Sputtering, a modern vacuum deposition technique, offers several advantages over older methods like thermal evaporation or E-beam evaporation. Key benefits include the ability to deposit a wide range of materials (including those with high melting points), precise control over film composition and properties, better adhesion due to higher kinetic energy of sputtered atoms, and compatibility with reactive gases for advanced processes. Additionally, sputtering is more reproducible, easier to automate, and suitable for ultrahigh vacuum applications. It also allows for molecular-level precision, enabling the creation of pristine interfaces and uniform films with high packing densities, even at low temperatures.
Key Points Explained:
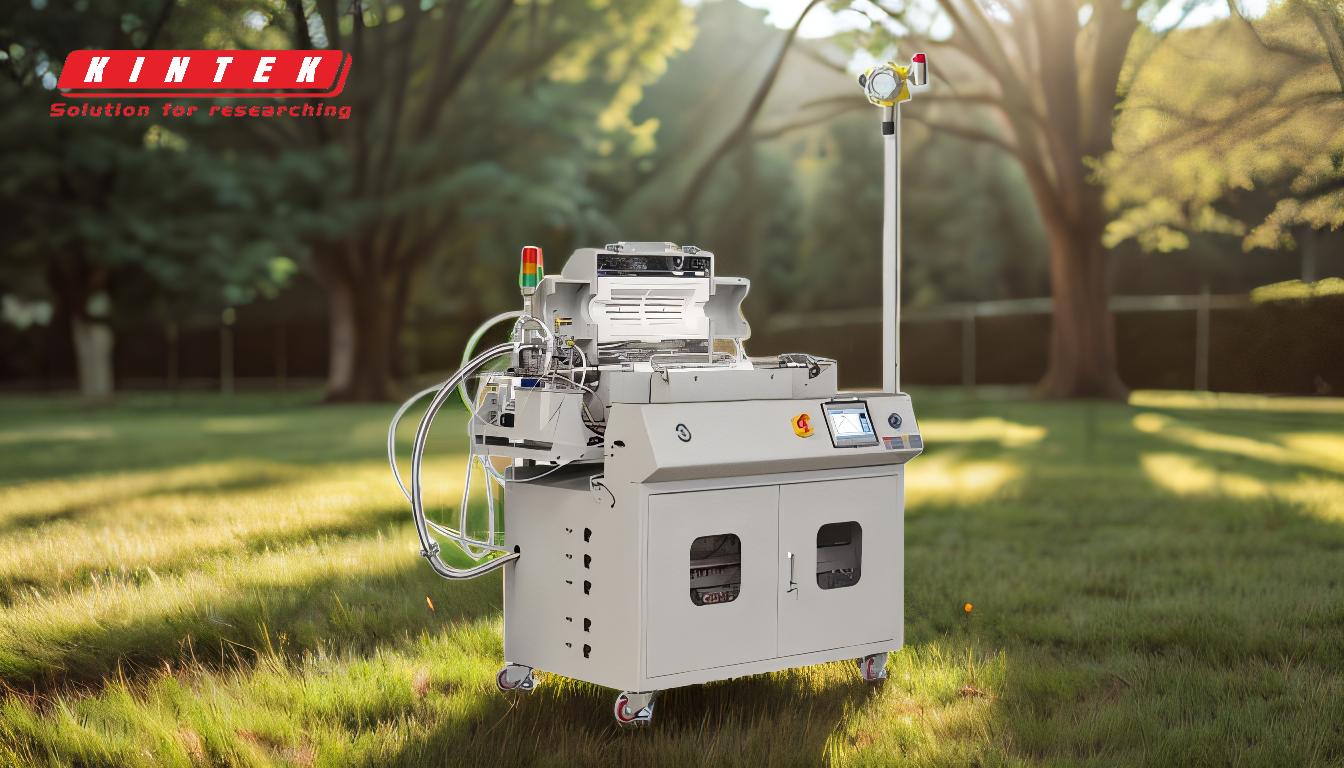
-
Deposition of a Wide Range of Materials:
- Sputtering can deposit materials with very high melting points, which are difficult or impossible to evaporate using older methods like thermal evaporation.
- It works well with diverse materials, including metals, alloys, compounds, plastics, organics, and glass, making it more versatile than traditional vacuum deposition techniques.
-
Better Adhesion and Film Quality:
- Sputter-ejected atoms have significantly higher kinetic energy compared to evaporated materials, resulting in better adhesion to substrates.
- Films produced by sputtering are more uniform, have higher packing densities, and exhibit better surface adhesion, even at low temperatures.
-
Precision and Control:
- Sputtering offers molecular-level precision, allowing for the creation of pristine interfaces between materials.
- Film properties can be precisely tuned by controlling process parameters, such as gas composition, pressure, and power.
-
Reproducibility and Automation:
- Sputter deposition is highly reproducible and easier to automate compared to older methods like E-beam or thermal evaporation.
- The sputtering target provides a stable, long-lived vaporization source, ensuring consistent results over time.
-
Reactive Deposition and Advanced Processes:
- Reactive deposition is easily accomplished using reactive gaseous species activated in plasma, enabling the formation of oxide or nitride films with desired compositions.
- Sputtering is compatible with advanced processes like epitaxial growth and can be performed in ultrahigh vacuum conditions.
-
Cost-Effectiveness and Maintenance:
- Sputter deposition is relatively inexpensive compared to other deposition processes.
- The process is maintenance-free, reducing operational costs and downtime.
-
Compact and Flexible Setup:
- The sputter deposition chamber can have a small volume, and the source and substrate can be spaced close together, minimizing radiant heat and simplifying the setup.
- The sputtering target can be shaped (e.g., line, rod, or cylinder) to suit specific applications.
-
Broad Material Compatibility:
- Sputtering works well with a broader range of materials, including mixtures and alloys, compared to methods like thermal evaporation.
- It is suitable for depositing optical films by oxidizing or nitriding sputtered metal ions to achieve desired film compositions.
By leveraging these advantages, sputtering has become a preferred method for modern vacuum deposition, offering superior performance, flexibility, and cost-effectiveness compared to older techniques.
Summary Table:
Advantage | Description |
---|---|
Wide Range of Materials | Deposits materials with high melting points, metals, alloys, compounds, and more. |
Better Adhesion & Film Quality | Higher kinetic energy ensures uniform films with excellent adhesion. |
Precision & Control | Molecular-level precision for pristine interfaces and tunable film properties. |
Reproducibility & Automation | Highly reproducible, easy to automate, and consistent over time. |
Reactive Deposition | Compatible with reactive gases for oxide/nitride films and advanced processes. |
Cost-Effectiveness | Relatively inexpensive and maintenance-free. |
Compact & Flexible Setup | Small chamber size, minimal radiant heat, and customizable target shapes. |
Broad Material Compatibility | Works with mixtures, alloys, and optical films for diverse applications. |
Ready to enhance your deposition process? Contact us today to learn more about sputtering solutions!