Chemical vapor deposition (CVD) is a versatile and widely used technique for depositing thin films of materials onto substrates through chemical reactions in the vapor phase. One prominent example of CVD is plasma-enhanced chemical vapor deposition (PECVD), which is commonly used in the semiconductor industry to deposit silicon dioxide (SiO₂) and silicon nitride (Si₃N₄) films. PECVD utilizes plasma to lower the temperature required for the chemical reactions, making it suitable for temperature-sensitive substrates. This process involves introducing precursor gases into a reaction chamber, where they are ionized by plasma, leading to the formation of thin films on the substrate. CVD techniques, including PECVD, are critical for applications such as microelectronics, optics, and protective coatings.
Key Points Explained:
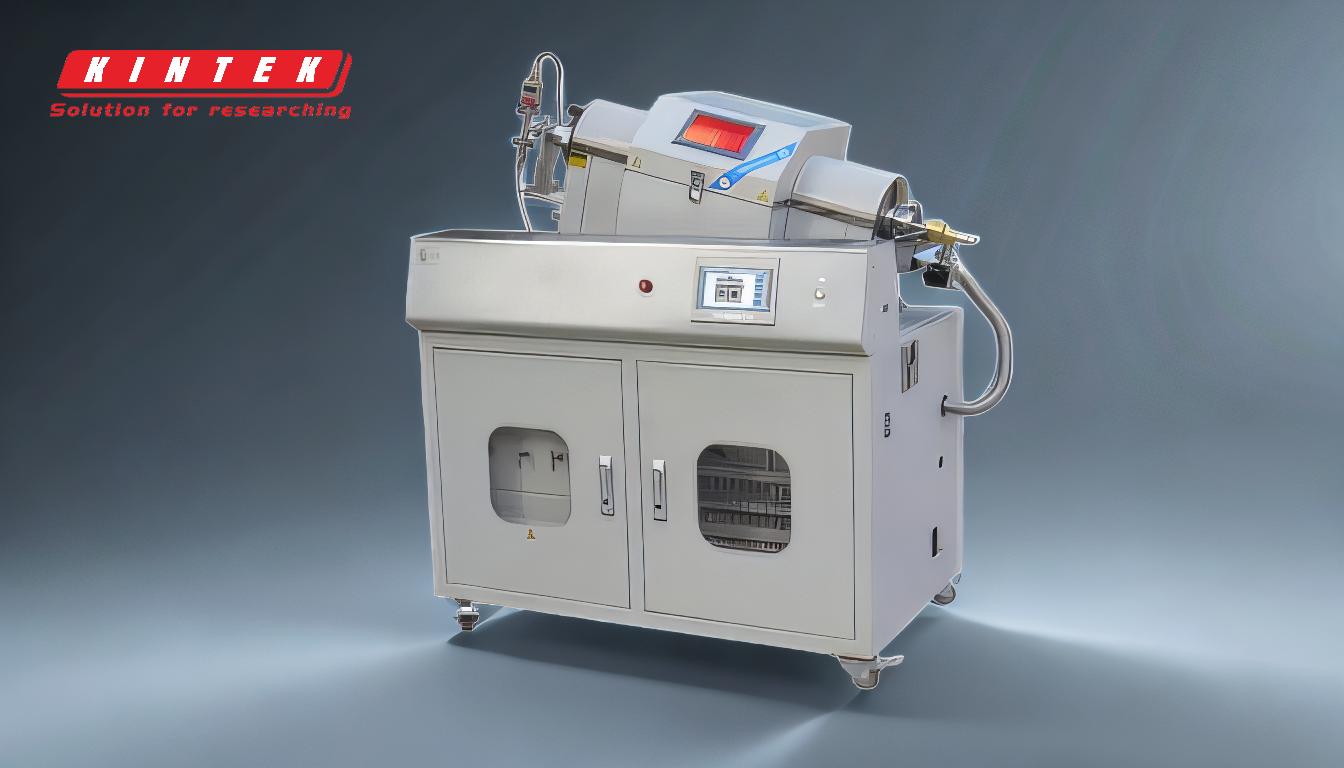
-
Definition and Purpose of CVD:
- Chemical vapor deposition (CVD) is a process used to deposit thin films of materials onto a substrate through chemical reactions involving gaseous precursors.
- The purpose of CVD is to create high-quality, uniform coatings or films with precise control over thickness and composition. This makes it essential for industries like semiconductors, optics, and energy storage.
-
Types of CVD:
- Plasma-Enhanced Chemical Vapor Deposition (PECVD): Uses plasma to enable chemical reactions at lower temperatures, ideal for temperature-sensitive substrates.
- Thermal Chemical Vapor Deposition: Relies on heat to drive the chemical reactions.
- Metalorganic Chemical Vapor Deposition (MOCVD): Uses metalorganic compounds as precursors, often for depositing compound semiconductors.
- Laser Chemical Vapor Deposition: Utilizes laser energy to initiate and control the deposition process.
- Aerosol-Assisted Chemical Vapor Deposition: Employs aerosolized precursors for deposition.
- Direct Liquid Injection CVD: Involves injecting liquid precursors into a heated chamber for vaporization and reaction.
-
Steps in the CVD Process:
- Transport of Gaseous Species: Precursor gases are introduced into the reaction chamber and transported to the substrate surface.
- Adsorption: The gaseous species adsorb onto the substrate surface.
- Surface Reactions: Chemical reactions occur on the substrate surface, often catalyzed by heat or plasma.
- Nucleation and Growth: The reaction products form nuclei that grow into a continuous thin film.
- Desorption and Transport of Byproducts: Gaseous byproducts are desorbed from the surface and removed from the chamber.
-
Key Parameters in CVD:
- Chamber Pressure: Affects the rate and uniformity of deposition.
- Substrate Temperature: Influences the kinetics of surface reactions and film quality.
- Precursor Selection: Determines the composition and properties of the deposited film.
- Deposition Technology: Techniques like PECVD, ALD, and APCVD offer different advantages depending on the application.
-
Applications of CVD:
- Semiconductors: Used to deposit dielectric layers (e.g., SiO₂, Si₃N₄) and conductive films (e.g., polysilicon, tungsten).
- Optics: Creates anti-reflective coatings and optical filters.
- Protective Coatings: Deposits wear-resistant and corrosion-resistant layers on tools and components.
- Energy: Used in the fabrication of solar cells and batteries.
-
Advantages of CVD:
- High-quality, uniform films with excellent adhesion.
- Ability to deposit a wide range of materials, including metals, semiconductors, and ceramics.
- Scalability for industrial production.
-
Challenges in CVD:
- High equipment and operational costs.
- Complexity in controlling process parameters.
- Potential for hazardous byproducts, requiring proper safety measures.
By understanding these key points, a purchaser of CVD equipment or consumables can make informed decisions about the type of CVD system and precursors needed for their specific application. For example, if the goal is to deposit thin films on temperature-sensitive substrates, PECVD would be a suitable choice due to its lower temperature requirements.
Summary Table:
Aspect | Details |
---|---|
Example of CVD | Plasma-Enhanced Chemical Vapor Deposition (PECVD) |
Key Features | Uses plasma for lower temperature reactions, ideal for sensitive substrates |
Applications | Semiconductors, optics, protective coatings, energy storage |
Advantages | High-quality, uniform films; scalable for industrial production |
Challenges | High costs, complex parameter control, potential hazardous byproducts |
Discover how PECVD can enhance your thin film processes—contact us today for expert guidance!