A thick film circuit is a type of electronic circuit that is created by depositing layers of conductive, resistive, and insulating materials onto a substrate, typically ceramic or glass. These layers are much thicker than those used in thin film circuits, often ranging from several micrometers to tens of micrometers. Thick film circuits are widely used in various applications, including hybrid microelectronics, sensors, and passive components, due to their cost-effectiveness, durability, and ability to be customized for specific needs.
Key Points Explained:
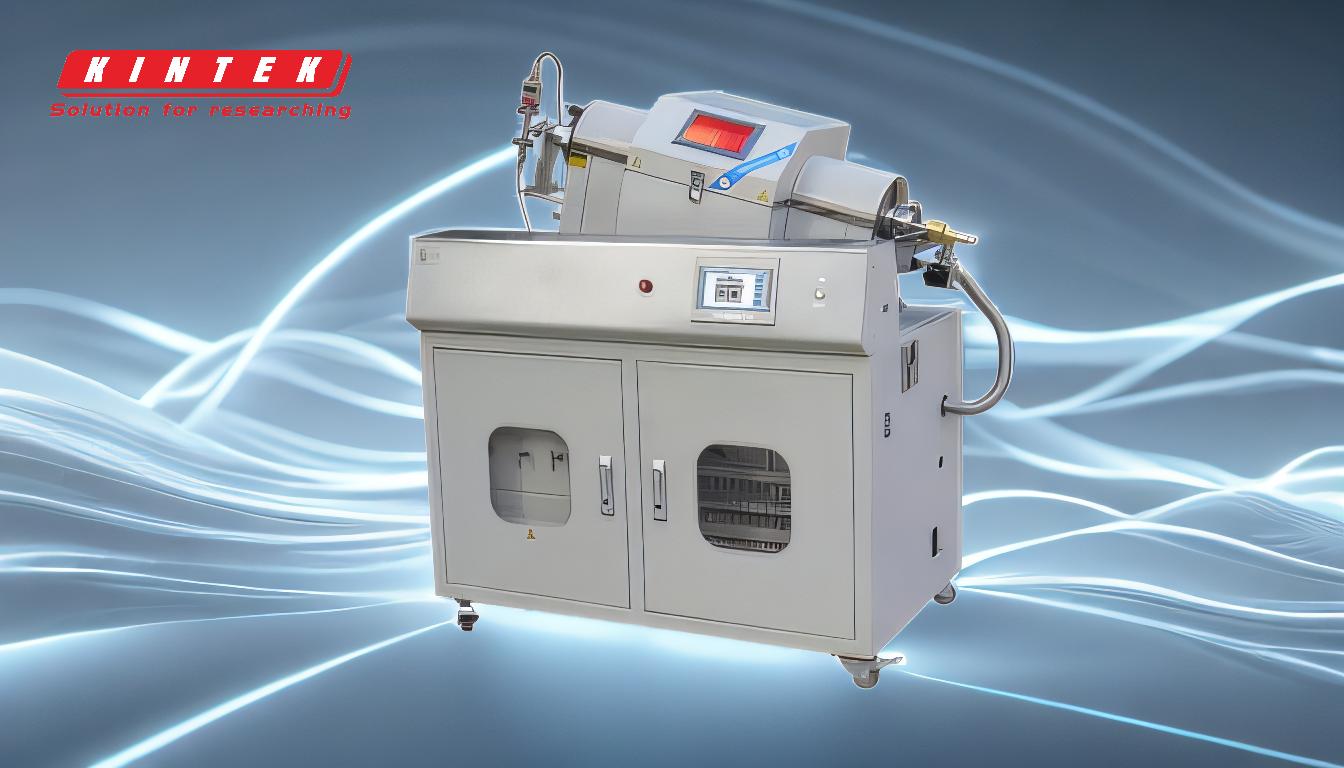
-
Definition and Composition of Thick Film Circuits:
- Thick film circuits are constructed by screen-printing or depositing layers of conductive, resistive, and insulating materials onto a substrate. The materials used include conductive pastes (e.g., silver, gold), resistive pastes (e.g., ruthenium oxide), and dielectric pastes.
- These layers are significantly thicker than those in thin film circuits, often exceeding several micrometers in thickness.
-
Manufacturing Process:
- The primary method for creating thick film circuits is screen printing, where a patterned stencil is used to apply the conductive, resistive, and insulating pastes onto the substrate.
- After printing, the substrate is fired in a high-temperature furnace to sinter the materials, ensuring good adhesion and electrical properties.
-
Applications of Thick Film Circuits:
- Hybrid Microelectronics: Thick film circuits are commonly used in hybrid microelectronics, where they integrate with other components to form complete electronic systems.
- Sensors: They are used in various sensors, such as temperature sensors, pressure sensors, and gas sensors, due to their ability to be customized for specific sensing requirements.
- Passive Components: Thick film technology is used to manufacture passive components like resistors, capacitors, and inductors.
-
Advantages of Thick Film Circuits:
- Cost-Effectiveness: Thick film circuits are generally less expensive to produce than thin film circuits, making them suitable for high-volume production.
- Durability: The thicker layers provide better mechanical strength and durability, making them suitable for harsh environments.
- Customizability: The screen-printing process allows for easy customization of the circuit design, making it ideal for specialized applications.
-
Comparison with Thin Film Circuits:
- Thickness: Thick film circuits have much thicker layers (micrometers to tens of micrometers) compared to thin film circuits, which have layers ranging from a fraction of a nanometer to one micron.
- Deposition Method: Thin film deposition involves the deposition of individual atoms or molecules, while thick film deposition involves the deposition of particles.
- Applications: Thin film circuits are often used in applications requiring high precision and miniaturization, such as semiconductor devices, whereas thick film circuits are used in applications where cost, durability, and customizability are more important.
-
Future Trends and Developments:
- Advanced Materials: Research is ongoing to develop new materials for thick film circuits that offer improved electrical and thermal properties.
- Integration with Other Technologies: There is a growing trend towards integrating thick film circuits with other technologies, such as flexible electronics and printed electronics, to create more versatile and innovative products.
In summary, thick film circuits are a versatile and cost-effective solution for a wide range of electronic applications. Their ability to be customized, combined with their durability and cost-effectiveness, makes them a popular choice in industries ranging from consumer electronics to industrial sensors.
Summary Table:
Aspect | Details |
---|---|
Definition | Electronic circuits with thick layers of conductive, resistive, and insulating materials. |
Manufacturing Process | Screen-printing and high-temperature firing of materials onto substrates. |
Applications | Hybrid microelectronics, sensors, and passive components. |
Advantages | Cost-effective, durable, and highly customizable. |
Comparison | Thicker layers than thin film circuits, better for harsh environments. |
Interested in how thick film circuits can benefit your projects? Contact us today to learn more!