Physical Vapor Deposition (PVD) is a versatile technique used to create thin, durable, and high-performance coatings on various materials. One of the most common examples of PVD is electron-beam (e-beam) evaporation, which is widely used in industries such as aerospace, semiconductors, and optics. This method involves using an electron beam to heat and vaporize a source material, which then condenses onto a substrate to form a thin film. E-beam evaporation is particularly valued for its ability to produce dense, temperature-resistant coatings and optical films, making it ideal for applications in extreme environments. Other examples of PVD include sputtering and thermal evaporation, each with unique processes and applications.
Key Points Explained:
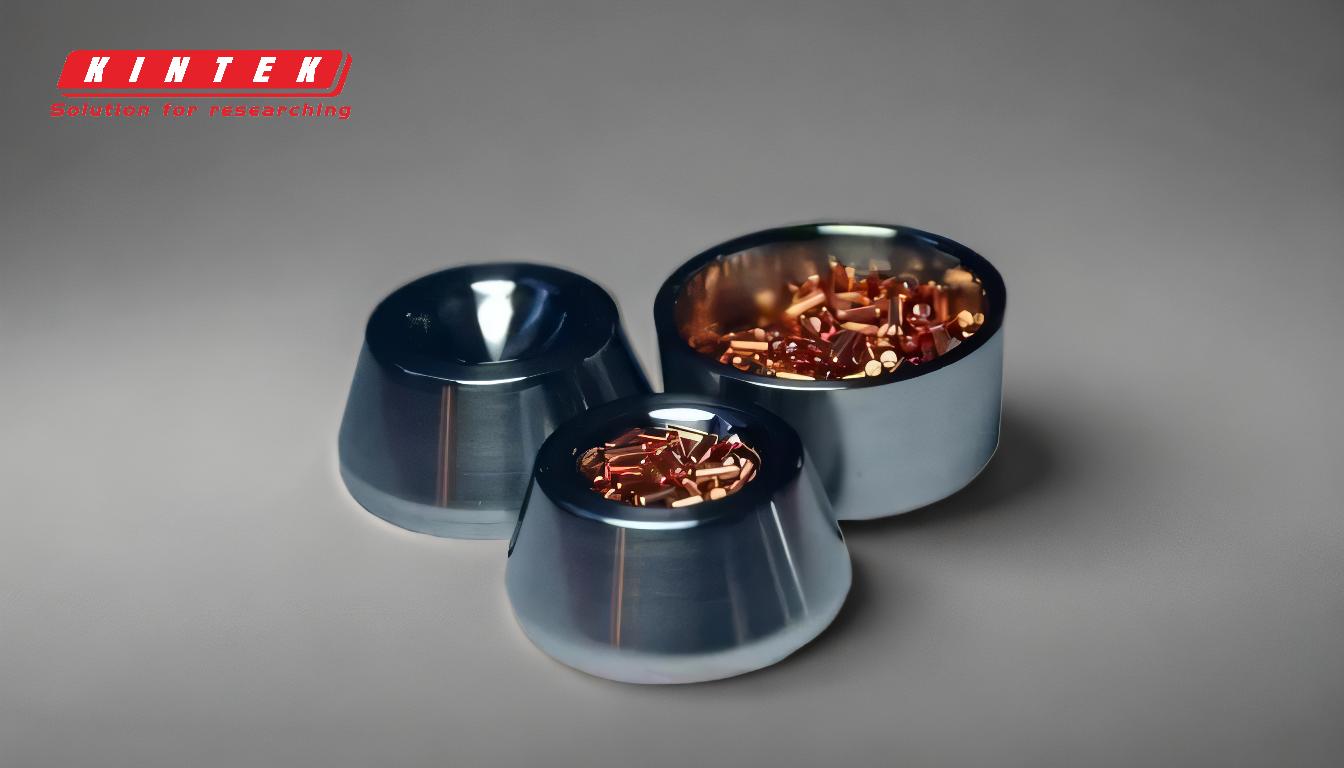
-
What is Physical Vapor Deposition (PVD)?
