A sputtering machine is a versatile tool used primarily for depositing thin films of material onto a substrate. This process, known as sputter deposition, involves bombarding a target material with high-energy ions, causing atoms to be ejected and deposited onto a nearby surface. Sputtering machines are widely used across various industries, including semiconductors, electronics, optics, medical devices, and energy. They are essential for creating thin, uniform coatings that enhance the functionality, durability, and performance of products such as computer chips, solar panels, optical lenses, medical implants, and energy-efficient windows. The process is favored for its precision, ability to operate at low temperatures, and compatibility with a wide range of materials, including metals, ceramics, and alloys.
Key Points Explained:
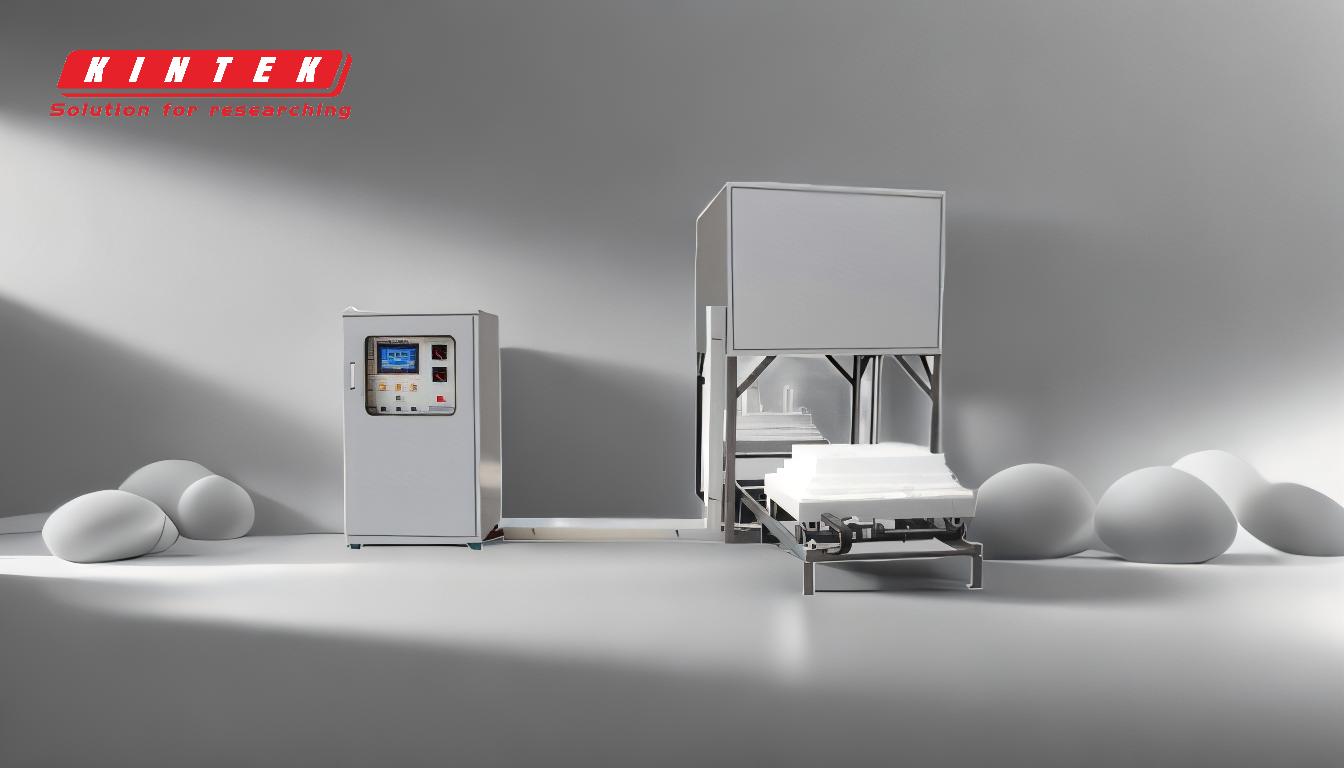
-
Thin Film Deposition:
- Sputtering machines are primarily used for depositing thin films onto substrates. This process involves accelerating ions from a source material (the target) onto a surface, creating a uniform coating. The thin films can be as thin as a few nanometers, making the process ideal for applications requiring precision and consistency.
-
Industries and Applications:
- Semiconductors and Electronics: Sputtering is crucial in the production of semiconductors and computer chips. It is used to deposit thin films of conductive and insulating materials onto silicon wafers, which are the building blocks of modern electronics.
- Optics: In the optical industry, sputtering is used to create coatings for lenses, mirrors, and other optical devices. These coatings can enhance light transmission, reduce glare, and improve durability.
- Medical Devices: Sputtering is employed in the medical industry to create biocompatible coatings on implants and surgical tools. These coatings can improve the performance and longevity of medical devices.
- Energy: Sputtering is used in the production of solar panels and energy-efficient windows. Thin films deposited by sputtering can enhance the efficiency of solar cells and improve the insulation properties of windows.
- Consumer Electronics: Sputtering is used in the manufacturing of CDs, DVDs, and LED displays. The process ensures that the thin films are uniform and free of defects, which is critical for the performance of these devices.
-
Materials Used:
- Sputtering targets can be made from a variety of materials, including metals, alloys, and ceramics. Common materials include gold, silver, aluminum, and titanium. These materials are chosen based on the desired properties of the thin film, such as conductivity, reflectivity, or hardness.
-
Advantages of Sputtering:
- Low Temperature Operation: Unlike other deposition methods, sputtering can be performed at low temperatures, making it suitable for temperature-sensitive substrates.
- Uniform Coatings: Sputtering produces highly uniform coatings, which are essential for applications requiring precise thickness and consistency.
- Versatility: Sputtering can be used with a wide range of materials, including metals, ceramics, and alloys, making it a versatile tool for various industries.
-
Types of Sputtering:
- DC Magnetron Sputtering: This is the most common type of sputtering, used in industries such as optics, semiconductors, and energy. It involves using a magnetic field to enhance the sputtering process, resulting in higher deposition rates and better film quality.
- RF Sputtering: This type of sputtering is used for insulating materials, where a radio frequency (RF) power source is used to create the plasma needed for sputtering.
- Reactive Sputtering: In this process, a reactive gas is introduced into the sputtering chamber, allowing the deposition of compound films such as oxides, nitrides, and carbides.
-
Specific Applications:
- Gold Sputtering: Gold is commonly used in the electronics industry for creating conductive coatings on circuit boards and in the preparation of specimens for scanning electron microscopy.
- Ceramic Sputtering: Ceramic targets are used to create hardened coatings for tools and other applications requiring wear resistance.
- Optical Coatings: Sputtering is used to create anti-reflective coatings, mirrors, and filters for optical devices.
In summary, sputtering machines are indispensable tools in modern manufacturing, enabling the creation of thin, precise coatings that enhance the performance and durability of a wide range of products. Their versatility, precision, and ability to operate at low temperatures make them suitable for a variety of industries, from semiconductors to medical devices.
Summary Table:
Key Aspect | Details |
---|---|
Primary Use | Depositing thin films onto substrates for precision applications. |
Industries | Semiconductors, optics, medical devices, energy, consumer electronics. |
Materials Used | Metals (gold, silver), alloys, ceramics. |
Advantages | Low-temperature operation, uniform coatings, material versatility. |
Types of Sputtering | DC Magnetron, RF, Reactive. |
Applications | Solar panels, optical lenses, medical implants, LED displays, and more. |
Interested in how a sputtering machine can benefit your industry? Contact us today for expert advice!