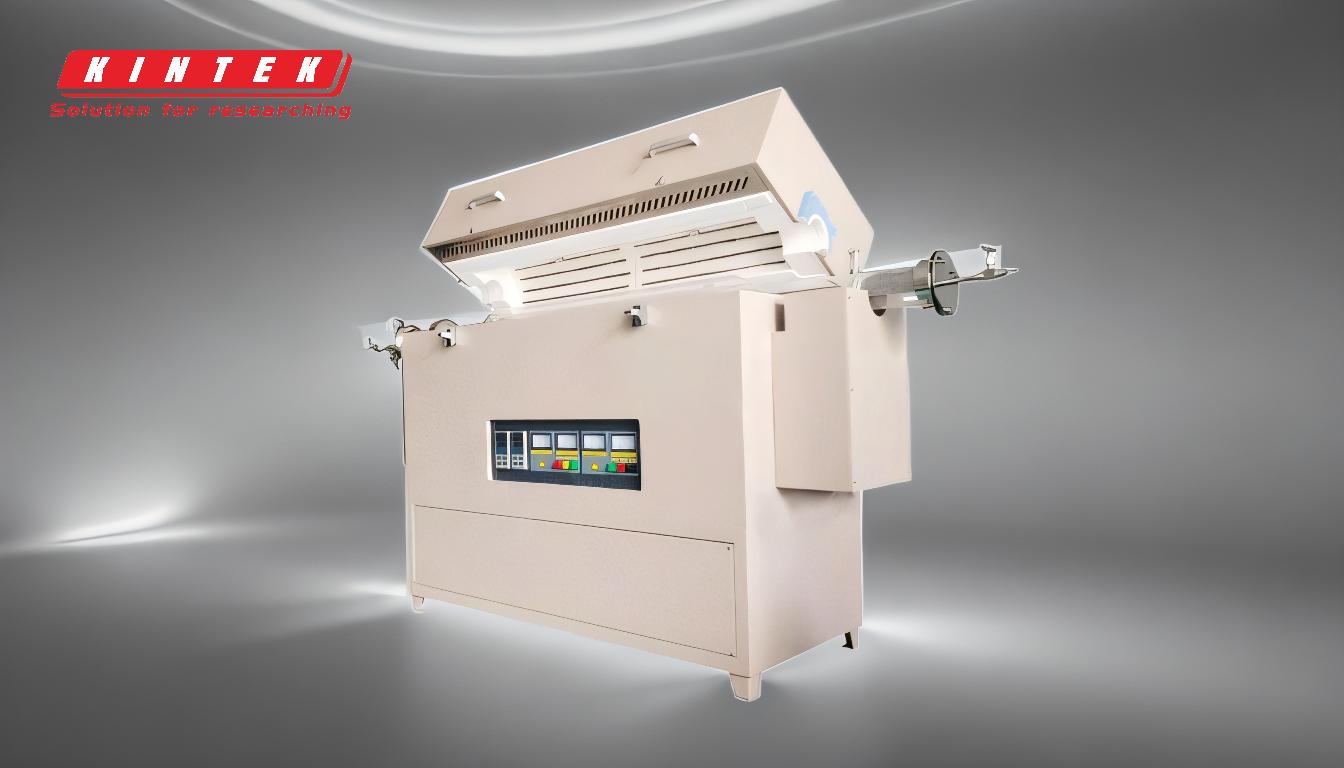
-
Definition and Working Principle:
- A resistance furnace is an electric furnace that generates heat by passing an electric current through a conductor, utilizing the Joule heating effect. The electrical energy is converted into heat energy, which is then used to heat materials or workpieces.
- In direct heating furnaces, the electric current flows directly through the material being heated, while in indirect heating furnaces, the current flows through a separate heating element or conductive medium, which then transfers heat to the material.
-
Types of Resistance Furnaces:
- Direct Heating Furnaces: These are less common and involve applying electric power directly to the material being heated. This method is typically used for conductive materials.
- Indirect Heating Furnaces: These are more prevalent and involve heating a separate element or medium, which then transfers heat to the material. This method is suitable for a wider range of materials and applications.
-
Temperature Ranges and Applications:
- Medium Temperature Furnaces (300°C–1,050°C): Used for processes such as annealing, normalizing, and melting of non-ferrous metals, as well as stove enamelling.
- High Temperature Furnaces (1,050°C–1,350°C): Employed for hardening applications and other high-temperature processes.
-
Applications Across Industries:
- Resistance furnaces are used in a variety of industries, including ceramics, metallurgy, electronics, glass, chemicals, machinery, refractories, and building materials.
- Specific applications include powder roasting, ceramic sintering, high-temperature experiments, material treatment, high-temperature atmosphere sintering, ceramic glue discharge, flue gas treatment, annealing, and sintering.
-
Specialized Types of Resistance Furnaces:
- Graphite Resistance Furnaces: These are specifically used in graphitization, heat treatment, sintering, and other high-temperature processes.
- Box Resistance Furnaces: These are used for heat treatment, production processes, and temperature testing of large parts and other products. They are widely applied in industries such as ceramics, metallurgy, electronics, and chemicals.
-
Design and Components:
- The furnace charge (material to be heated) can serve as the resistance element in some designs, with the heat-producing current introduced by electrodes buried in the metal.
- In other designs, resistance elements line the interior of the furnace, providing indirect heating to the material.
-
Advantages of Resistance Furnaces:
- Precise Temperature Control: Resistance furnaces offer excellent control over heating processes, ensuring uniform temperature distribution.
- Energy Efficiency: They convert electrical energy directly into heat with minimal losses, making them energy-efficient.
- Versatility: Suitable for a wide range of materials and applications, from low-temperature annealing to high-temperature sintering.
-
Considerations for Purchasers:
- Temperature Requirements: Choose a furnace that meets the specific temperature range required for your application.
- Heating Method: Decide between direct and indirect heating based on the material and process requirements.
- Furnace Size and Capacity: Ensure the furnace can accommodate the size and quantity of the materials to be processed.
- Industry-Specific Needs: Select a furnace designed for the specific industry and application, such as graphite resistance furnaces for high-temperature processes or box resistance furnaces for large parts.
By understanding these key points, purchasers can make informed decisions when selecting a resistance furnace that best meets their industrial and material processing needs.
Summary Table:
Aspect | Details |
---|---|
Definition | Industrial heating device using electric current to generate heat via Joule heating. |
Types | Direct heating (less common) and indirect heating (more common). |
Temperature Ranges | Medium (300°C–1,050°C) and high (1,050°C–1,350°C). |
Applications | Heat treatment, sintering, annealing, material testing, and more. |
Industries | Ceramics, metallurgy, electronics, chemicals, glass, and machinery. |
Advantages | Precise temperature control, energy efficiency, and versatility. |
Ready to find the perfect resistance furnace for your needs? Contact us today for expert guidance!