A temperature control system for digital applications is a sophisticated setup designed to maintain precise temperature levels in various environments, crucial for the optimal performance of digital devices and processes. These systems integrate advanced technologies such as PID controllers, thermocouples, and solid-state relays to ensure accurate temperature regulation. They are widely used in industries like semiconductor manufacturing, medical equipment, and data centers, where even minor temperature fluctuations can significantly impact performance and reliability. The system's ability to provide real-time monitoring, precise control, and adaptive responses to environmental changes makes it indispensable in maintaining the integrity and efficiency of digital applications.
Key Points Explained:
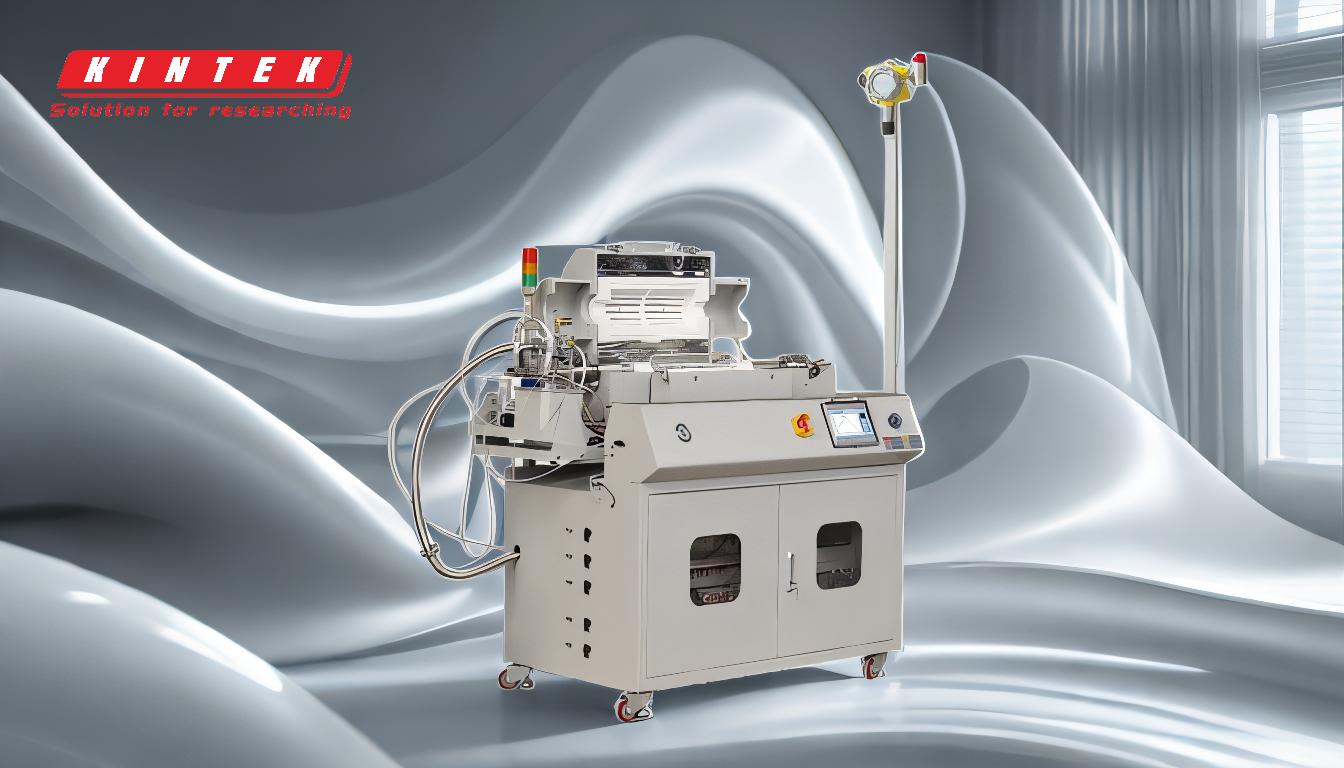
1. Definition and Purpose
- Temperature Control System: A system designed to regulate and maintain a specific temperature within a defined environment.
- Digital Applications: These include environments where digital devices operate, such as data centers, semiconductor fabrication, and medical equipment.
- Purpose: To ensure that digital devices operate within their optimal temperature range, preventing overheating or undercooling that could lead to performance degradation or failure.
2. Key Components
- PID Controllers: Proportional-Integral-Derivative controllers are used to maintain the desired temperature by continuously adjusting the control inputs based on the difference between the setpoint and the actual temperature.
- Thermocouples: Sensors that measure temperature by detecting changes in voltage caused by temperature differences.
- Solid-State Relays: Devices that switch power on and off without moving parts, used to control heating elements or cooling systems.
- Digital Interfaces: Allow for real-time monitoring and control through software, enabling precise adjustments and data logging.
3. How It Works
- Temperature Sensing: Thermocouples or other sensors continuously monitor the temperature of the environment or device.
- Feedback Loop: The PID controller receives data from the sensors and calculates the necessary adjustments to maintain the setpoint.
- Control Actions: The controller sends signals to solid-state relays to activate heating or cooling systems as needed.
- Adaptive Response: The system can adapt to environmental changes, such as fluctuations in ambient temperature or changes in device load, to maintain stability.
4. Applications
- Semiconductor Manufacturing: Precise temperature control is critical in processes like photolithography and chemical vapor deposition.
- Data Centers: Maintaining optimal temperatures ensures the reliability and longevity of servers and other critical infrastructure.
- Medical Equipment: Devices like MRI machines and laboratory incubators require stable temperatures to function correctly.
- Consumer Electronics: Smartphones, laptops, and other devices benefit from temperature management to prevent overheating and extend lifespan.
5. Advantages
- Precision: High accuracy in maintaining the desired temperature, essential for sensitive digital applications.
- Efficiency: Reduces energy consumption by optimizing heating and cooling cycles.
- Reliability: Minimizes the risk of device failure due to temperature extremes.
- Scalability: Can be adapted for various scales, from small devices to large industrial environments.
6. Challenges and Considerations
- Complexity: Designing and implementing a temperature control system requires expertise in both hardware and software.
- Cost: High-quality components and sophisticated control algorithms can be expensive.
- Maintenance: Regular calibration and maintenance are necessary to ensure long-term accuracy and reliability.
- Integration: Ensuring compatibility with existing systems and devices can be challenging.
7. Future Trends
- IoT Integration: Incorporating Internet of Things (IoT) technology for remote monitoring and control.
- AI and Machine Learning: Using advanced algorithms to predict and adapt to temperature changes more effectively.
- Energy Efficiency: Developing more energy-efficient components and control strategies to reduce environmental impact.
- Miniaturization: Creating smaller, more compact systems for use in portable and wearable digital devices.
By understanding these key points, one can appreciate the critical role that temperature control systems play in ensuring the reliability and efficiency of digital applications across various industries.
Summary Table:
Key Aspect | Details |
---|---|
Purpose | Regulates temperature to prevent overheating or undercooling in digital devices. |
Key Components | PID controllers, thermocouples, solid-state relays, digital interfaces. |
How It Works | Sensors monitor temperature; PID controllers adjust heating/cooling systems. |
Applications | Semiconductor manufacturing, data centers, medical equipment, consumer electronics. |
Advantages | Precision, efficiency, reliability, scalability. |
Challenges | Complexity, cost, maintenance, integration. |
Future Trends | IoT integration, AI, energy efficiency, miniaturization. |
Discover how a temperature control system can optimize your digital applications—contact our experts today!