- PVD is a process used to deposit thin films of material onto a substrate by physically vaporizing a source material and allowing it to condense on a surface. This method is widely used to create coatings that are hard, durable, and resistant to wear, corrosion, and extreme temperatures.
- The process occurs in a vacuum environment to ensure the purity and quality of the deposited film.
-
Common PVD Techniques:
- Sputtering: A technique where high-energy ions bombard a target material, causing atoms to be ejected and deposited onto a substrate. This method is commonly used for creating semiconductor devices, optical coatings, and wear-resistant coatings.
- Thermal Evaporation: Involves heating a material in a vacuum until it vaporizes, and then depositing the vapor onto a substrate. This method is often used for creating reflective coatings and thin films in optical applications.
- Electron-Beam (e-beam) Evaporation: A specialized form of thermal evaporation where an electron beam is used to heat and vaporize the source material. This method is preferred for applications requiring high-purity and dense coatings, such as aerospace components and solar panels.
-
Example of PVD: Electron-Beam Evaporation
- Process: In e-beam evaporation, an electron beam is directed at a source material in a vacuum chamber. The intense heat generated by the beam vaporizes the material, which then condenses onto a substrate to form a thin film.
-
Applications:
- Aerospace: Used to apply temperature-resistant coatings on components, enhancing their ability to withstand extreme conditions.
- Optics: Applied to create highly reflective films for mirrors, lenses, and solar panels.
- Semiconductors: Used to deposit thin films for electronic devices, improving performance and durability.
-
Advantages of E-Beam Evaporation:
- High Purity: The vacuum environment and precise control of the electron beam ensure minimal contamination of the deposited film.
- Dense Coatings: The high energy of the process results in dense, adherent films that are resistant to wear and corrosion.
- Versatility: Suitable for a wide range of materials, including metals, ceramics, and compounds.
-
Other PVD Techniques and Their Uses:
- Sputtering: Commonly used in the production of semiconductor devices, optical coatings, and hard coatings for cutting tools.
- Thermal Evaporation: Ideal for creating reflective coatings, such as those used in mirrors and decorative finishes.
- Pulsed Laser Deposition (PLD): Used for depositing complex materials, such as superconductors and thin films for research purposes.
-
Industrial Applications of PVD:
- Aerospace: PVD coatings are applied to components to enhance their resistance to high temperatures, wear, and corrosion, ensuring durability in extreme environments.
- Electronics: Used to deposit thin films for semiconductors, improving the performance and longevity of electronic devices.
- Optics: PVD is used to create optical films for lenses, mirrors, and solar panels, enhancing their reflectivity and efficiency.
- Tooling: Hard coatings are applied to cutting tools and molds to increase their lifespan and performance in demanding applications.
-
Why PVD is Preferred in Certain Applications:
- Durability: PVD coatings are known for their hardness and resistance to wear, making them ideal for tools and components subjected to harsh conditions.
- Precision: The ability to control the deposition process at the atomic level allows for the creation of highly uniform and precise coatings.
- Material Compatibility: PVD can be used with a wide range of materials, including metals, ceramics, and polymers, making it a versatile solution for various industries.
By understanding these key points, it becomes clear why PVD, and specifically e-beam evaporation, is a critical technology in modern manufacturing and materials science. Its ability to produce high-performance coatings makes it indispensable in industries where durability, precision, and resistance to extreme conditions are paramount.
Summary Table:
PVD Technique | Key Features | Applications |
---|---|---|
E-Beam Evaporation | High-purity, dense coatings; vacuum environment; precise control | Aerospace (temperature-resistant coatings), optics (reflective films), semiconductors |
Sputtering | High-energy ions bombard target material; uniform deposition | Semiconductor devices, optical coatings, wear-resistant coatings |
Thermal Evaporation | Heating material in vacuum; simple and cost-effective | Reflective coatings, thin films for optical applications |
Pulsed Laser Deposition (PLD) | Deposits complex materials; high precision | Superconductors, thin films for research purposes |
Discover how PVD can enhance your industrial applications—contact our experts today!